Progressive stamping die design is an intricate and vital process in the manufacturing sector, where efficiency and precision are paramount. This intricate process involves the use of a series of stamping stations, each with its own unique function, designed to transform sheet metal into complex, finished parts with minimal waste. The efficiency brought about by progressive die design significantly reduces production costs while maintaining high precision and repeatability in mass production.
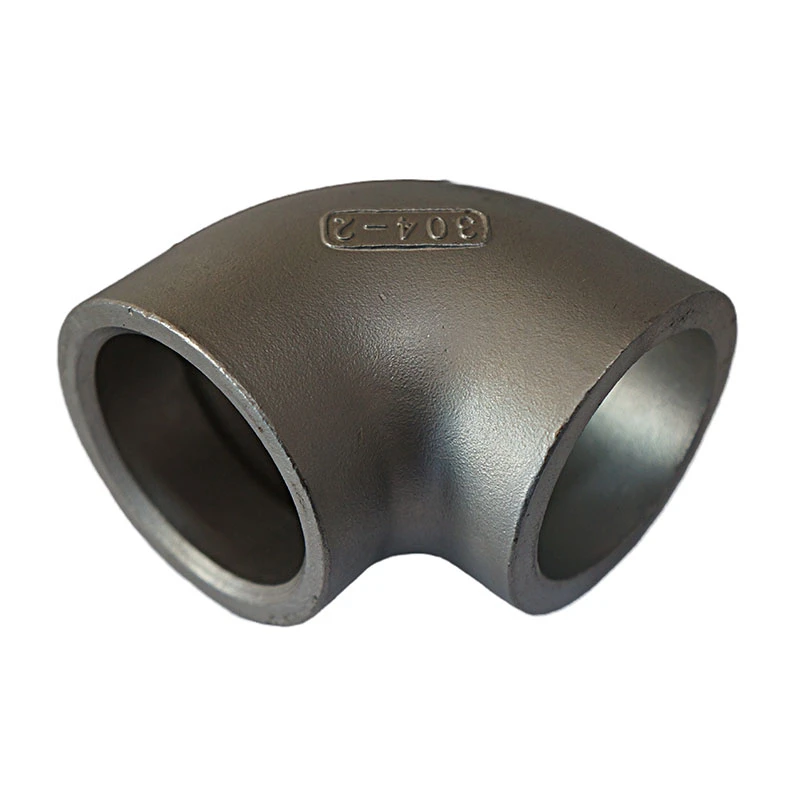
An effective progressive stamping die design starts with a thorough understanding of the production requirements. Engineers work closely with manufacturers to gather details about the part specifications, material type, thickness, and desired production volume. From a practical standpoint, understanding these factors allows for the creation of a die that not only performs efficiently but also has a longer lifespan. This early collaboration ensures that the design adheres to the technical standards while accommodating any unique manufacturing challenges.
Material selection is another critical aspect that contributes to the success of a progressive stamping die. Different materials have varying characteristics that affect wear resistance, formability, and cost. For instance, tool steels like A2 and D2 are commonly used due to their hardness and wear resistance, which are necessary for enduring the repeated stress of the stamping process. Additionally, considering the material’s thermal expansion properties can mitigate unexpected changes in die dimensions during operation, thus maintaining the precision of the stamped product.
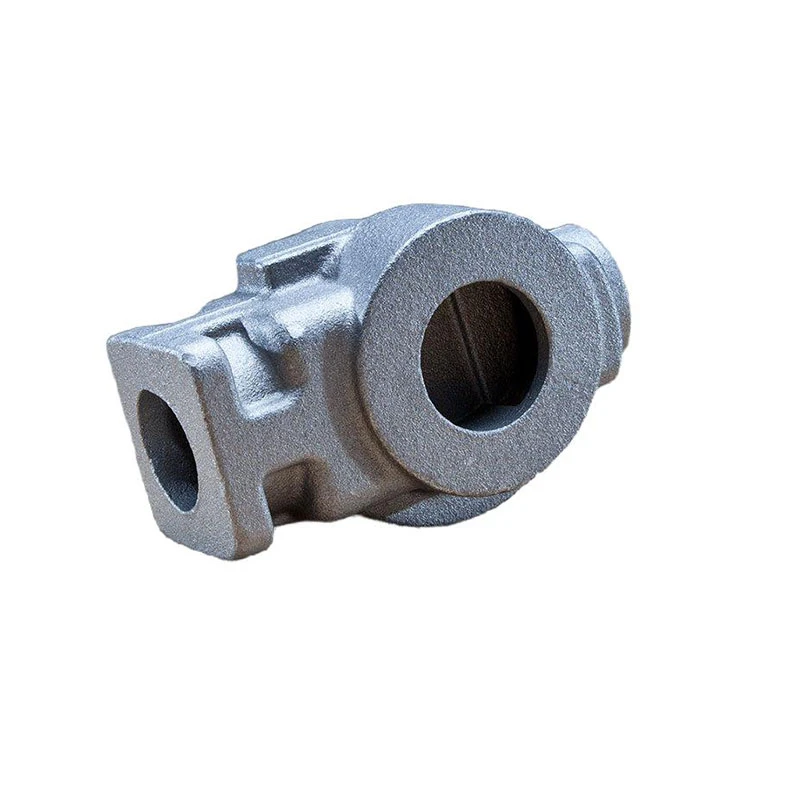
Precision in design cannot be overstated. The design phase involves the creation of detailed CAD models which simulate the stamping process. This simulation is not just about the visual representation of the part being formed, but it also validates the die design to ensure that potential issues such as material tearing, wrinkling, or excessive wear are identified and resolved before the manufacturing process begins. Finite element analysis (FEA) tools are often used to predict material behavior and optimize the sequence of operations within the die.
To ensure robustness and reliability, expert die designers incorporate features that enhance the alignment and guide precision of the die. Guide pillars, wear plates, and accurate punch-and-die alignment are meticulously planned to ensure that each station in the die performs its task precisely. This precise alignment is instrumental in achieving consistent quality across large production runs, hence reinforcing the trustworthiness of the production process.
progressive stamping die design
The authoritative aspect of progressive die design is best demonstrated through the sophisticated technology and expertise required. Those responsible for designing and maintaining these systems must possess an in-depth understanding of product design principles, metallurgy, and production techniques. Continuous learning and adaptation are keys, as advances in machine technology and materials can influence the future designs of progressive stamping dies. Regular training sessions and workshops are crucial investments for companies aiming to stay at the forefront of this field.
Once in operation, it is essential to establish a routine maintenance schedule for the dies to prevent unexpected breakdowns, which can lead to costly downtime. Regular inspection, cleaning, lubrication, and adjustment of the dies not only extend their life but also assure consistent production quality. Trust is built with customers when they are confident that each part they receive is manufactured to the highest standard without deviation.
Moreover, real-world experience brings a unique perspective to the field of progressive stamping die design. Experienced professionals often know subtle intricacies that might not be immediately obvious through theoretical study alone. For example, they are adept at determining optimal press speed, tonnage requirements, and the arrangement of progression within the die which translates to minimal waste and maximized output. This experiential knowledge is invaluable in troubleshooting issues that arise, often leading to quicker, more effective solutions.
Progressive stamping die design is not merely a technical task; it’s an art that combines engineering, precision, and experience. With every advancement in technology, the need for seasoned expertise grows, ensuring that the end products remain competitive in terms of quality and cost. By focusing on these core elements—experience, expertise, authoritativeness, and trustworthiness—the progressive stamping process continues to evolve, pushing the boundaries of what is possible in metal fabrication while fostering relationships built on a robust foundation of reliability and excellence.