Metal precision components are the unsung heroes of modern engineering, playing a crucial role in the functionality, durability, and efficiency of countless products across various industries. From automotive to aerospace and electronics to medical devices, these components are integral to the structures and systems we rely on daily. As an engineer with decades of hands-on experience in the design and fabrication of precision components, I understand their significance and the meticulous process required to produce them to exact standards.
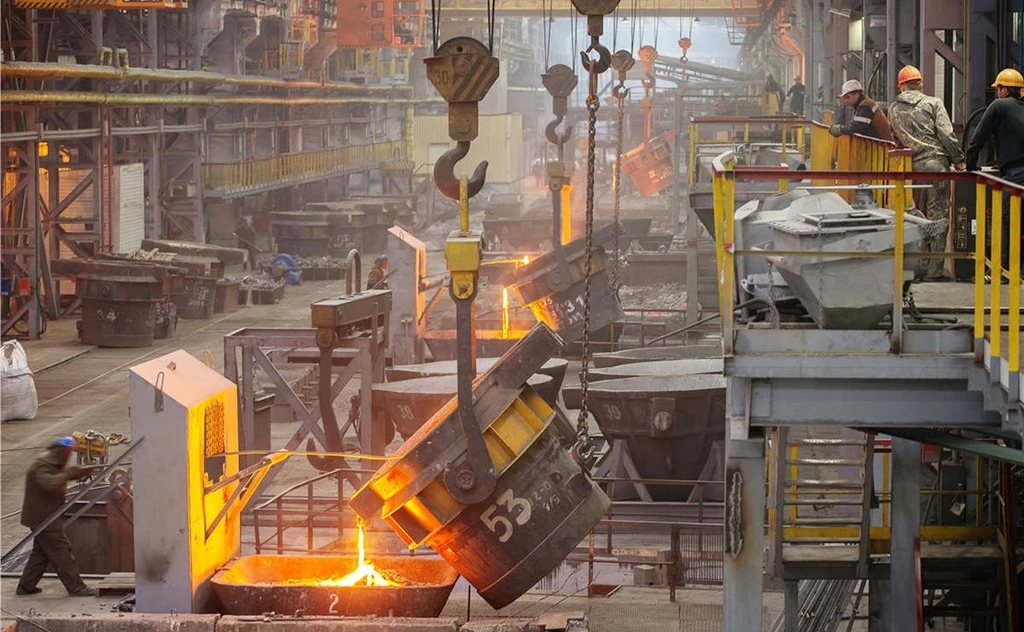
Creating metal precision components demands expertise not only in engineering principles but also in material science. High precision machining is not limited to cutting and forming; it's a symphony of technology, skill, and understanding the unique properties of different metals. For instance, the decision to use stainless steel, aluminum, or titanium goes beyond just the application; it involves examining factors like tensile strength, corrosion resistance, and weight.
One notable example from my career involved designing a component for the aerospace industry where weight and strength were critical.
The challenge was to maintain structural integrity while minimizing the component's weight. This required innovations in the use of titanium alloys, known for their superior strength-to-weight ratio and resistance to extreme temperatures. These materials, while advantageous, required adjustments to our CNC machining processes, including tooling and speed alterations to maintain precision without compromising the material's properties.
