Understanding the intricate world of stamping car parts provides a unique vantage point to explore this indispensable manufacturing process that drives the automotive industry. At its core, stamping is a sophisticated technique transforming flat metal sheets into precise and complex car parts through a series of processes such as blanking, bending, punching, and embossing. The art and science of stamping car parts have evolved over the decades, rendering it not just as a vital operation, but a reflection of technological and engineering advancements.
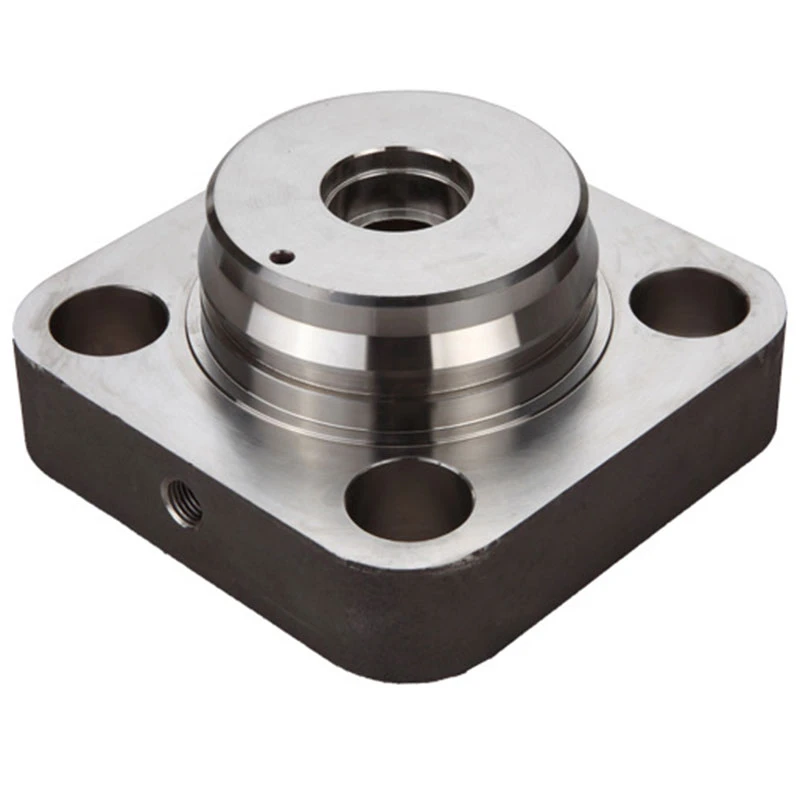
The automotive industry heavily relies on the stamping process due to its efficiency, cost-effectiveness, and precision. Major components such as body panels, chassis parts, brackets, and even structural reinforcements come to life through stamping. No other method provides the scalability and replicability required to meet the global demands of automakers.
One of the most compelling aspects of stamping is its ability to adapt to various materials. Where once steel was the mainstay, modern stamping now accommodates lightweight and stronger materials like aluminum and advanced high-strength steels. The shift towards lightweight materials helps manufacturers meet stringent fuel efficiency and emission standards without compromising safety or performance. Stamping processes must therefore align with these material properties to maintain optimal durability and design integrity.
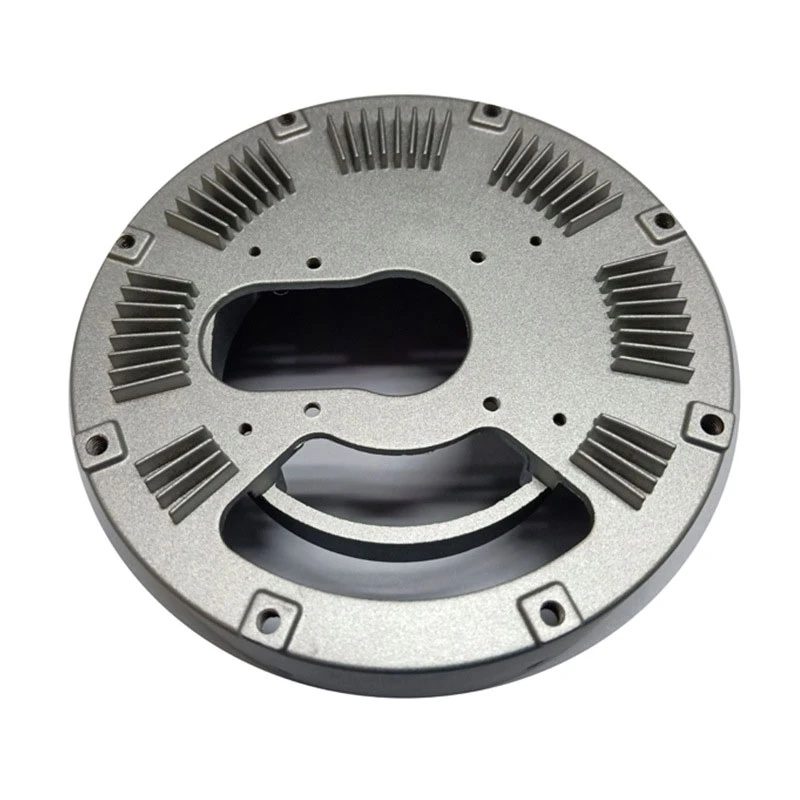
The expertise required in designing the dies—the tools used in stamping—underscores the specialized knowledge necessary for a successful stamping operation. Die engineering demands an understanding of material behavior, machine capabilities, and the desired specifications of the end product. It also requires innovation to anticipate and solve issues like spring-back (where metal returns to its original shape after bending), ensuring components are manufactured to exact tolerances consistently.
The authority of a company in the stamping industry often hinges on its technological prowess and compliance with industry standards. Cutting-edge technologies such as computer-aided design (CAD) systems and finite element analysis (FEA) simulations are employed to craft dies with precision and predict potential problems before they arise on the production floor. Such technology adoption not only streamlines operations but also reinforces a company's competitive position in the market.
stamping car parts
Moreover, trustworthiness is particularly significant in stamping car parts, as the structural integrity of a vehicle—and by extension, the safety of its occupants—depends on the reliable performance of these components. Rigorous testing and quality control are paramount at every stage of the stamping process. Accreditation from recognized bodies and consistent audits offer additional layers of trust and underscore a company's commitment to quality and safety.
Despite its established legacy, stamping car parts continuously evolves with innovations such as servo-press technology, which provides unparalleled control over the speed and motion of the stamping press, enabling more energy-efficient and precise operations. The adoption of Industry 4.0 principles, such as IoT and real-time data analytics, further enhances the stamping process by minimizing downtime through predictive maintenance and streamlining supply chain logistics.
For businesses engaged in stamping car parts, maintaining relevance involves an ongoing commitment to research and development. Developing sustainable stamping practices is becoming increasingly crucial as companies strive to reduce their environmental footprint. Implementing waste reduction strategies and optimizing resource use, such as recycling scrap metal, are not only environmentally responsible practices but also result in cost savings.
Stamping car parts also demands a keen focus on workforce development. Skilled machinists, engineers, and technicians must be continually trained in the latest technologies and methodologies to sustain the companies' reputation for reliability and quality. Comprehensive training programs and partnerships with educational institutions foster a pipeline of talent equipped to meet current and future industry challenges.
In sum, the realm of stamping car parts is a dynamic ecosystem shaped by innovation, precision engineering, and dedicated craftsmanship. The combination of traditional methodologies with cutting-edge technology underscores the sector's resilience and adaptability in meeting the ever-evolving demands of the automotive market. This confluence of expertise, authority, and trust positions stamping not just as a manufacturing process but as an essential pillar in the foundation of modern automobile construction.