Die casting, a pivotal manufacturing process, plays an essential role in creating precise metal parts by injecting molten metal into a mold cavity under high pressure. One critical aspect of die casting that often draws considerable attention is the minimum wall thickness achievable. Understanding this facet not only contributes to cost efficiency but also enhances the mechanical properties of the final product.
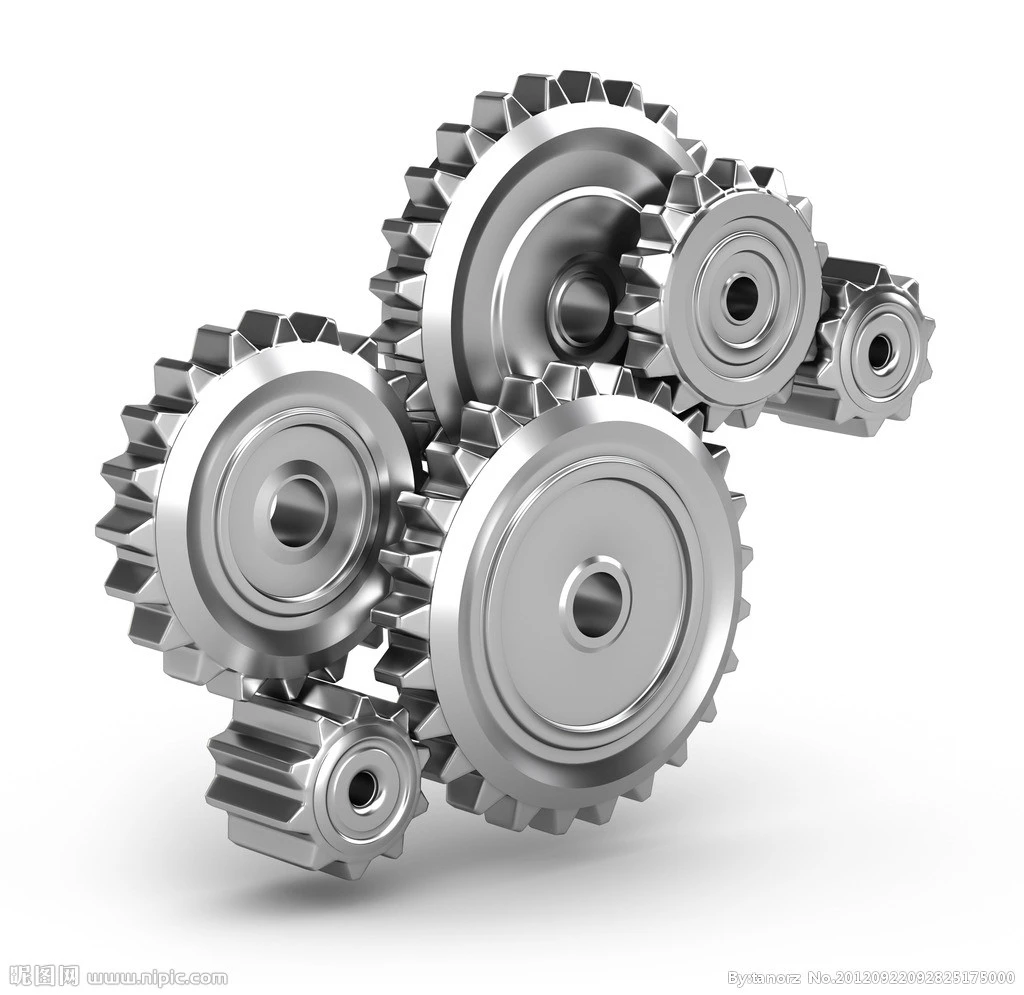
Achieving optimal wall thickness in die casting is a delicate balancing act involving material properties, mold design, and casting parameters. To initiate with, aluminum, magnesium, and zinc are the most commonly used metals due to their favorable properties in casting thin-walled components. Among these, zinc allows for the thinnest walls, often as thin as 0.25mm, owing to its excellent fluidity and low melting point.
The advantages of thinner walls are multifaceted. Firstly, they lead to reduced material usage, which directly translates into cost savings. Moreover, lighter parts result in decreased shipment costs and enhanced energy efficiency in applications such as automotive components. However, these benefits can only be realized if the structural integrity of the part is maintained.
