Olivine Foundry Sand A Sustainable Solution for Modern Metal Casting
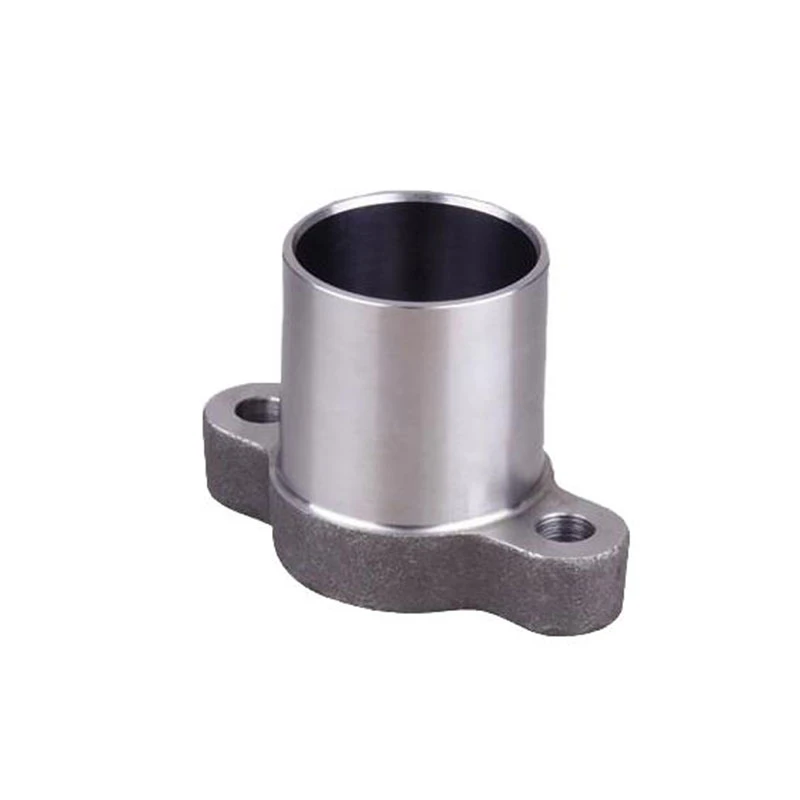
In the ever-evolving field of metal casting, manufacturers are constantly seeking materials that enhance performance while minimizing environmental impact. Olivine foundry sand stands out as an exceptional solution, offering unique advantages that cater to both operational efficiency and sustainability.
As an experienced foundry engineer with over two decades in the industry, I have witnessed firsthand the transformation that olivine sand brings to casting processes. With its high thermal resistance and low thermal expansion, olivine minimizes sand expansion defects such as veining, a challenge that plagues many foundries. Unlike silica, which can lead to thermal shock, olivine remains stable under extreme temperatures, ensuring cleaner castings and reduced waste.
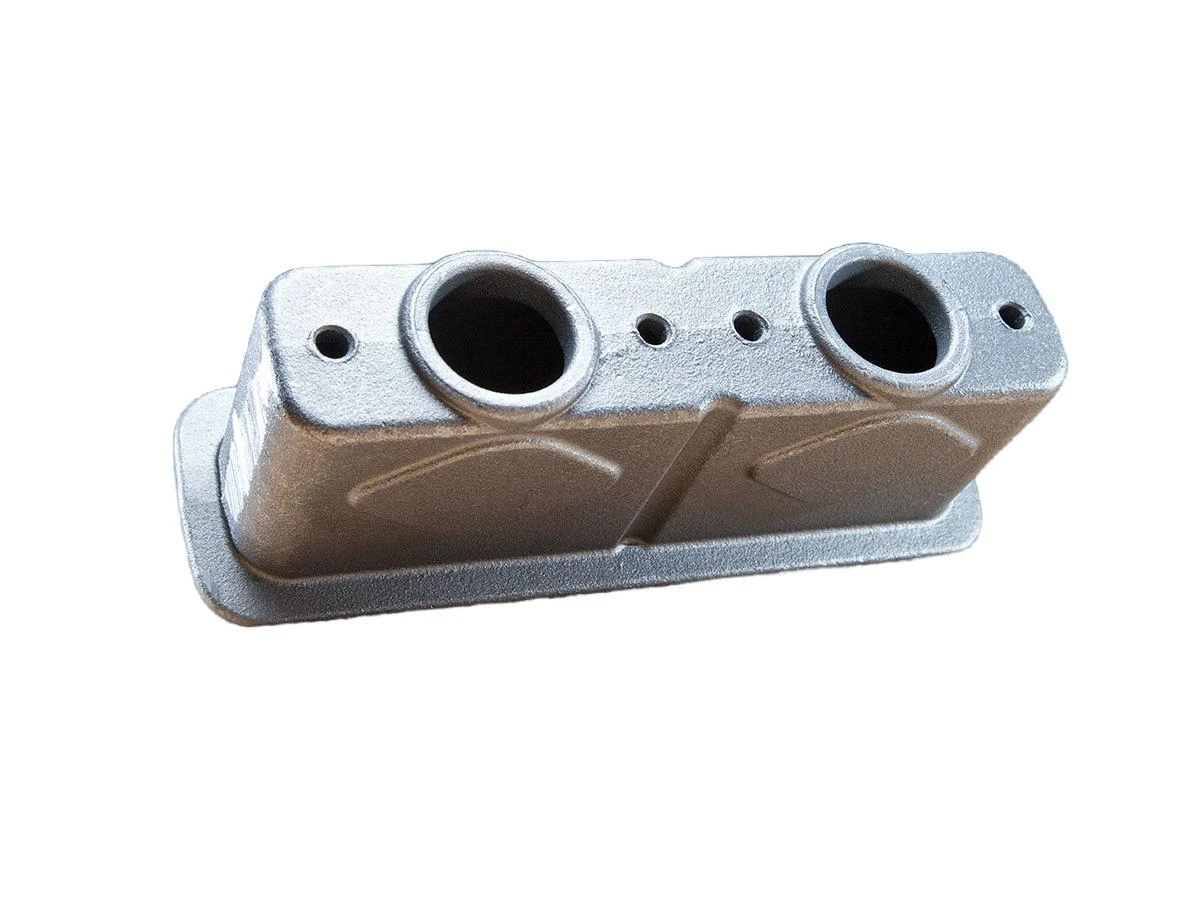
Olivine's physical properties are not its only beneficial aspects. Through years of research and application, it's clear that this naturally occurring mineral is not just a functional choice but an economical one. Its ability to maintain strength and integrity through multiple cycles reduces the annual sand expenditure, offering significant cost savings to foundry operations. The durability of olivine sand enables foundries to recycle it more effectively, further contributing to lower operational costs.
From an expertise perspective, olivine sand's chemical composition plays a crucial role in its advantages. Composed primarily of magnesium iron silicate, it does not produce free silica dust, a byproduct associated with health hazards in workers exposed to silica sand. This makes olivine a safer option for maintaining workplace health standards. Its inherent characteristics also simplify core removal, reducing labor costs and improving the overall efficiency of the cast cleaning process.
olivine foundry sand
