Green sand casting stands as a cornerstone in the metal casting industry, known for its cost-effectiveness and versatility. For foundries large and small, the selection of high-quality green sand casting supplies is essential to ensure the production of consistent, defect-free castings. This guide delves into the nuances of choosing these critical supplies, helping you enhance the quality and efficiency of your casting processes.
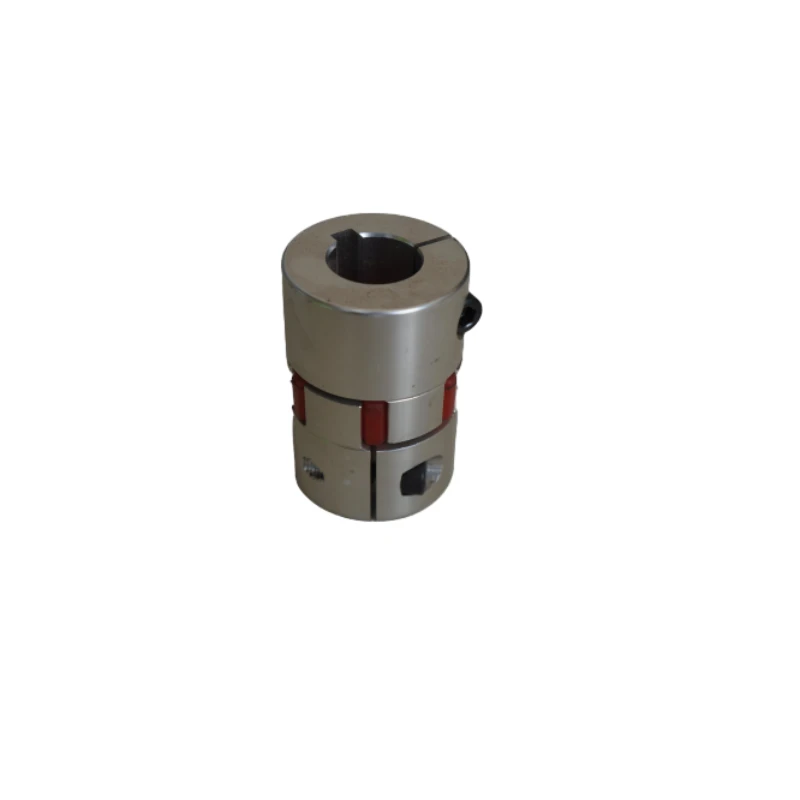
Green sand casting refers to the molding processes where sand, clay, and water form the mold material. It's an ancient technique that's advanced significantly with technology, offering unmatched adaptability and precision. Expertise in this area begins with an understanding of each component's role and the selection of the right supplies.
The Sand Component Quality Matters
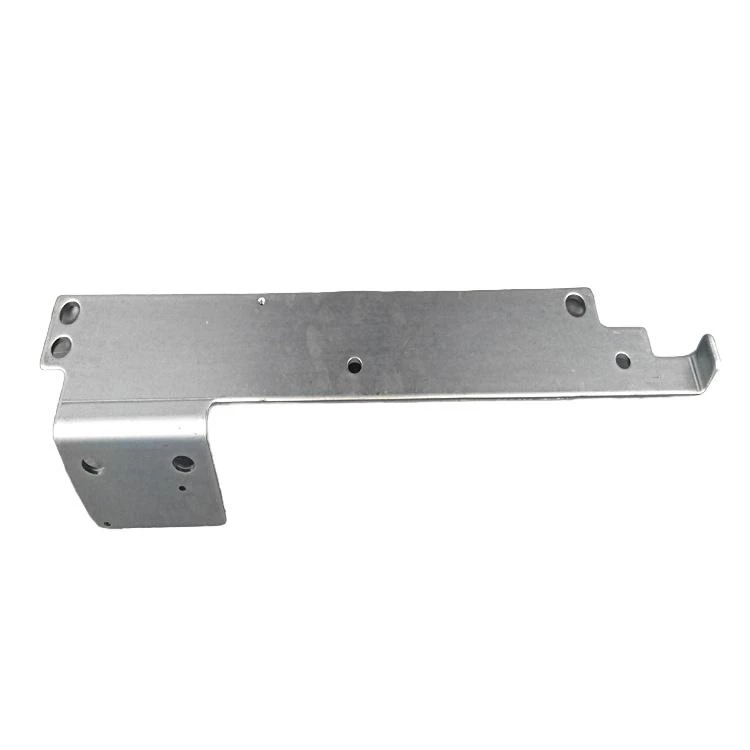
The primary ingredient in green sand casting is the sand itself. Generally composed of silica, the quality of sand directly impacts mold integrity and surface finish of the cast products. Foundries should seek suppliers that provide sand with optimal grain size, shape, and distribution. Coarser grains might improve permeability but can sacrifice the surface finish, whereas finer grains result in a smoother finish but might hinder proper gas escape. It's crucial to assess the specific needs of your projects when procuring sand.
Secondary ingredients, like chromite or zircon sands, are sometimes added to enhance specific properties like thermal stability or surface finish. An expert supplier will provide thorough guidance on these enhancements to suit your casting requirements.
Understanding the Binder – Clay in Green Sand
Clay acts as the binder that holds the sand grains together. Bentonite clay is commonly used due to its swelling properties when mixed with water, which increases mold strength. The selection of clay involves assessing properties like its green compression strength, permeability, and ability to maintain coherence at high temperatures. An inadequate binder can lead to mold collapsibility issues, directly impacting casting integrity.
Regular testing and analysis should be implemented to monitor the effectiveness of the clay component in your sand mix. This ensures that the composition remains consistent, especially in a high-turnover environment where molds are recycled frequently.
Water The Right Balance
green sand casting supplies
Water content in the sand mixture is a critical factor that influences the mold's plasticity and collapsibility. Too much water can cause defects like blowholes, while too little can lead to inadequate mold cohesion. Expertfoundrymen regularly monitor and adjust moisture levels, taking into account environmental factors such as temperature and humidity, to maintain ideal conditions for mold production.
Chemical Additives Enhancing Performance
Modern green sand casting often involves the use of chemical additives to improve mold properties such as strength, permeability, and the surface finish of the casts. Additives like carbonaceous materials help reduce defects by forming a semi-permeable layer between the mold and casting. Expertise in the application and proportion of these additives is crucial, as they can alter the characteristics of the molds in subtle yet significant ways.
Equipment Precision in Process Control
The equipment used for mixing and molding plays a vital role in the quality of green sand castings. High-performance mixers ensure uniform distribution of sand, clay, water, and additives. Additionally, automated molding machines provide precise compaction and consistency across numerous moldings, minimizing errors and production scarcities.
Foundry operators should invest in regularly updated and well-maintained equipment. Regular calibration and maintenance schedules ensure machines operate at optimum levels, contributing significantly to reducing waste and increasing the quality of the final product.
Trust in Expert Suppliers
Selecting the right supplier for green sand casting supplies defines the success and efficiency of your green sand casting operations. Look for suppliers with demonstrated expertise and a track record of innovation within the industry. Trust is built on previous performances, detailed quality reports, and their willingness to offer solutions tailored to specific project needs.
In conclusion, the right supplies and equipment combined with expertise in managing the green sand casting process are pivotal for producing high-quality castings. This foundation not only improves the operational efficiency of your foundry but also elevates the quality of the cast products, ensuring your business maintains its competitive edge in the demanding field of metal casting.