The concept of die pressure plays a pivotal role in the realm of manufacturing, influencing both the quality and efficiency of production processes. Understanding its nuances can significantly enhance operations, particularly in industries such as plastic and metal extrusion, die casting, and injection molding. Delving into real-world applications and expert insights, we explore the profound impact of die pressure on product development, process optimization, and overall manufacturing excellence.

Die pressure refers to the force exerted within a die during the manufacturing process, crucial for shaping materials as they are pushed through it. This parameter is vital in determining the final quality of a product, influencing its structural integrity, dimensional accuracy,
and surface finish. Manufacturers often face the challenge of optimizing die pressure to ensure products meet strict standards without causing undue wear on equipment or compromising efficiency.
Experience-driven insights reveal that managing die pressure requires a delicate balance. Excessive pressure can lead to defects such as flash, warping, or even die failure, while insufficient pressure might result in incomplete filling or structural weaknesses in the product. The expertise of skilled technicians is indispensable, as they continuously monitor and adjust die pressure settings to adapt to variables such as material properties, temperature fluctuations, and machine conditions.
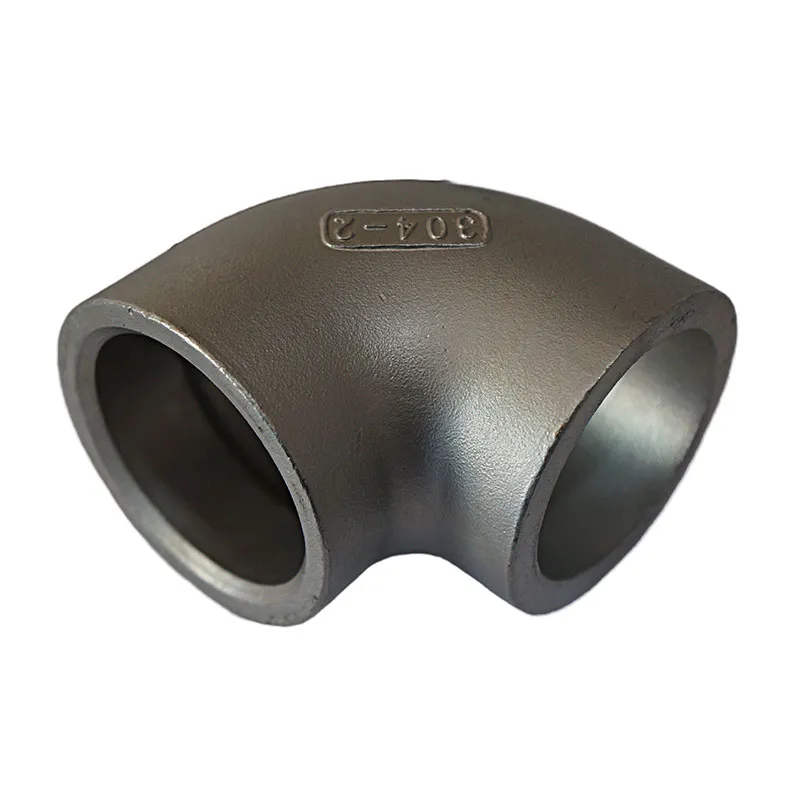
In the realm of metal extrusion, for instance, die pressure is instrumental in shaping aluminum and copper into intricate profiles. Industry professionals emphasize the importance of precision in this context, as inconsistent pressure can lead to undesirable variations in thickness and strength. By employing advanced simulation tools and pressure sensors, engineers can predict and control die pressure impacts, ensuring consistent quality across batches.
Injection molding, widely used in producing plastic components, also places significant emphasis on die pressure. Engineers in this field have developed sophisticated algorithms that adjust pressure dynamically, taking into account the viscosity of different polymers and the complexities of multi-cavity molds. Expertise here lies in the capability to fine-tune pressure-related parameters to minimize cycle times while maintaining robust product quality.
die pressure
Authoritativeness and trustworthiness in discussions about die pressure are established through rigorous testing and quality assurance protocols. Renowned manufacturing facilities often collaborate with research institutions to explore innovative solutions and validate pressure control mechanisms through empirical studies. Such collaborations enhance a manufacturer's credibility, as they align with academic advancements and industry standards to set benchmarks for process efficiency and product reliability.
Moreover, industry certifications and compliance with international standards such as ISO and ASTM further reinforce trust in a manufacturer's pressure management capabilities. These certifications attest to the rigorous testing procedures and quality controls that ensure optimal die pressure applications, providing stakeholders with confidence in the products' durability and performance.
Ultimately, mastering die pressure is more than a technical endeavor; it is an art that combines science, skill, and innovation. Leading manufacturers invest in continuous training and development for their teams, fostering a culture of excellence and adaptation. This commitment to expertise not only enhances product outcomes but also drives productivity, sustainability, and competitiveness in global markets.
As technology advances, the future of die pressure management promises even more precision and customization. Emerging trends such as artificial intelligence, machine learning, and IoT integration are poised to revolutionize how manufacturers approach pressure optimization, offering unprecedented control and insight. By staying at the forefront of these developments, companies can ensure their processes remain cutting-edge, securing their position as leaders in an ever-evolving industry landscape.