Silica sand, a vital component in metal casting, is not merely about availability and pricing. Its relevance in the realm of metal casting extends far beyond. This naturally occurring mineral, primarily composed of silicon dioxide (SiO2), plays a pivotal role in producing high-quality castings. The excellence of silica sand is defined by factors like grain shape, size distribution, and purity, each contributing to the casting's surface finish, strength, and dimensional accuracy.
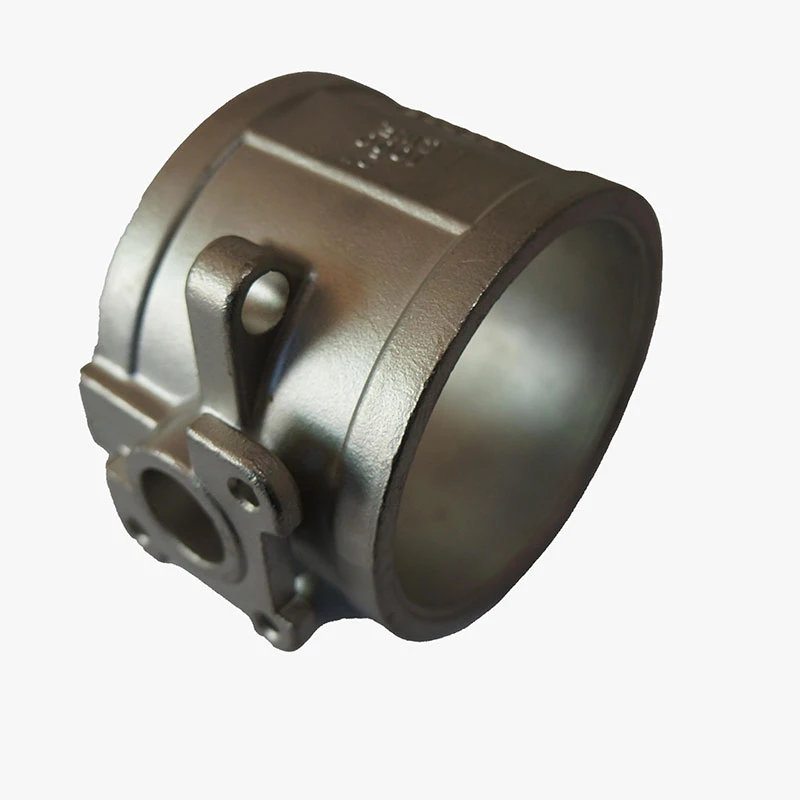
Precision casting begins with the selection of appropriate materials, and using high-quality silica sand ensures superior results. The importance of grading cannot be overstated; uniform grain size distribution impacts the sand's permeability, affecting how gases escape during the casting process. An optimal grain size offers a balance that prevents defects while ensuring a smooth finish. Industries leveraging silica sand's properties typically conduct rigorous testing to ascertain the precise compatibility of the sand with their casting processes.
Expert foundries understand that not all silica sands are created equal. To maximize casting precision and minimize defects such as sand inclusions, they rely on sands that have a round grain shape. This characteristic influences packing density and the subsequent permeability and green strength of the mold. Additionally, round-grained sand facilitates better handling and cleaning in automated systems, reducing operational inefficiencies.
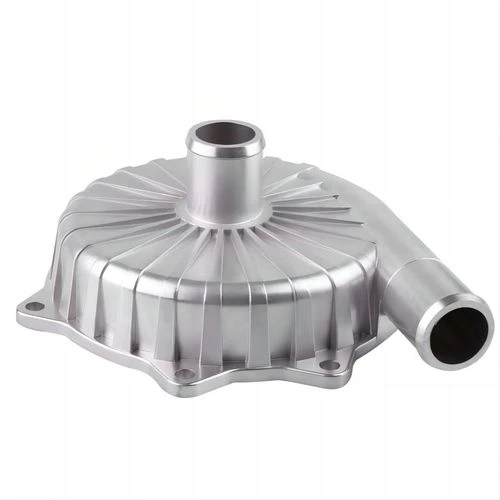
Purity of silica sand can significantly impact the metal casting process. The presence of impurities can lead to unwanted reactions, influencing the integrity of the cast product. Experienced metallurgists advocate for the use of high-purity sand, especially in critical applications such as aerospace and automotive industries, where even minor deviations can cascade into critical failures. Foundries often employ meticulous washing and grading processes to enhance the purity levels of the sand, thus ensuring compliance with strict industry standards.
silica sand for metal casting
The credibility and trustworthiness of a foundry in delivering top-notch cast goods often hinge on its ability to employ the most suitable silica sand. Established firms never compromise on sourcing sand from reputable suppliers known for consistent quality. By upholding strict quality assurance protocols, these suppliers offer sand that aligns with regulatory compliances, ensuring both safety and environmental adherence.
It's noteworthy how innovative technological advancements are enhancing the usability of silica sand in metal casting. Recent developments incorporate enhanced thermal properties, which allow for greater refractory capabilities suitable for high-temperature applications. This edge provides foundries with the flexibility needed to pursue more complex and demanding casting projects, thereby expanding their potential business horizons.
The holistic approach taken by industry leaders extends beyond just procuring silica sand. They adopt a comprehensive framework involving continuous process improvements, leveraging cutting-edge technology, and investing in workforce training. This end-to-end commitment from resource selection to finished product delivery is what sets experts apart in the highly competitive metal casting arena.
In a landscape where precision is non-negotiable, and competition is intense, the informed use of silica sand stands as a cornerstone of excellence. Advanced techniques and entrenched expertise enable manufacturers to exploit this resource efficiently. Moving forward, the unyielding demand for high-quality castings will only elevate the status of silica sand from a mere ingredient to an indispensable asset in metal casting.