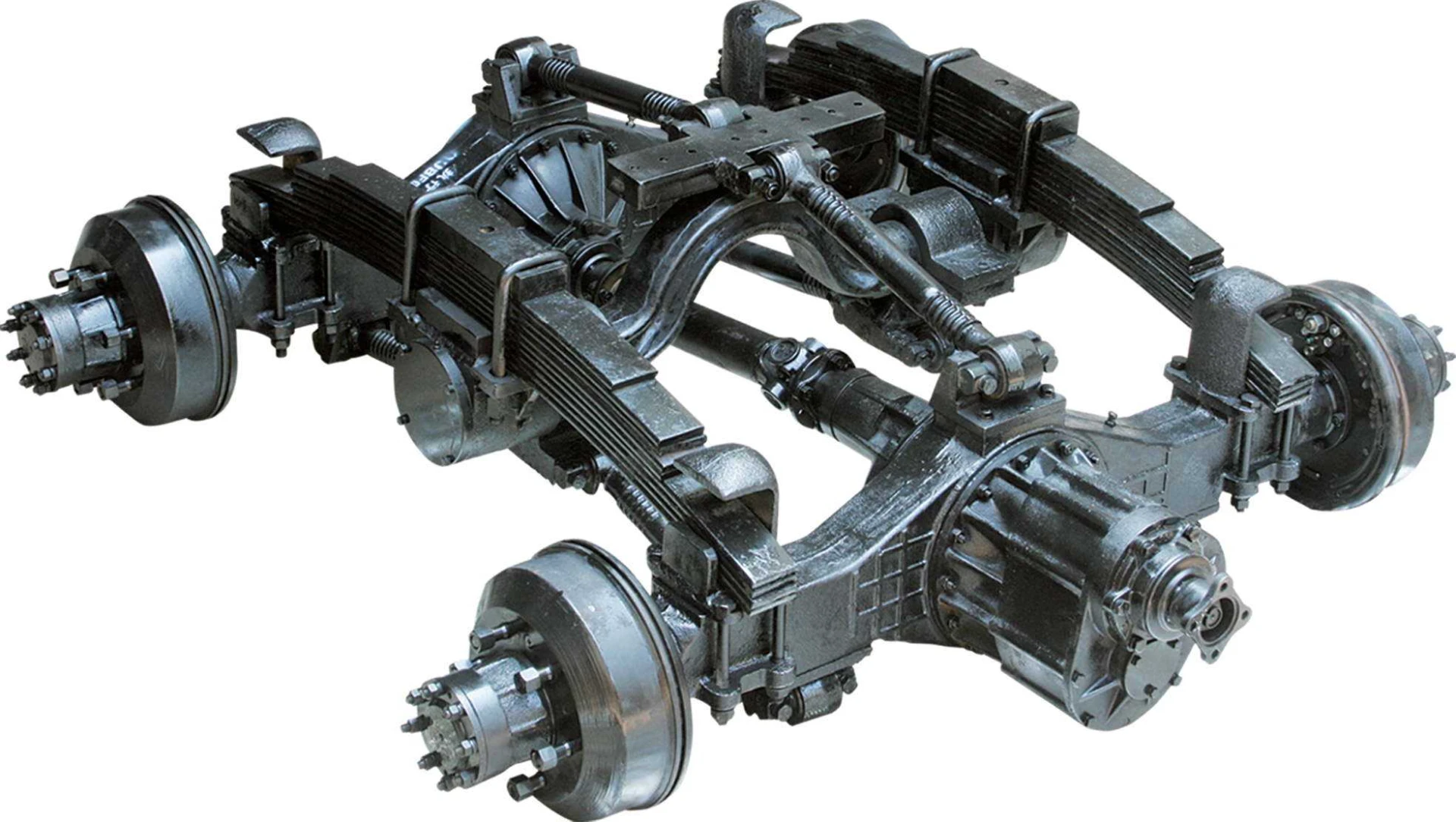
Attention to detail in every phase of production is paramount. The journey from prototype to production-scale involves a rigorous testing phase to ensure each component may withstand the demands of its intended environment. In the medical field, for instance, precision is paramount; components such as surgical instruments or implantable devices must meet stringent hygiene and functional standards. Our team meticulously inspects each component using advanced measurement technologies like 3D laser scanning and Coordinate Measuring Machines (CMM) to achieve micrometer-level accuracy.
metal precision components
One fundamental aspect of expertise in producing these components is the ability to forecast and troubleshoot potential issues. It involves a deep understanding of not only the machines and materials but also the application. For example, when creating components for electrical devices, precision ensures appropriate connectivity and prevents interference, a testament to the criticality of dimension accuracy and surface finish. By simulating operational stresses and conducting fatigue testing, we can predict performance under extreme conditions, tailoring each component to its specific endurance requirements.
Authoritativeness in the field of precision component manufacturing is built through continuous innovation and adaptation. As technology advances, so does the sophistication of the components we are expected to deliver. Our facility continuously invests in cutting-edge machinery and software, ensuring we remain at the forefront of manufacturing capabilities. Adopting methods like additive manufacturing (3D printing) for prototyping allows us to expedite the development phases and implement rapid refinements to design iterations without traditional machining constraints.
Trustworthy manufacturing processes also involve adhering to international standards and certifications such as ISO 9001, which affirm our commitment to quality. Further, our collaboration with clients is more than transactional; it is a partnership. By keeping open channels for feedback and incorporating customer-specific requirements into our processes, we address unique industry challenges, be it tighter tolerances or advanced material applications.
In conclusion, metal precision components are much more than their role in the finished product; they are vital elements that demand a convergence of experience, specialized knowledge, authoritative best practices, and a robust framework of trust and quality assurance. Through dedication to craftsmanship and an unwavering focus on innovation, these components not only fulfill their expected functions but often exceed the capabilities of any initial design aspirations, driving forward technological advancement in every sector they touch.