In the ever-evolving world of automotive engineering, the process of engine block sand casting stands as a cornerstone of precision manufacturing. This method, rooted in centuries of craftsmanship and innovation, continues to be a key component in the production of robust and reliable engine blocks for a variety of vehicles.
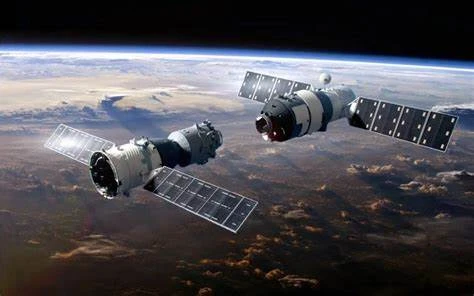
Sand casting, with its unique blend of artistry and engineering, begins with the creation of a mold. This mold is typically constructed using a mixture of sand, clay, and water, providing it with the necessary stability and permeability. The blend, meticulously curated by expert foundry specialists, ensures the mold's ability to withstand the extreme temperatures of molten metal while capturing the intricate details of the engine block design.
Expertise in this domain requires an intimate understanding of metallurgy.
Selecting the ideal metal alloy for the engine block is pivotal. Commonly used materials include aluminum and cast iron, each offering distinct advantages in terms of weight, strength, and thermal conductivity. Professionals in the field are adept at balancing these properties to meet specific performance criteria, ensuring the final product not only meets but exceeds industry standards.
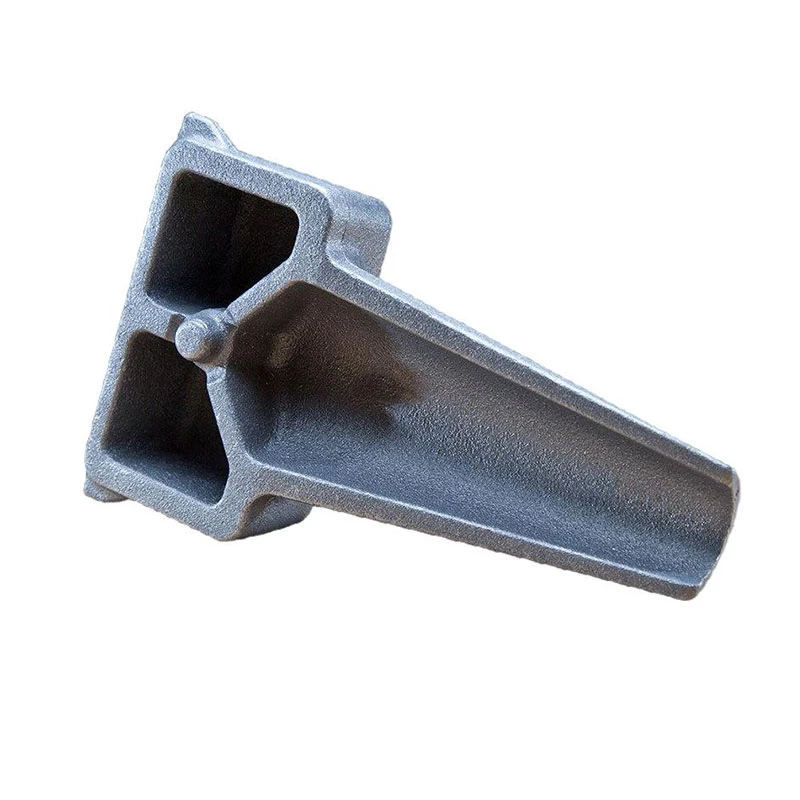
The process of pouring the molten metal into the sand mold is where experience comes into play. The temperature and speed of the pour are expertly controlled to avoid common pitfalls such as cold shuts, porosity, or the formation of undesirable microstructures. Skilled technicians are trained to monitor these variables closely, often using advanced computer modeling to predict and rectify issues before they arise.
engine block sand casting
Once the metal has cooled and solidified, the mold is broken away to reveal the raw engine block. This moment represents the culmination of precise planning and execution, a testament to the authoritative knowledge applied throughout the casting process. However, the journey is far from over. Rigorous quality assurance tests are conducted to detect any structural anomalies or defects that could affect performance. These tests, often employing state-of-the-art imaging technology, help reinforce trust in the manufacturing process, aligning with the highest standards of reliability and safety.
The final phases of production involve machining and finishing. Here, trustworthiness is further established as the engine block undergoes precision cutting and polishing. These processes are finely tuned to achieve the exact specifications required for seamless integration into a vehicle's engine system. The expertise of CNC machinists ensures that each engine block not only meets the physical dimensions but also adheres to strict tolerances that guarantee optimal performance.
In conclusion, engine block sand casting is not merely a manufacturing process; it is a confluence of tradition, technology, and expertise. Its enduring presence in the automotive industry is a testament to its effectiveness and the unwavering commitment of the professionals who champion it. With every engine block produced, sand casting reinforces its status as a trusted and authoritative method, delivering the power and reliability that drivers worldwide depend on.