Pressure die casting parts form the backbone of modern manufacturing, providing critical components for various industries, including automotive, aerospace, electronics, and consumer appliances. The precision, durability, and efficiency offered by these components have revolutionized production processes, making them indispensable in today's technological landscape.
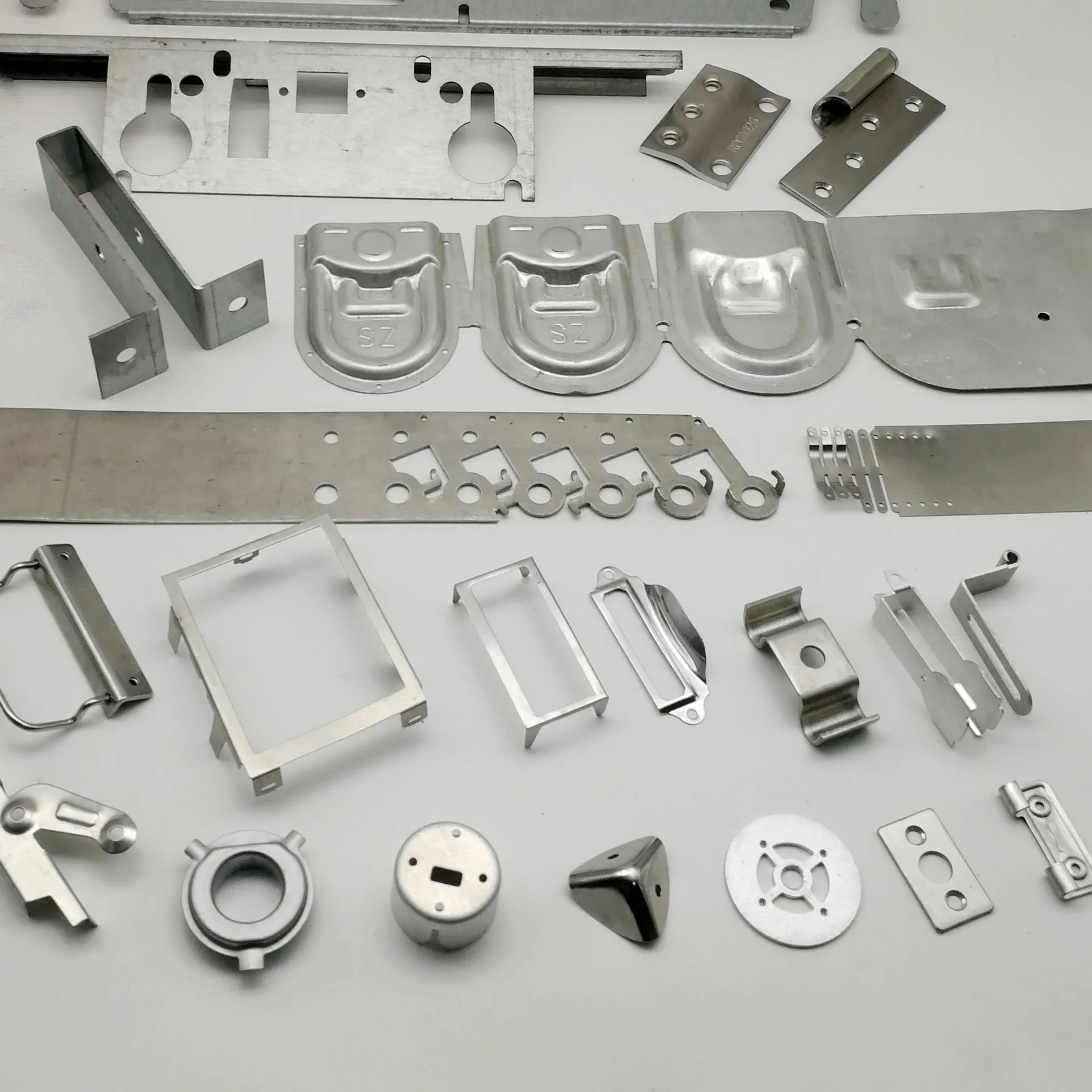
Having been in the manufacturing sector for over two decades, I've seen firsthand how the meticulous design and crafting of pressure die casting parts can significantly influence a product's performance and lifecycle. The art and science of pressure die casting lie in the ability to produce complex shapes with tight tolerances, all while ensuring high strength and a superior finish. This intricate process begins with molten metal — typically aluminum, zinc, or magnesium — which is injected into a die at high pressure. The rapid cooling and solidification allow for the creation of parts with exceptional dimensional stability and surface smoothness.
