In the ever-evolving landscape of manufacturing, sand casting remains a foundational technique pivotal for creating complex metal components with cost-effectiveness and efficiency. Central to this process is the sand casting core, a vital component that facilitates the formation of intricate internal cavities in metal castings. As the industry advances, understanding the nuances of sand casting core technology not only elevates product quality but significantly enhances production efficiency.
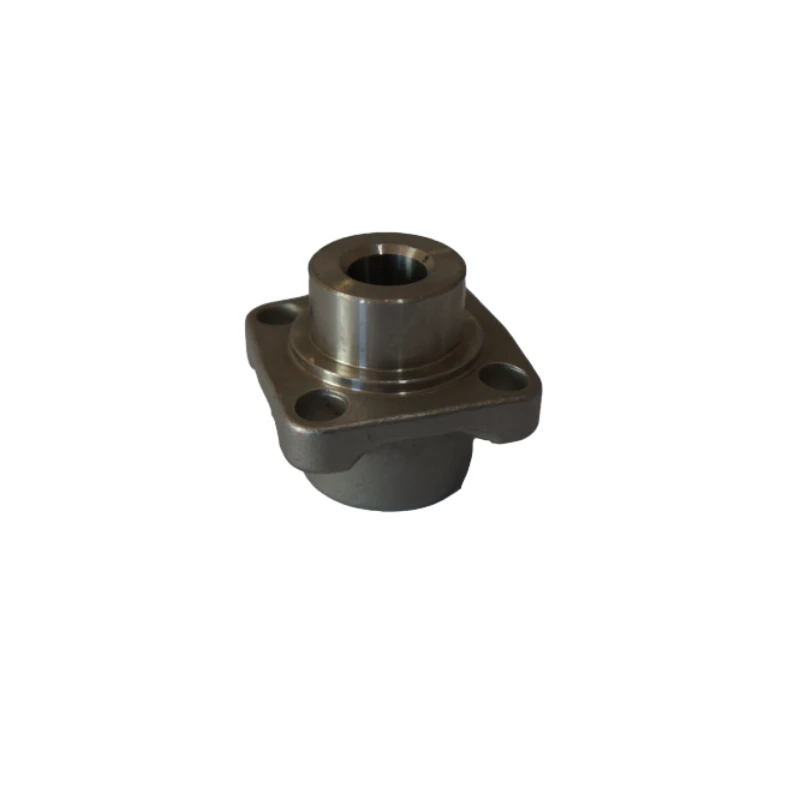
Sand casting cores are specially designed components formed from sand and binders, used to create intricate voids and passageways in cast metal parts. Utilizing specialized sand, often mixed with binders to strengthen the formation, the sand core ensures precise and accurate cavity formation within the mold. This technology is indispensable in producing parts for industries ranging from automotive to aerospace, where precision and internal complexities are paramount.
Expertise in sand casting core production involves a deep understanding of materials and techniques. Traditional sand typically consists of silica, although modern approaches incorporate chromite or zircon sands for enhanced properties, such as higher thermal resistance and lower expansion rates. Coupling these with sophisticated binders, such as phenolic resins or sodium silicate, ensures the core maintains integrity under the intense conditions of metal casting.
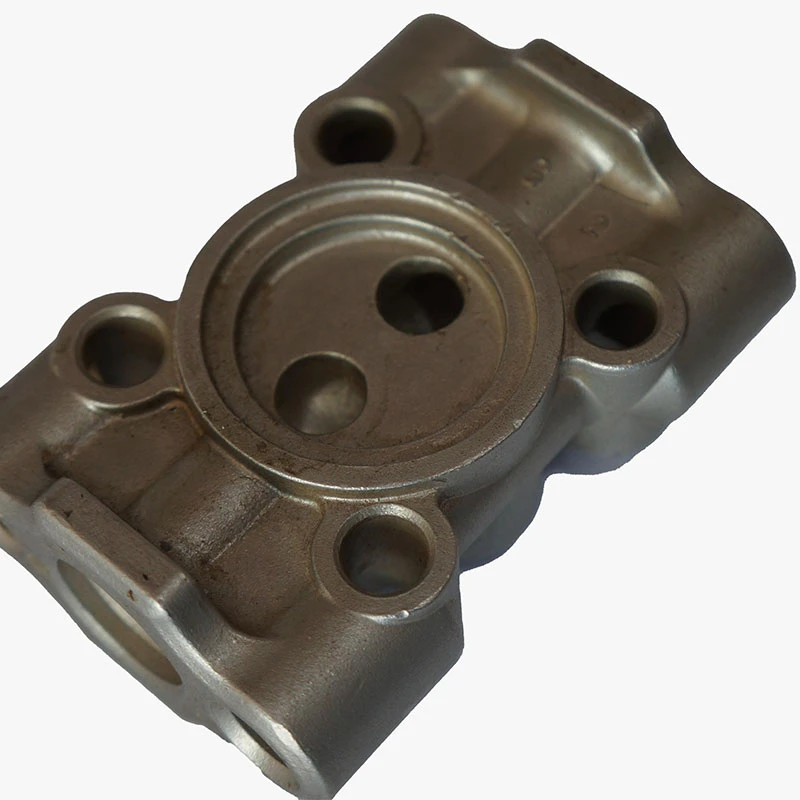
Creating a sand core begins with a design phase, where engineers meticulously design the core to meet the specific requirements of the casting. Computer-aided design (CAD) software plays a critical role in this stage, providing a virtual prototype that can be manipulated to optimize the casting process before moving into production. This digital model is then used to create a core box, a physical mold in which the sand core is formed.
The core box is crafted with precision, often using CNC machining or additive manufacturing processes to ensure exacting standards. Once the core box is prepared, the sand and binder mixture is introduced, compacted, and cured, forming a robust sand core ready for use. Employing cutting-edge curing techniques, such as cold-box or hot-box processes, enhances the durability and reliability of the core, ensuring consistent performance during high-temperature metal pouring.
sand casting core
A critical aspect of sand casting core production is maintaining a delicate balance between core strength and collapsibility.
Post-casting, the core must be easily removed without damaging the finished part. Innovative materials and techniques, such as heat-treatable binders and controlled collapsibility sands, have been developed to address this challenge, providing solutions that allow for easy removal while maintaining core integrity during metal pouring.
The implementation of sand cores in casting not only enables the production of complex geometries but also contributes to better material utilization and reduced machining requirements, translating to cost savings and increased production efficiency. Moreover, the advancement of environmentally friendly binders and reusable sand materials underscores the industry's commitment to sustainable practices.
Trust in the reliability and precision of sand casting cores is paramount. Industry standards and rigorous quality assurance processes ensure that each core produced meets stringent specifications. From the careful selection of raw materials to the detailed inspection of finished cores, every step in the production process is carefully managed to uphold the highest levels of quality and performance.
In conclusion, the sand casting core is a cornerstone of modern manufacturing, providing unparalleled flexibility and precision in creating complex internal geometries for metal castings. Leveraging the latest materials, technologies, and design methodologies, businesses can enhance product quality, reduce waste, and optimize overall production processes. As the industry continues to innovate, the role of sand casting cores will undoubtedly expand, delivering even greater efficiencies and capabilities for manufacturers worldwide.