High-pressure aluminum die casting represents a crucial evolution in modern manufacturing, providing a reliable method for producing complex metal parts with remarkable precision and strength. This technology stands out for its efficiency and cost-effectiveness, primarily when deployed at scale. Drawing from extensive experience in industrial applications and an expert understanding of material science, we reveal insights into this sophisticated process.

The journey of high-pressure aluminum die casting begins with choosing the right aluminum alloys that deliver desired qualities, such as lightweight, high thermal conductivity, and corrosion resistance. Popular alloys include the 380 and 6060 series, renowned for their malleability and durability. This selection requires an authoritative assessment to match specific industry needs, such as automotive, aerospace, or consumer electronics, where these components are omnipresent.
Before casting, creating the die — composed often of hard-wearing tool steel — is essential. The design of these dies is critical, involving expert CAD software analysis to ensure precision. The dies are carefully engineered for multiple uses, allowing for efficient production cycles. This step showcases expert knowledge of thermodynamics and metallurgy, as understanding how these metals flow and solidify under pressure is pivotal.
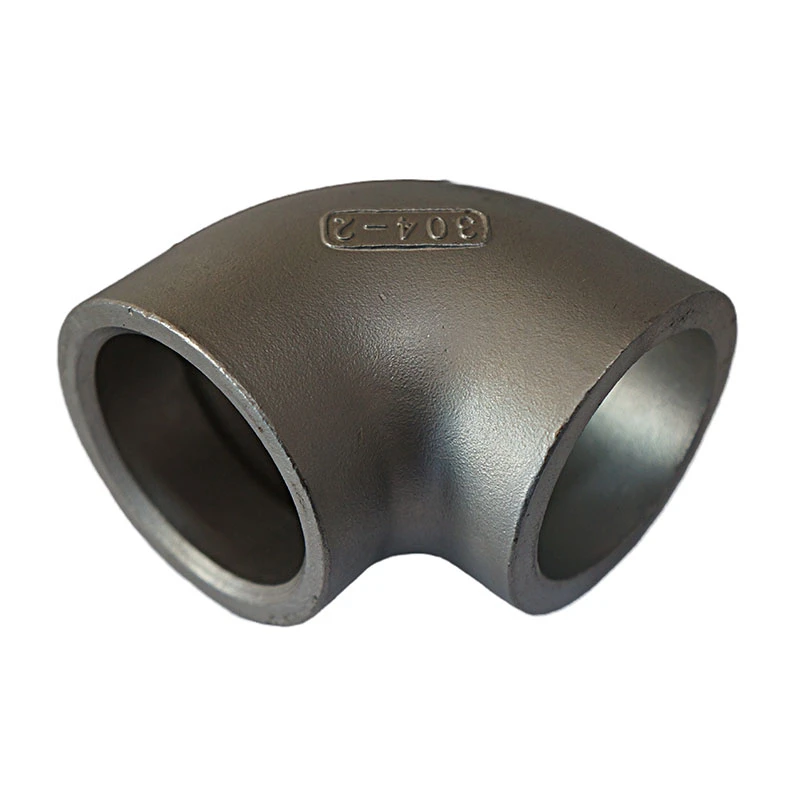
Once the materials have been prepared and the design approved, the casting process moves to the actual production phase. Aluminum is melted down at high temperatures and injected into the die using a powerful press. The high-pressure element ensures that the molten aluminum fills every crevice of the mold cavity, minimizing defects and maintaining a uniform structure. Experience dictates that controlling the injection speed and temperature is vital to produce a flawless finish and ensure the mechanical properties of the cast are preserved. This meticulous attention reflects authoritative practices that industry leaders rely on, reinforcing the process's reliability.
high pressure aluminum die casting
Operators, highly trained and experienced in managing these systems, are integral to maintaining production quality. They oversee the casting process, monitoring for deviations in pressure, temperature, and timing that could compromise the integrity of the finished product. This step encapsulates trustworthiness as operators must adhere to stringent quality assurance protocols to meet industry standards. Their expertise minimizes the rate of defective products, a critical factor in sectors like automotive manufacturing, where precision is non-negotiable.
After casting, secondary processes such as trimming, deburring, and heat treatment refine the shape and properties of the finalized component. Depending on the part's end use, additional treatments like anodizing or painting may be applied. Expertise in post-casting processes is vital, as these finishing touches not only enhance aesthetic appeal but also offer additional protection against corrosion and wear. This knowledge underscores the multifaceted expertise required in aluminum die casting and keeps operations effective and efficient.
The environmental impact of high-pressure aluminum die casting is another critical point of consideration. Aluminum's recyclability makes it an eco-friendly choice, aligning with global efforts toward sustainable manufacturing. Furthermore, the casting process is continuously evolving, with contemporary advancements aimed at reducing energy consumption and waste, driven by both technological innovation and regulatory mandates. Manufacturers committed to environmental stewardship invest in cutting-edge technologies that lower the carbon footprint of die casting activities, an authoritative assertion of responsibility towards sustainable practice.
In conclusion, high-pressure aluminum die casting is an unparalleled method for manufacturing complex, high-integrity parts. Its success lies in the application of deep material knowledge, design expertise, and precise engineering controls. Industries that invest in this technology benefit not only from enhanced product quality but also from a sustainable and economic manufacturing process. The combination of these factors cements the role of aluminum die casting as a pillar of modern industrial production, showcasing its enduring relevance and adaptability.