Pressure die casting stands as a critical manufacturing process pivotal to producing complex metal parts with high precision and fine surface finish. Trusted by industries ranging from automotive to aerospace, pressure die casting offers unique advantages that can cater to large production runs with minimal waste.
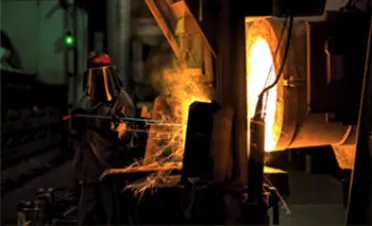
One compelling aspect of pressure die casting is its ability to produce intricate designs that would be challenging or impossible with other manufacturing methods. Manufacturers use this process to achieve parts with tight tolerances and fine detections, often requiring minimal secondary operations. The process begins with the selection of appropriate materials, usually non-ferrous metals such as aluminum, magnesium, or zinc, each bringing unique properties that benefit specific applications.
Aluminum, for example, is lightweight yet strong, making it ideal for automotive applications where reducing weight without sacrificing strength can lead to significant fuel efficiency gains. On the other hand, zinc alloys provide excellent thermal and electrical conductivity, suitable for electronic components which demand precision and reliable performance. The expertise of the die casting manufacturer becomes evident in selecting the right alloy and optimizing the design to exploit these material properties effectively.
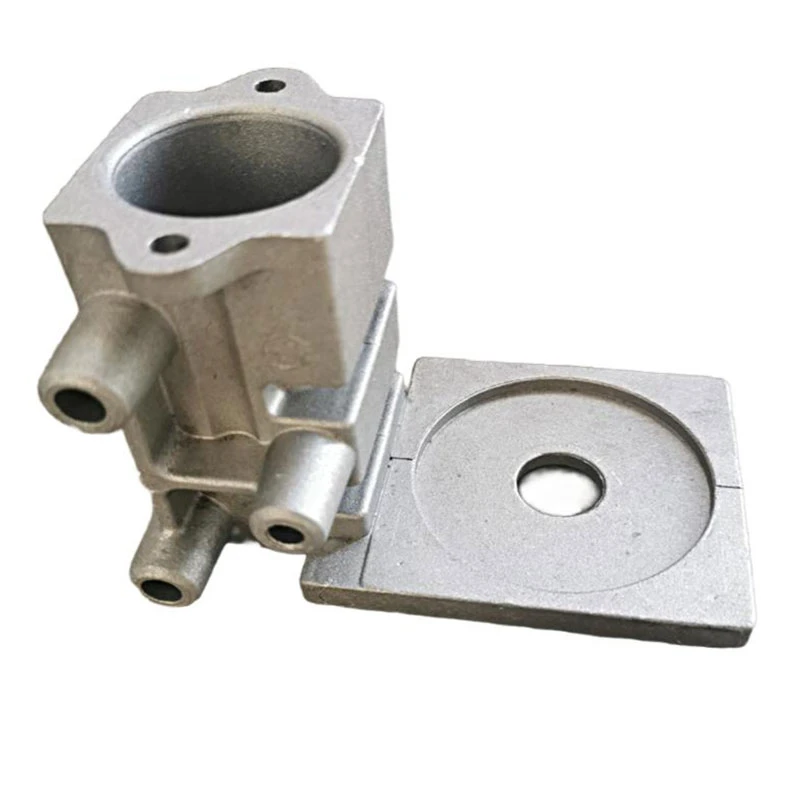
Precision in pressure die casting comes not only from the material choice but also from the equipment and technology employed. Top manufacturers leverage advanced die casting machines equipped with programmable logic controllers (PLCs) for precise control over every parameter of the casting cycle. This level of technological integration ensures consistent quality across production batches, highlighting the manufacturer's commitment to maintaining high standards.
Equally important is the design of the die itself. Manufacturers often engage in extensive simulations before creating the physical die to predict the flow and cooling patterns of the molten metal, ensuring minimal defects such as porosity or cracking. This reliance on computer-aided design (CAD) and computer-aided engineering (CAE) tools signifies a blend of traditional craftsmanship and modern technology, underscoring the expertise inherent within proficient die casting firms.
pressure die casting manufacturers
Furthermore,
a credible pressure die casting manufacturer emphasizes sustainability and environmental responsibility. The process inherently generates less waste than other methods due to the recyclability of scrap and excess material. By implementing rigorous quality controls and lean manufacturing principles, these manufacturers not only cut down material waste but also minimize energy consumption, adhering to global standards for environmental stewardship.
Innovations in pressure die casting extend beyond material choice and design precision. With the advent of Industry 4.0, manufacturers now harness data analytics and predictive maintenance to preemptively address equipment downtimes, further enhancing production efficiency. This transformation represents a significant leap in experience, as manufacturers adapt to newer technologies to remain competitive and deliver value to their clients.
While technological prowess and sustainability are key, the trustworthiness of a pressure die casting manufacturer also hinges on transparent communication and robust customer support. A reputed manufacturer is actively involved throughout the product development cycle, engaging with clients to understand their specifications and constraints fully. This collaboration results in parts that not only meet but often exceed expectations, ensuring products that deliver superior performance and safety.
Finally, what sets exceptional pressure die casting manufacturers apart is their authoritative presence within the industry. Such manufacturers often play a role in shaping industry standards, contributing to research and development, and sharing insights at international forums. This authoritative involvement provides them an in-depth understanding of emerging trends and technologies, reinforcing their position as industry leaders.
Thus, choosing the right pressure die casting manufacturer involves evaluating their experience, expertise, and track record of reliability. Prospective clients should consider firms known for their advanced capabilities, sustainable practices, and total commitment to quality and customer satisfaction. By doing so, businesses can ensure a harmonious partnership that yields high-quality, durable, and innovative products tailored to their specific needs.