Sand casting is an essential manufacturing process that has been used for centuries to create complex metal components with precision and efficiency. Whether you're a budding entrepreneur aiming to understand sand casting for product creation or a seasoned engineer deep-diving into advanced techniques, understanding the materials involved in sand casting can significantly influence the quality of the final product.
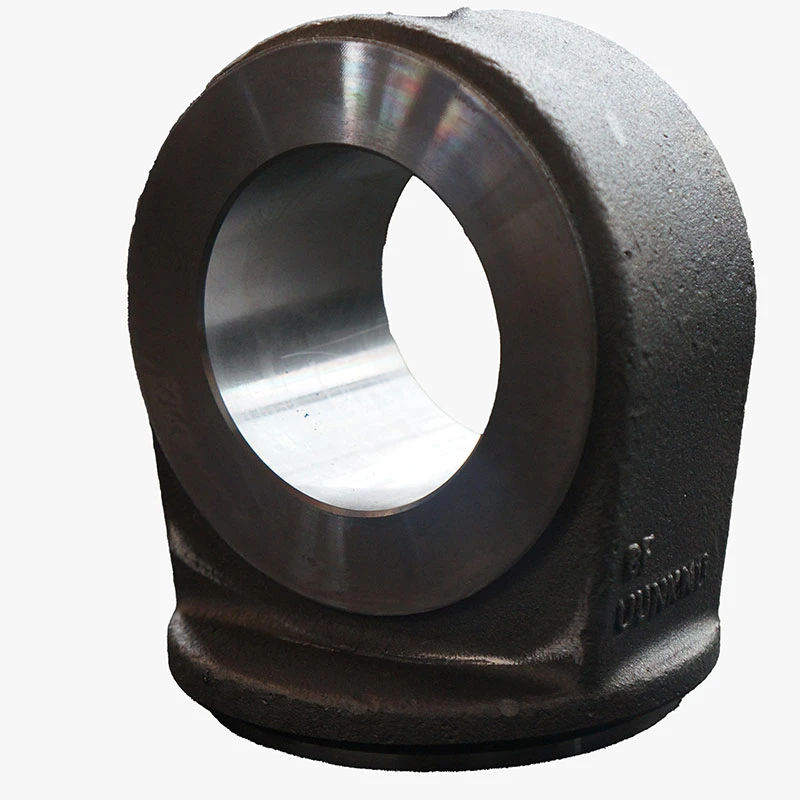
The journey of sand casting begins with the fundamental element the mold. This mold is primarily made from a special type of sand combined with other materials to give it the necessary properties for casting. The choice of sand is crucial as it directly impacts the surface finish, dimensional accuracy, and the overall quality of the cast product.
Silica sand, the most common type used in sand casting, is lauded for its high melting point and collapsibility, which ease the casting process. However, its limitations in terms of thermal expansion and surface finish necessitate the blending with other materials. To combat these issues, manufacturers often mix silica with other substances such as zircon, chromite, or olivine sands. These materials offer lower thermal expansion and higher density, enabling the creation of more detailed and finer surface finishes.
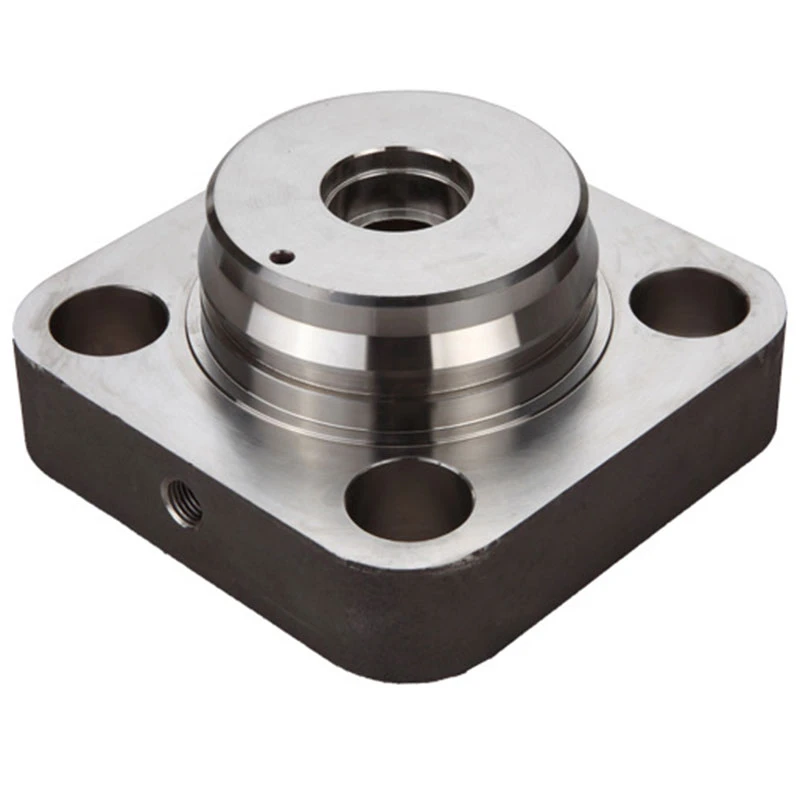
Binding agents are another critical component in the mold-making process. They serve to hold the sand together, providing strength and stability to the mold. Common binders include clay-based binders like bentonite, which are cost-effective and provide adequate strength. Nonetheless, for applications requiring precise tolerances and smooth finishes, alternative organic binders such as phenolic urethanes are often employed for their superior performance in terms of mold rigidity and surface finish quality.
The core in sand casting is another crucial element, especially for creating intricate internal geometries in the casting. Cores are made from similar sand mixtures and bonded with specific binders like furan or sodium silicate. The choice of core materials directly affects the dimensional accuracy and structural integrity of the hollow sections within the casting.
what materials are used in sand casting
A metal of choice is the final and perhaps the most visible aspect of sand casting. The choice of metal depends on the application and desired properties of the finished product.
Common metals include aluminum, iron, steel, and brass. Each metal has its specific set of properties such as melting temperature, shrinkage characteristics, and mechanical strengths, which influence the casting outcomes.
In addition to these core elements, several auxiliary materials play a vital role in refining the casting process. Coatings are applied to molds and cores to minimize the occurrence of casting defects and improve the surface quality. These coatings, typically made from materials like graphite, zirconium silicate, or magnesia, create a barrier between the metal and the sand, preventing sand erosion and metal penetration.
Additionally, additives are occasionally mixed with the sand to enhance specific properties. For example, coal dust can be added to prevent defects such as scabbing and metal penetration. Similarly, other additives may be used to improve the mold’s thermal conductivity and reduce the incidence of casting defects like gas porosities.
The success of sand casting hinges on the harmonious interplay of these materials, matched carefully with the process requirements and desired characteristics of the finished product. Understanding and selecting the right combination of materials not only optimizes production efficiency but also ensures high-quality, durable components.
Continuous advancements in material science and technology have propelled sand casting into new realms, enabling manufacturers to envision and create increasingly complex and high-performance parts. By focusing on the intricate details of material selection and process optimization, engineers and manufacturers can achieve excellence in sand casting, ensuring their products meet the highest standards of quality and performance demanded by today's competitive markets.