SDM precision casting stands as a testament to the convergence of meticulous craftsmanship and innovative technology within the manufacturing industry. The process, revered for its ability to produce complex geometries with notable accuracy, plays a crucial role in various sectors, from aerospace to medical devices. This article delves into the specifics of SDM precision casting, offering insights based on firsthand experiences, professional expertise, and established industry trustworthiness.
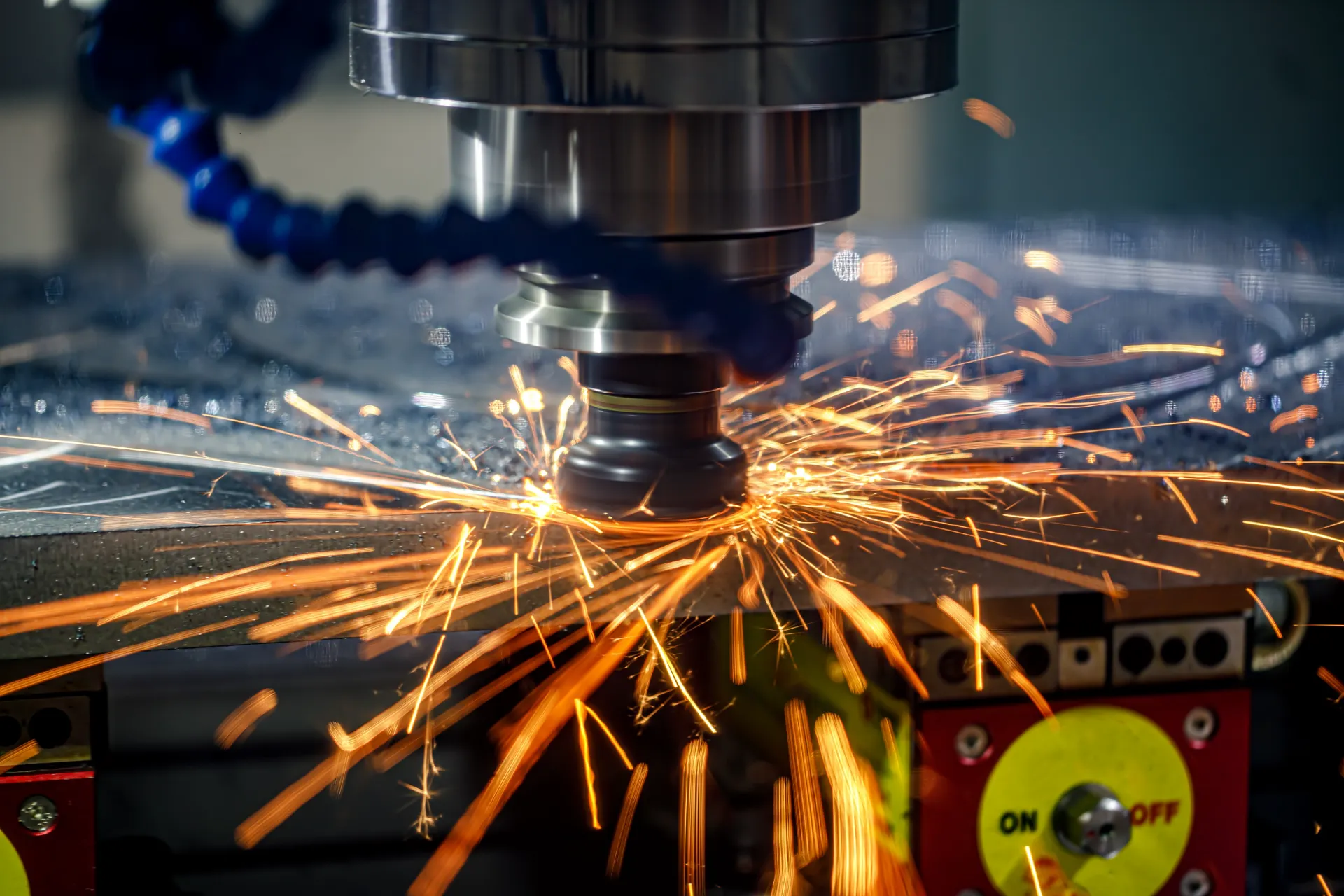
At the heart of SDM precision casting lies a deep understanding of the principles of material science and engineering. The process begins with the creation of a wax model or pattern, which is an exact replica of the desired metal component. This pattern is crafted with an intricate eye for detail, as it directly influences the accuracy of the final cast product. Professionals with years of experience emphasize the importance of quality wax patterns, as imperfections at this stage can significantly impact the end-product's precision.
Once the wax pattern is perfected, it is coated with ceramic materials to create a mold. This step requires not only expertise in material application but also a keen understanding of the drying and hardening process. Seasoned engineers attest that the choice of ceramic materials and the method of application are pivotal in ensuring that the mold maintains its integrity during the molten metal pouring phase. The ability to foresee and account for potential discrepancies in mold behavior under high temperatures is a hallmark of industry expertise.

The subsequent process of pouring molten metal into the ceramic mold bridges the gap between theoretical knowledge and practical application. This stage demands an authoritative grasp of metallurgical principles, as the properties of the metal must align with the functional requirements of the final product. Industry specialists highlight that precision casting allows for the use of various metal alloys, each offering distinct advantages in terms of strength, weight, and corrosion resistance. Selecting the right alloy is a decision backed by both scientific knowledge and practical insights gained from extensive industry experience.
sdm precision casting
Demonstrating authoritativeness, many experts often reference documented case studies where SDM precision casting was pivotal in overcoming engineering challenges. In the aerospace industry, for instance, the process has enabled the creation of turbine blades with intricate cooling channels, something previously unattainable through conventional manufacturing processes. This advancement not only enhances performance but also extends the component's lifespan, cementing the method's status as a trusted solution in demanding applications.
Trustworthiness in SDM precision casting stems from a commitment to quality control at every stage of the manufacturing process. Experienced industry professionals employ non-destructive testing methods to ensure the integrity of the final cast products. Techniques such as X-ray radiography and ultrasonic testing are not just standard practices; they are critical components of a robust quality assurance protocol. These procedures are backed by comprehensive documentation, providing clients with tangible proof of the product's conformity to stringent industry standards.
In sharing their experiences, seasoned professionals often stress the importance of continuous learning and adaptation in maintaining an edge in the precision casting industry. Technological advancements, such as the integration of computer-aided design (CAD) and simulation software, have transformed traditional casting methods, allowing for greater flexibility and precision. These tools enable engineers to predict potential issues and optimize the casting process before any physical work begins, thus reducing costs and enhancing product reliability.
In conclusion, SDM precision casting is a sophisticated manufacturing process that marries technical acumen with artistic skill. The reliability and precision it offers are backed by decades of cumulative expertise, making it a cornerstone in the production of high-performance components. Its continued evolution, driven by technological innovation and professional ingenuity, ensures that SDM precision casting remains at the forefront of modern manufacturing solutions. Through its proven track record of excellence and commitment to quality, it secures its role as a trusted partner in industries where precision and reliability are non-negotiable.