Gravity die casting components represent a remarkable intersection of engineering precision and manufacturing excellence in modern industry. This manufacturing process, known for its ability to produce parts with superior mechanical properties and dimensional accuracy, has seen significant adoption across various sectors due to its versatility and reliability.
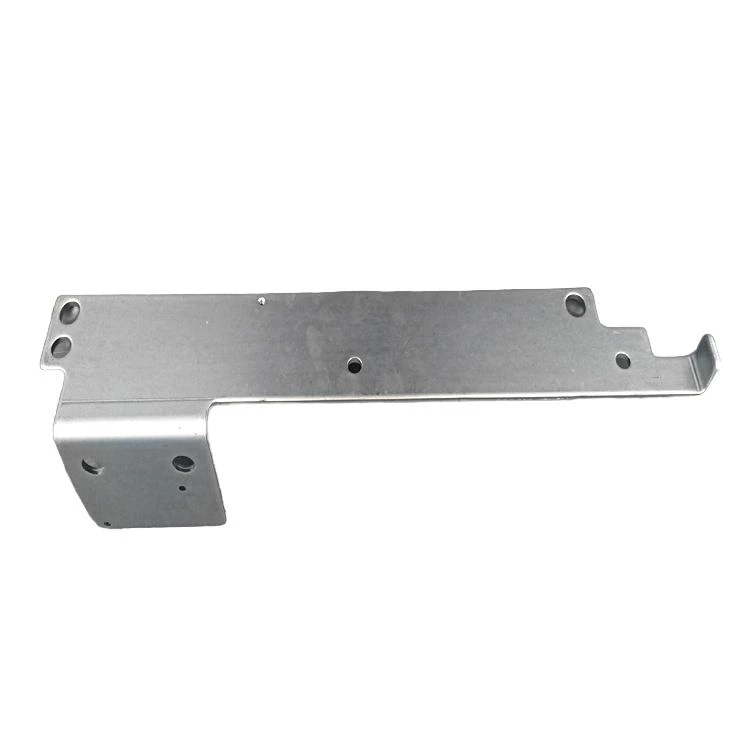
The gravity die casting process involves pouring molten metal into a mold cavity under the force of gravity, which is a distinct departure from other methods such as pressure die casting. This allows for a slower, more controlled fill of the mold and results in components with high structural integrity. Industries ranging from automotive to aerospace have benefited immensely from the capabilities of gravity die casting, making it a vital process for producing small to medium-sized batches where quality cannot be compromised.
One of the key advantages of gravity die casting is the quality of the finish and the strength it imparts to components. The method produces parts that are free of porosity, a common issue in other casting processes, resulting in high-density and durable products. For example, automotive manufacturers rely heavily on this process to produce engine components that can withstand high pressures and temperatures, ensuring safety and efficiency in their vehicles.
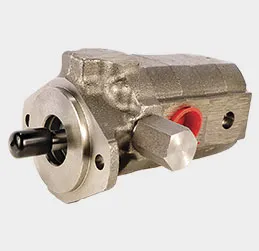
Moreover, gravity die casting provides excellent dimensional accuracy and a high level of repeatability, which are crucial in precision engineering tasks that require tight tolerances. This is particularly evident in the production of gear housings and other complex components where uniformity across parts is essential. The capability to achieve consistent part quality reduces the need for additional machining or finishing processes, saving both time and costs in the production cycle.
gravity die casting components
When discussing expertise in gravity die casting, it is important to consider the material selection and mold design, as these factors drastically affect the quality of the final product. An expert in this field understands that selecting the right alloy—be it aluminum, zinc, or another non-ferrous metal—can impact the component’s mechanical properties and its suitability for the intended application. Equally important is the design of the mold, which must account for metal flow, heat dissipation, and the desired shape and complexity of the component.
Working with an authoritative manufacturer who specializes in gravity die casting is crucial to achieving optimal results. These manufacturers employ cutting-edge technology and adhere to stringent quality standards, ensuring all components meet or exceed industry expectations. They often provide insights into the latest advancements in casting techniques and materials, ensuring that the products not only meet current demands but are also prepared for future challenges.
Trust in gravity die casting is built through consistent performance and component reliability. Manufacturers that follow systematic quality control processes—from initial design to the final inspection—reinforce confidence in the parts produced. High-quality gravity die casting components are less prone to defects, reducing the risk of part failure in critical applications and ensuring the longevity and durability expected from precision-engineered products.
As industries continue to evolve and demand more from their engineering processes, gravity die casting remains at the forefront due to its ability to deliver high-strength, precise, and reliable components. Whether the application requires parts for high-stress environments or detailed customizations, gravity die casting components offer a proven solution, leveraging the process’s innate strengths and the expertise of industry leaders to push the boundaries of what is possible in modern manufacturing.