The art of zinc casting has revolutionized industries by providing versatile and cost-effective solutions for manufacturing. When considering zinc casting round components, it is essential to delve into the intricacies that make this process not only efficient but also a preferred choice for manufacturers prioritizing quality and precision.
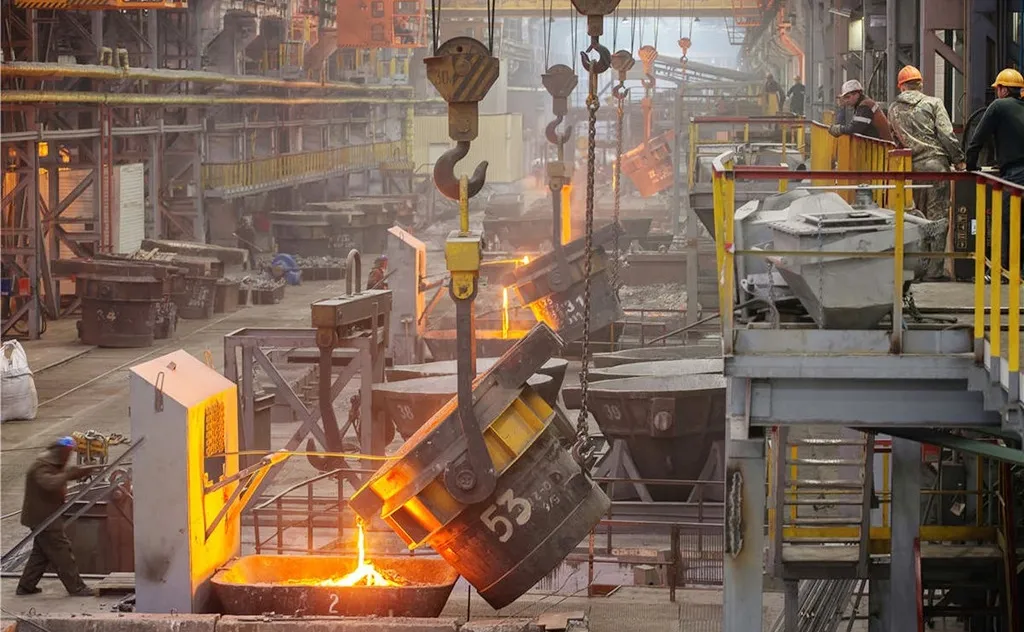
Drawing from years of expertise, zinc casting stands out primarily for its unparalleled dimensional stability and ability to create intricate shapes that would be challenging using other materials. The process involves melting zinc at controlled temperatures and using molds to form round components that boast superb structural integrity. This method is particularly advantageous for producing parts that require high strength-to-weight ratios.
Manufacturers have turned to zinc casting round components for their exceptional wear resistance, and this is not by happenstance. Zinc die casting molds can be produced with tight tolerances that allow for less material waste and higher repeatability, ensuring consistent quality in large production runs. Expert metallurgists often emphasize zinc's capability to conform to precise dimensions, which is critical for products in the automotive, electronics, and telecommunications industries.
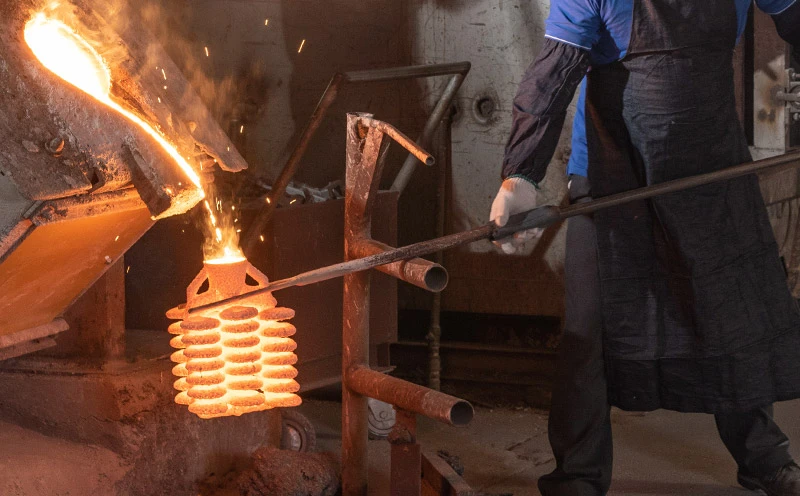
The professional community vouches for zinc casting due to its cost-effectiveness, balancing initial investment in tooling with the long-term savings accrued from low material waste and reduced post-processing needs. The zinc alloy used often contains small percentages of elements such as aluminum, copper, and magnesium, enhancing the component's mechanical properties while maintaining rust resistance.
This makes zinc casting an authoritative choice for projects demanding longevity and reliability.
zinc casting round
For manufacturers seeking trustworthiness in production, zinc casting offers a reliable path towards minimizing defects. The surface finish of zinc cast products is smooth and does not require extensive machining, reducing potential for human error and ensuring consistency across batches. Professionals in the industry often rely on zinc's inherent properties to deliver a trusted performance, especially in applications requiring complex geometries and decorative finishes.
Incorporating zinc casting round components into production not only promotes an efficient engineering process but also supports sustainable practices. Zinc is a recyclable material, and many manufacturers are committed to reducing their environmental footprint by incorporating recycled zinc into their casting processes. This fosters an eco-friendly production line which is crucial in today's environmentally-conscious market landscape.
Implementing zinc casting requires a deep understanding of the material properties and the casting process itself. Consulting with engineers and metallurgists, companies can optimize their designs to take full advantage of zinc's unique benefits. Establishing partnerships with experienced foundries specializing in zinc casting can ensure that the final products meet all quality standards and specifications.
In conclusion, the expertise surrounding zinc casting round components highlights its position as a cornerstone in the manufacturing sector. Its capability to deliver high-quality, cost-effective, and environmentally sustainable products makes it a trusted choice for multiple industries. Investing in zinc casting not only supports production efficiency but also aligns with the core values of modern manufacturing—precision, reliability, and sustainability.