Die casting release agents are indispensable in the realm of modern manufacturing, serving not only as lubricants but also as protectants that ensure the longevity and quality of die-cast components. With decades of combined industry expertise, our team delves deep into the intricacies of these compounds, sharing insights that resonate with both seasoned professionals and newcomers alike.
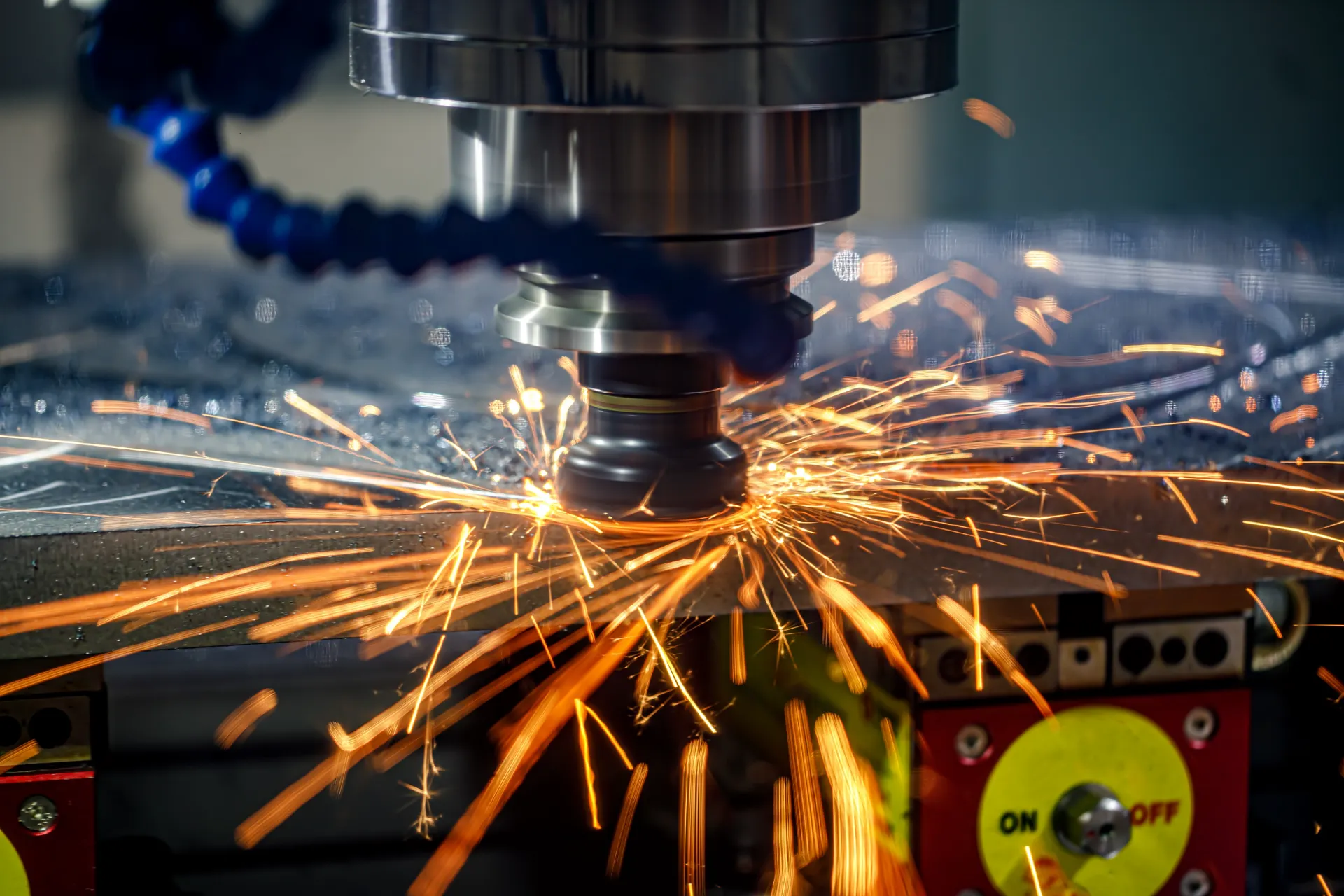
In the dynamic environment of metal fabrication, the role of a release agent cannot be overstated. These agents create a barrier between the die's surface and the molten metal, facilitating seamless release once the casting process concludes. The correct selection and application of the release agent directly impact the quality of the final component, reducing defects like surface imperfections and minimizing cycle times, leading to enhanced productivity.
