Exploring the Intricacies of Hot Stamping Machine Parts
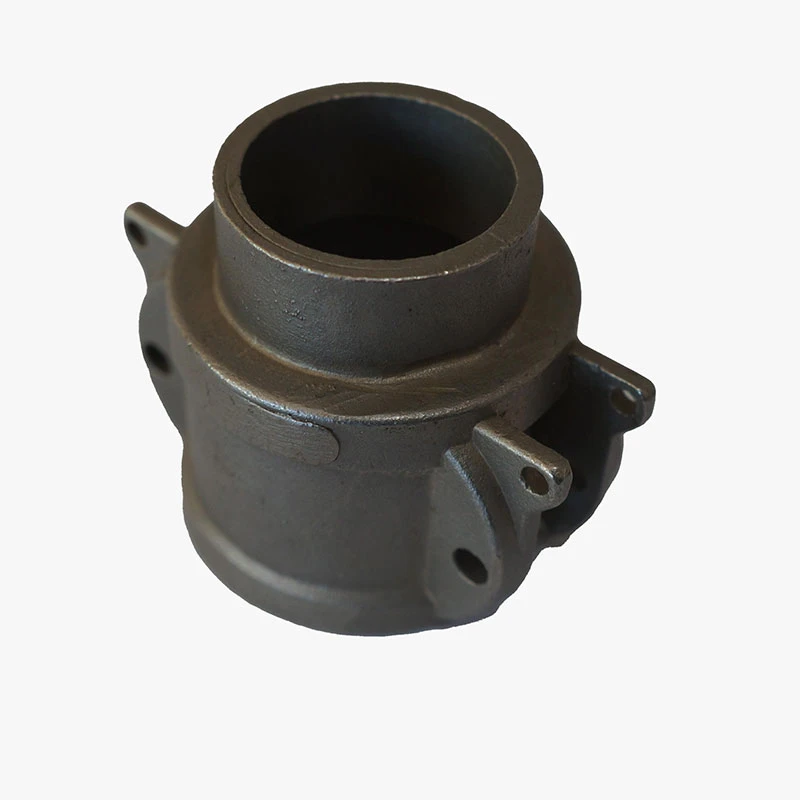
Hot stamping is a transformative process in the manufacturing industry, embedding intricate designs and texts onto various surfaces with precision and durability. The backbone of this advanced technology is its intricate machine parts, each engineered for seamless performance and longevity. Let’s delve into the world of hot stamping machine parts, exploring their functions, importance, and innovations that enhance user experience.
At the heart of any hot stamping machine is its die. This robust component, often crafted from brass, magnesium, or silicone, is crucial for transferring designs onto a substrate. Unlike traditional printing methods, where ink is merely applied on the surface, the hot stamping die employs heat and pressure to fuse the foil and the substrate, ensuring a long-lasting and smudge-resistant impression. The choice of material for the die often dictates the intricacy and detail of the designs that can be achieved. Brass, known for its durability and heat retention capabilities, is popular for detailed and high-volume applications, whereas silicone options are preferred for substrates with irregular surfaces.
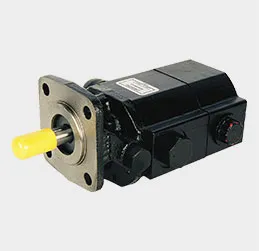
Precision in heat application is another critical factor in the effectiveness of a hot stamping machine. The heating plate, a key component, must distribute heat evenly across the die. Modern machines boast advanced heating elements controlled by sophisticated digital systems that regulate temperature with pinpoint accuracy. These systems ensure consistent results, reducing the need for rework and wasted materials, and enhancing overall efficiency.
Pressure application plays a vital role in the hot stamping process. The machine’s pneumatic or hydraulic press exerts force, driving the die into the substrate. This mechanism must be finely tuned to prevent excess pressure, which can damage both the substrate and the intricate designs of the die. Advances in pressure control systems now allow for precise adjustments based on substrate variability, providing reliable outcomes across different materials.
hot stamping machine parts
The foil feeding mechanism is yet another crucial part of the hot stamping machine. It ensures the continuous and accurate supply of foil to the die during the stamping process. Modern systems utilize servo motors and sensors that work in harmony to align foil precisely, reducing wastage and ensuring sharp edges in the finished product. This technology not only enhances the machine's efficiency but also improves the quality and consistency of the output, crucial for high-standard production environments.
An often-overlooked element of the machine's operation is its cooling system. Post-stamping, both the die and the substrate require rapid cooling to maintain shape and integrity. Effective cooling systems employ air jets and intelligent controls to quickly bring temperatures down to optimal levels, thus speeding up production cycles and preventing thermal stress on components.
Today's hot stamping machines also integrate advanced control systems for user-friendly operations. Intuitive interfaces, often with touch screen capabilities, allow operators to quickly adjust machine settings, monitor operation status, and troubleshoot issues with minimal downtime. The incorporation of automated features, such as self-calibration and real-time diagnostics, amplifies the machine's reliability and reduces the need for manual interventions, ensuring a smooth production flow.
The industry has seen significant innovations aimed at sustainability and efficiency. Environmentally friendly foils and energy-efficient systems are becoming standard, aligning with global ecological standards and reducing the carbon footprint of manufacturing processes. These advancements are complemented by enhanced machine durability, with parts engineered for longer life spans, reducing the need for frequent replacements and associated waste.
In conclusion, the nuanced interplay of components within a hot stamping machine underscores its significance in the modern manufacturing landscape. A deep understanding of these parts not only enhances operational efficiency and product quality but also contributes to sustainable practices in the industry. As technology continues to evolve, the spotlight on innovation in hot stamping machine parts will play a pivotal role in driving forward the capabilities and applications of this indispensable process.