Moreover, recognized authorities in the field, such as the American Foundry Society, endorse olivine as a sustainable alternative to traditional foundry sands. Numerous case studies corroborate these endorsements, highlighting olivine's reduced carbon footprint in foundry operations when compared to synthetic alternatives. Producing olivine sand requires less energy and releases fewer emissions, aligning perfectly with global efforts to reduce industrial environmental impact.
Trustworthiness in a foundry material comes from consistent performance across varied applications. My team's experience with olivine foundry sand across multiple projects has consistently shown improvements in casting surface finish and accuracy. Feedback from clients, ranging from small workshops to large-scale manufacturers, uniformly highlights enhanced product quality and customer satisfaction.
A real-world example comes from a medium-sized automotive parts manufacturer that transitioned to olivine foundry sand. Initially skeptical, the company took a phased approach, starting with non-critical components. The results were nothing short of impressive, with significant reductions in defect rates and an increase in final product integrity. Coupled with lower material consumption, the switch not only met but exceeded environmental compliance requirements, positioning the company as a leader in sustainable manufacturing practices.
In conclusion, olivine foundry sand is more than an alternative; it is a strategic choice for foundries seeking to combine environmental responsibility with operational excellence. Its established benefits, backed by expert research and authoritative endorsements, make it a reliable and trustworthy option for modern metal casting industries. By switching to olivine, foundries can achieve superior casting performance, optimize costs, and most importantly, play a part in fostering a sustainable future for the manufacturing sector.