The expertise required in pressure die casting is immense. It involves a deep understanding of material properties, die design, and the thermal dynamics at play during the casting process. From my experience, the choice of metal is crucial; aluminum, for instance, is favored for its lightweight and corrosion-resistant qualities, making it ideal for automotive applications where fuel efficiency and durability are paramount. On the other hand, zinc's excellent casting properties and ability to produce intricate details make it ideal for electronic components and small gears.
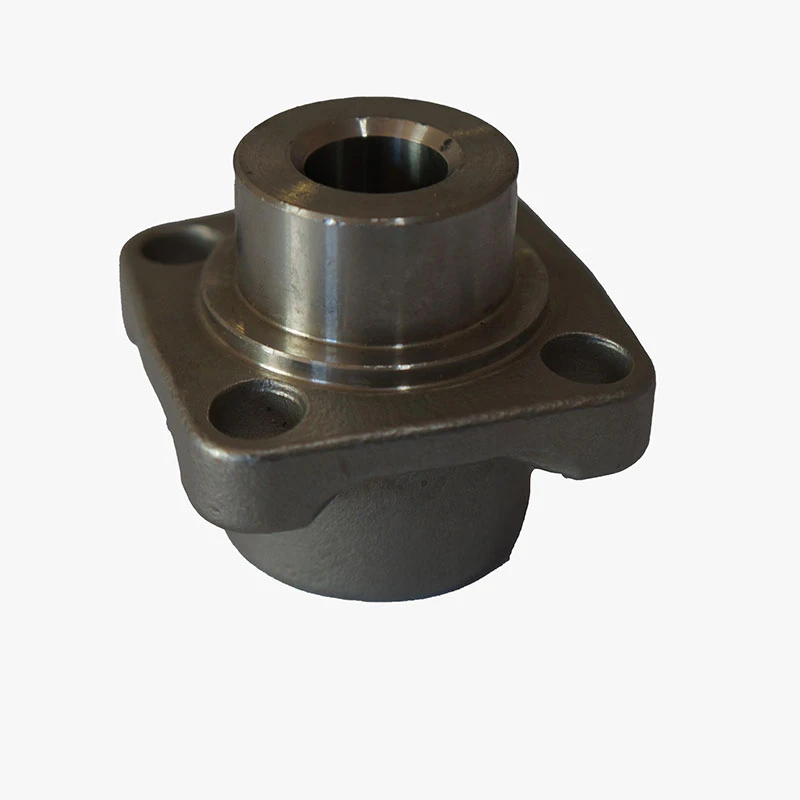
pressure die casting parts
Authoritativeness in the field of pressure die casting is measured by a manufacturer's capability to innovate and adapt to emerging technologies. For example, the adoption of computer simulations and 3D modeling in die design has drastically improved the precision and efficiency of the casting process. These technologies allow for the prediction and mitigation of potential issues such as shrinkage or thermal distortion, which can compromise the integrity of the final product. Collaborating with engineers and industry experts to incorporate these advanced methodologies underscores a commitment to quality and forward-thinking manufacturing practices.
Trustworthiness in pressure die casting operations stems from consistent quality assurance and adherence to stringent industry standards. ISO certifications and regular audits are indicative of a manufacturer's dedication to maintaining high standards of production and environmental responsibility. For instance, implementing a comprehensive quality management system ensures that each step of the casting process is monitored and optimized for repeatability and excellence. Moreover, investing in sustainable practices such as recycling excess metal and reducing energy consumption speaks to a company's accountability and desire to build long-term trust with clients and stakeholders.
In summary, pressure die casting parts are more than just components; they are integral to the reliability and success of the end products they form. By combining real-world experience with academic expertise, manufacturers can continue to lead in this specialized field. As the demand for high-quality, cost-effective, and environmentally conscious manufacturing solutions grows, so will the opportunity for companies that excel in pressure die casting to innovate and set industry benchmarks.