When it comes to die casting, particularly the process involving a shot sleeve, understanding the mechanics, composition, and its influence on the final product is critical. The shot sleeve serves as a pivotal component in the high-pressure die casting process, often dictating the quality and efficiency of the operation. Its robust design is crucial for ensuring molten metal is injected precisely and efficiently into the die cavity, a process integral to manufacturing dense, superior-quality metal parts.
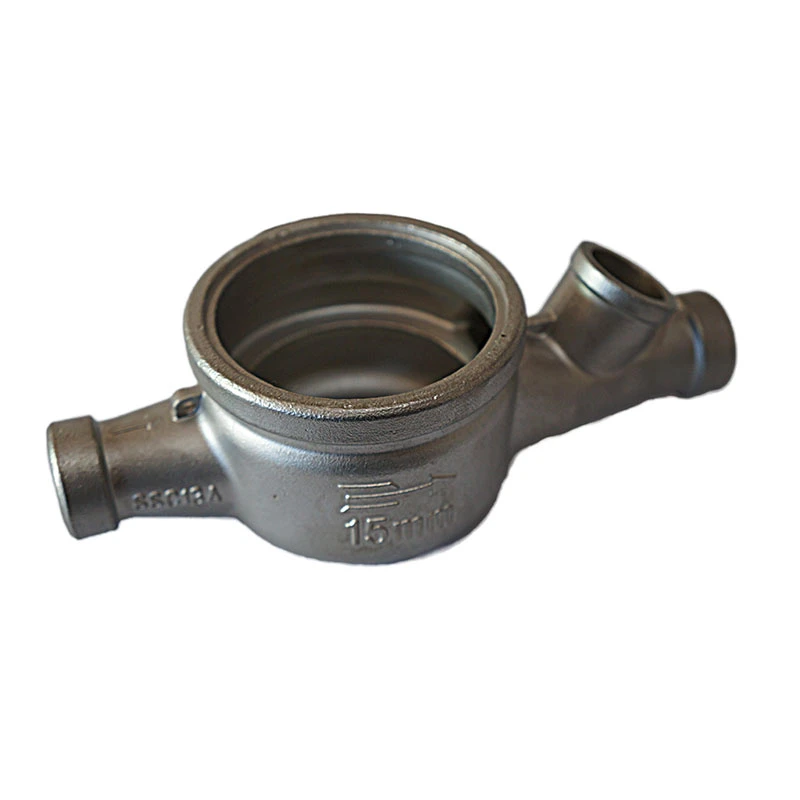
Shot sleeves are typically constructed from high-grade materials such as H13 tool steel, revered for its durability and heat resistance. The choice of material is instrumental in maintaining the structure under immense thermal and mechanical stress. Precision engineering is essential in its fabrication to prevent common die casting issues, such as porosity and misruns, which directly impact the reliability of the final product.
From an expert's point of view, optimizing the shot sleeve’s dimensions and maintenance schedules contributes significantly to enhancing the efficiency of the die-casting process. The inner surface of the shot sleeve should be perfectly smooth and chromium-coated to minimize friction and wear, facilitating a seamless flow of molten metal. Regular inspection and maintenance of the shot sleeve are imperative to prevent the accumulation of aluminum oxides and other residues that can obstruct metal flow, ensuring longevity and consistent performance.
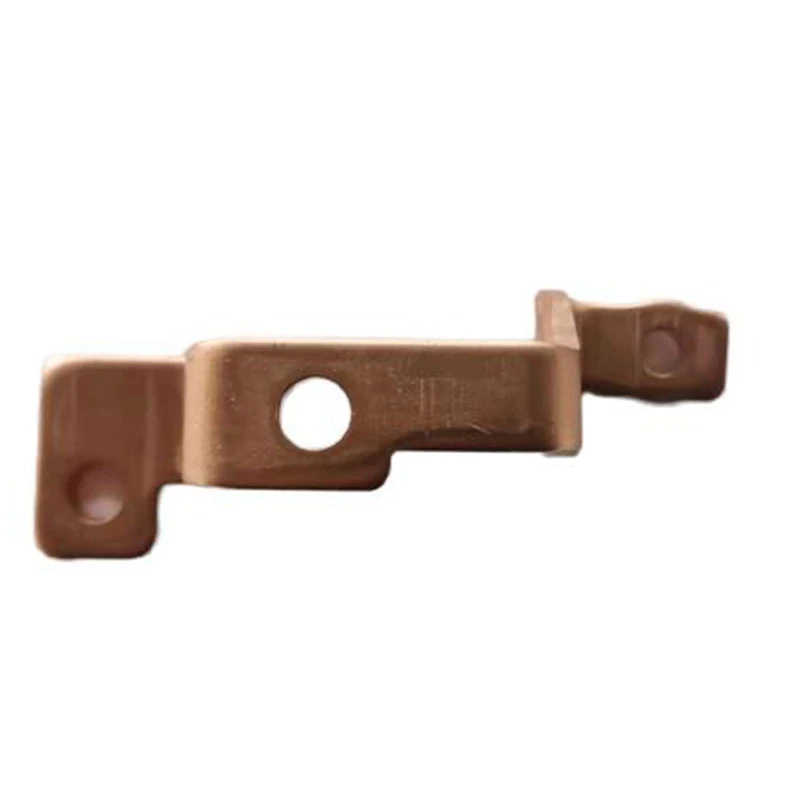
The shot sleeve's design directly influences the shot velocity and pressure, critical factors determining the quality of the casting. These parameters should be meticulously calibrated to prevent turbulence during metal injection, which can cause defects such as gas porosity. A well-designed shot sleeve minimizes turbulence, ensuring the metal fills the die cavity efficiently, thereby producing parts with high structural integrity.
Implementing advanced technologies such as simulation software in the design phase can provide insights into optimizing the shot sleeve’s performance. Simulations allow engineers to test different scenarios, adjusting parameters to achieve the desired outcomes before the actual casting process. This proactive approach enhances the manufacturability and reliability of the components produced, ultimately leading to cost savings and improved product quality.
shot sleeve in die casting
The expertise in employing cutting-edge technology and continuous innovation forms the backbone of successful manufacturing. Engineers and operators experienced in high-pressure die casting understand that the shot sleeve is not merely a conduit for molten metal but a critical component affecting the entire process chain. This expertise ensures the design and operation are always aligned with the latest industry standards, guaranteeing precision and efficiency.
From an authoritative standpoint, trusted manufacturers and suppliers of die casting equipment boast a thorough understanding of the shot sleeve mechanics. They remain committed to pioneering advancements in material science and engineering, maintaining a competitive edge. Engaging with stakeholders across the supply chain, these manufacturers invest in research and development, ensuring they remain at the forefront of the industry, offering products that exceed quality and performance benchmarks.
Die casting experts recommend partnering with reputable suppliers who provide comprehensive support, including technical consultation, material selection advice, and maintenance services. This partnership fosters trust and assures clients of the best practices in shot sleeve maintenance and operation, reinforcing the reliability of the end products.
In conclusion, the role of the shot sleeve in die casting is of paramount importance. Its careful design, construction, and maintenance are essential for achieving precision and quality in metal parts production. Leveraging innovation, expertise, and authority in the field ensures the continued advancement and reliability of the die-casting process. Commitment to excellence in shot sleeve technology not only enhances the manufacturing process but also builds long-lasting relationships based on trust and superior performance.