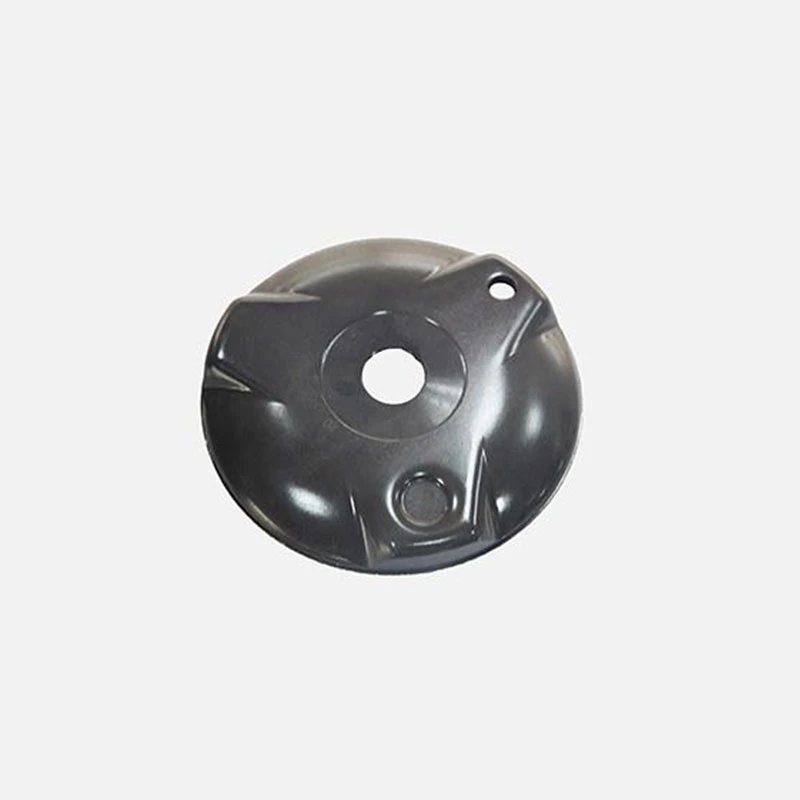
Mold design plays a pivotal role in achieving minimum wall thickness. Precise engineering of the mold includes accommodating sufficient draft angles and maintaining consistent wall thickness throughout. Uneven or excessive wall thickness can lead to defects such as warping or shrinkage. Advanced simulation software assists engineers in predicting and refining the ideal wall thickness during the mold design process.
Injection parameters like temperature and pressure must be meticulously controlled. Higher temperatures improve metal fluidity, allowing for thinner walls, yet pose a risk of metal-mold reaction, leading to defects. Similarly, increased pressure ensures the metal fills the mold completely but can lead to flash defects if the mold is not adequately secured.
die casting minimum wall thickness
The minimum wall thickness also hinges on the die casting technique employed. High-pressure die casting is prevalent for creating thin-walled sections due to its ability to produce parts at high speed with excellent surface finish and dimensional accuracy. Conversely, gravity die casting, while more cost-effective, may not achieve the same degree of thinness due to its slower casting speeds and lower pressure.
During the die casting process, ensuring consistent wall thickness becomes crucial for the part's performance and durability. Even minor inconsistencies can result in weak points that are susceptible to stress concentration or premature failure. Regular inspections and quality control measures such as X-ray testing or CT scanning help detect any internal defects before they manifest in the final product.
Innovation in die casting technology continues to push the boundaries of what is achievable in terms of wall thickness. Recent advancements in alloys and casting techniques have enabled manufacturers to produce parts with unprecedented thinness without compromising on strength or durability. Additionally, collaborative efforts with industries such as automotive and electronics are fueling research into new materials and processes that promise even greater reductions in wall thickness.
To summarize, the pursuit of minimum wall thickness in die casting is a testament to the intricate synergy between material science, engineering, and technology. The ability to cast extremely thin walls without sacrificing part performance or structural integrity remains a prized capability in the manufacturing industry. By staying informed about the latest advancements and applying best practices in design and process control, manufacturers can effectively capitalize on the numerous benefits that optimal wall thickness offers. This not only ensures high-quality parts but also contributes to sustainable and economically viable manufacturing solutions.