Sand casting iron is an ancient technique that continues to be indispensable in modern manufacturing. Its enduring relevance can be attributed to its versatility, cost-effectiveness, and efficiency in producing a broad range of intricate metal components. This article explores the nuances of sand casting iron, emphasizing its practical applications and benefits in contemporary production.
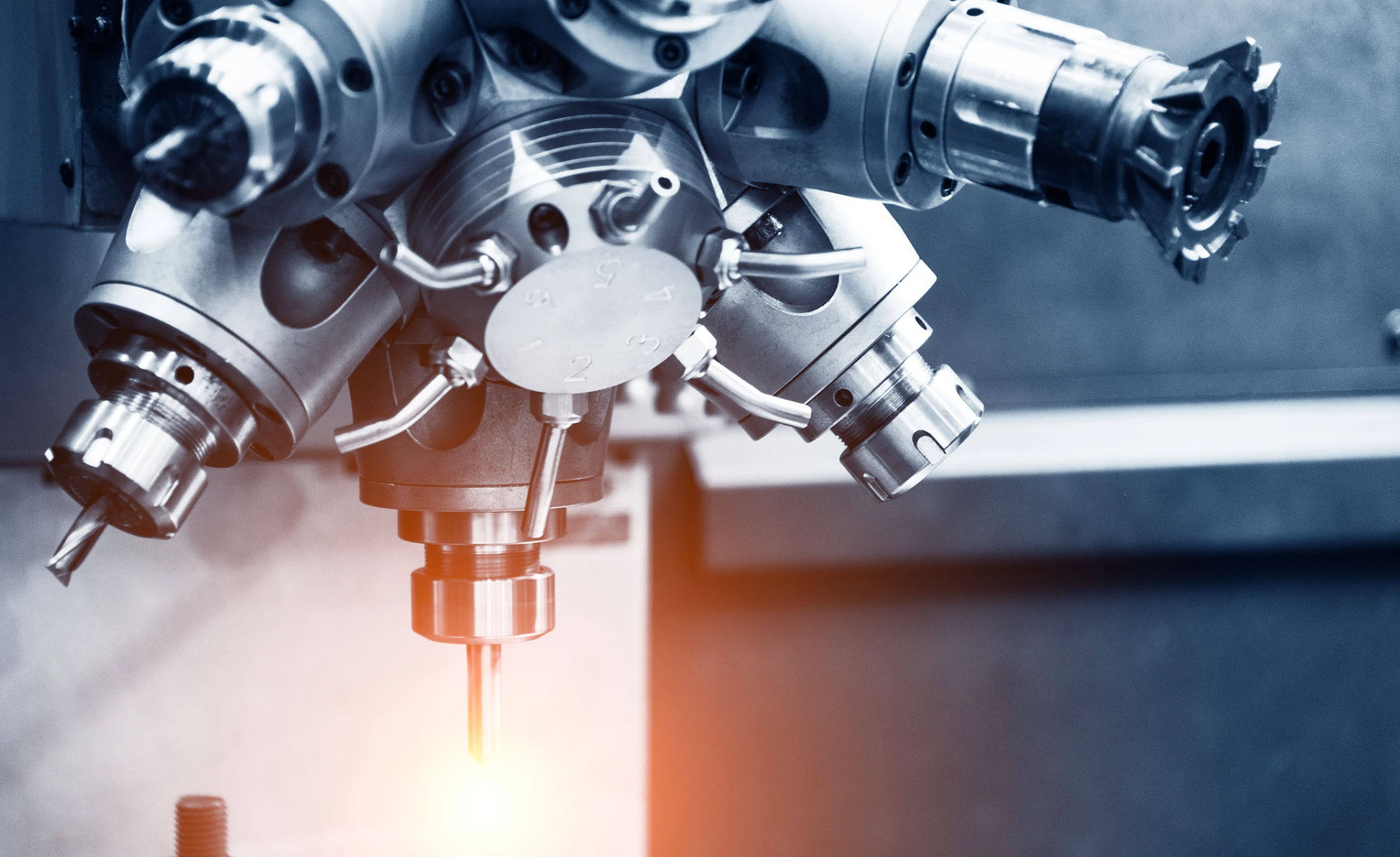
In the realm of metal casting, sand casting stands out due to its simplicity and adaptability. Essentially, sand casting involves creating a mold from sand and using it to form metal parts. The process begins with designing a pattern, which is typically made from wood, metal, or plastic. This pattern is then surrounded by compacted sand, forming a mold cavity that mirrors the item to be cast. Molten iron is poured into this cavity, allowed to cool, and upon solidification, the sand mold is broken to retrieve the cast piece.
One of the significant advantages of sand casting iron is its ability to produce complex geometries with relative ease. This attribute is especially valuable in industries such as automotive, where components like engine blocks and transmission cases require precision and durability. Sand casting facilitates the creation of intricate designs, accounting for changes in component dimensions as the iron cools and shrinks.
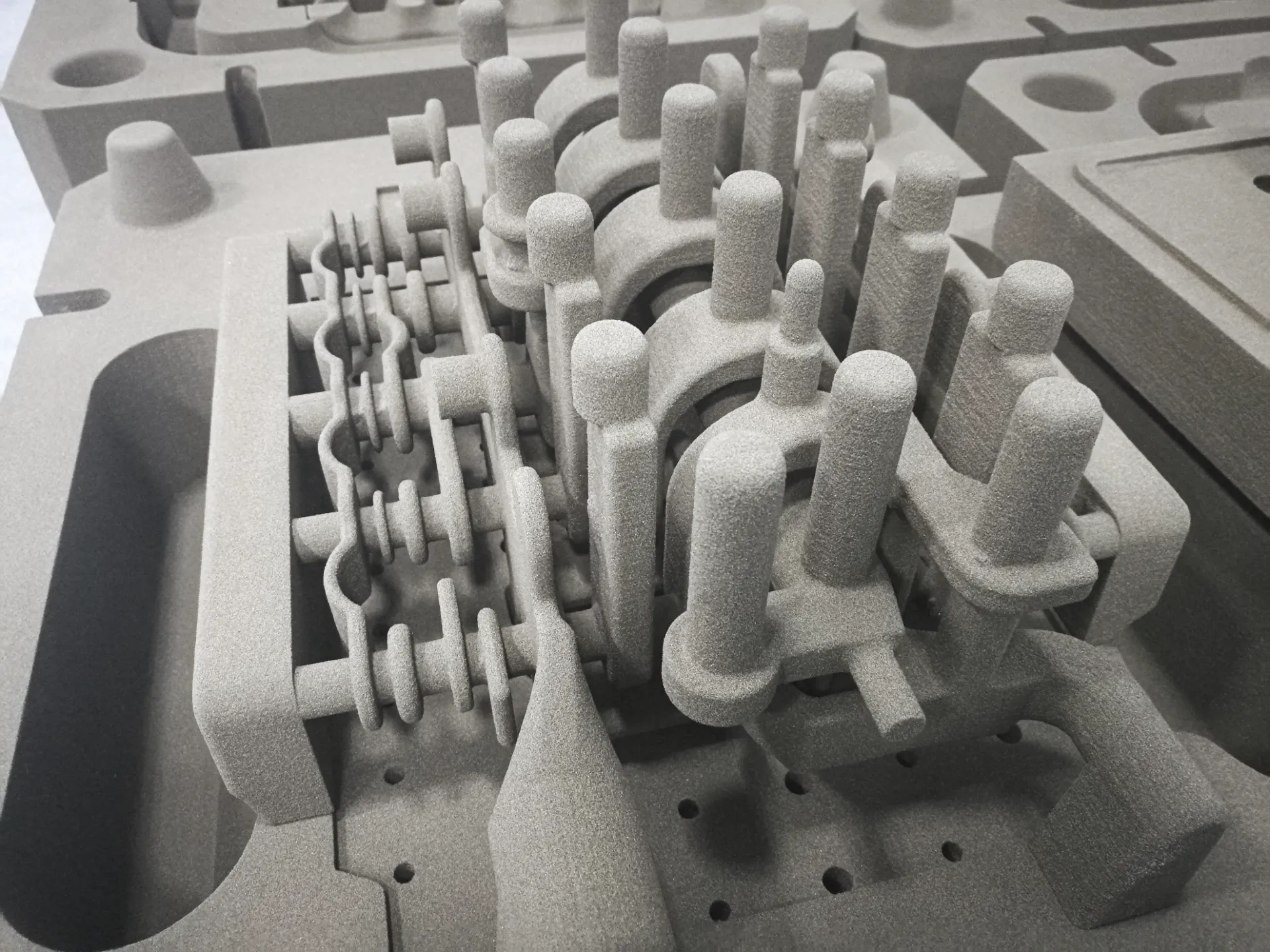
The economic aspect of sand casting cannot be overlooked. Compared to other casting methods such as die casting, sand casting is remarkably cost-effective. This is primarily because the materials used—sand and molten iron—are relatively inexpensive, and molds can be reused multiple times, minimizing waste. Moreover, it accommodates a range of production volumes, from small batches to large-scale manufacturing, without significant cost variation, making it an appealing choice for businesses of all sizes.
From an environmental perspective, sand casting iron offers sustainable opportunities. The sand used in the molds can often be recycled and reused, reducing the environmental footprint of the process. By implementing advanced sand reclamation techniques, manufacturers can further enhance the sustainability of sand casting, aligning with global efforts to promote eco-friendly industrial practices.
sand casting iron
Expertise in sand casting iron is pivotal for achieving optimal results in the production process. Operating at the intersection of art and science, skilled foundry workers bring both experience and technical knowledge to the table. Their proficiency in predicting how different alloys react during the casting process ensures that the final products meet rigorous quality standards. Furthermore, their ability to troubleshoot and refine casting techniques enhances the precision and reliability of the components created.
Industry leaders and seasoned engineers often turn to sand casting when faced with challenging production requirements. The authoritative nature of this method, backed by centuries of application and continuous innovation, lends credibility to its outputs. Manufacturers unveiling new or improved products frequently rely on sand casting to bring their visions to life, confident in the method’s ability to deliver authentic, high-quality components that withstand rigorous testing and usage.
Trustworthiness is arguably one of the most defining attributes of sand casting iron. The components produced through this method are known for their durability and strength, qualities that are essential in applications where safety and performance are paramount. By maintaining strict controls and adherence to quality management systems, sand casting operations ensure that every component meets the expected safety and performance benchmarks. As a result, clients and end-users have confidence in the integrity of products manufactured through this tried-and-true method.
In conclusion, sand casting iron remains a cornerstone of industrial production due to its unmatched adaptability, economic efficiency, and dependability. Its extensive history is a testament to its viability and efficacy, and ongoing advancements continue to refine the process, maintaining its relevance in the modern era. Whether for automotive, industrial, or artistic applications, sand casting offers a robust solution that caters to a wide array of production needs, ensuring it remains an authoritative and trusted method in the field of metal casting.