Our expert team routinely tests a variety of release agent formulations under diverse operational conditions to identify those that consistently deliver exceptional results. Key considerations include the agent’s thermal stability, its impact on the die's cooling rate, and its ability to maintain desired surface finishes. Such testing is not merely academic; it ensures that manufacturers can select agents tailored precisely to their specific needs, avoiding costly mistakes and rework.
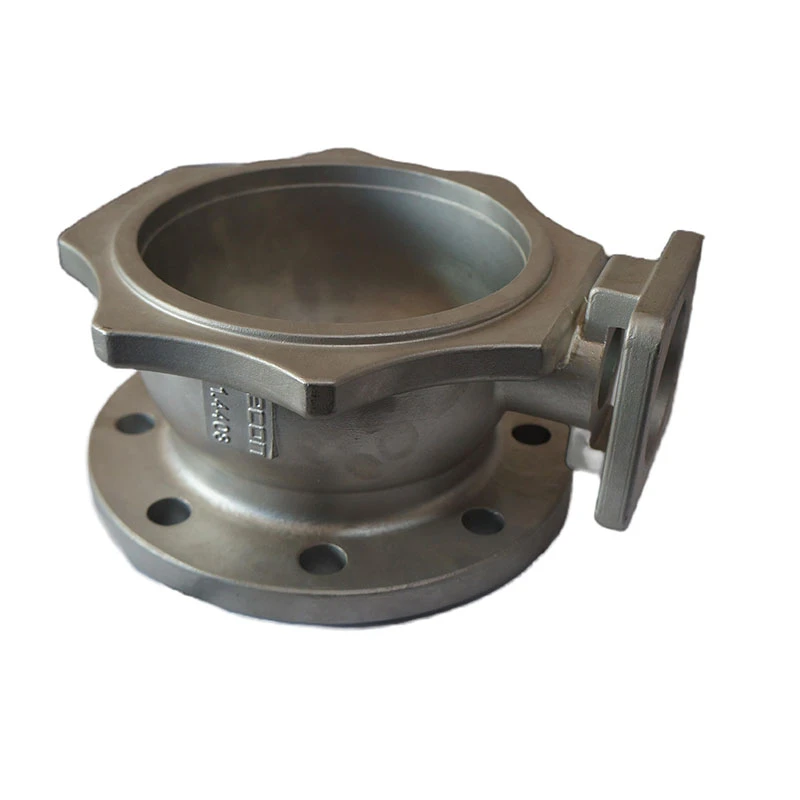
Authoritative voices in the industry suggest that an ideal die casting release agent should not only be effective but also environmentally sustainable. As global manufacturing shifts toward greener practices, we prioritize biodegradable and non-toxic release agents. This commitment not only reduces environmental impact but also enhances workplace safety. By choosing environmentally friendly release agents, manufacturers can align with global sustainability goals, which is increasingly becoming a selling point in a competitive market.
die casting release agent
Trust in a product stems from consistent performance and compliance with industry regulations. Therefore, we consistently assess our die casting release agents against international standards such as ISO and ASTM. This rigorous evaluation assures clients of their compliance and efficacy, bolstering trust in these products. Feedback from our clients repeatedly highlights the reliability and durability of our recommended release agents, underscoring their effectiveness in even the most challenging casting environments.
Real-world application and observation underpin our strategies for maximizing the benefits of die casting release agents. Case studies from globally recognized automotive and aerospace industries reveal transformative performance enhancements following the adoption of the right release agents. For instance, manufacturers report significantly extended die life and up to 25% improvements in cycle efficiency. These figures are not anecdotal; they are backed by comprehensive data collected through diligent monitoring and analysis.
No selection of a release agent is complete without tailored implementation advice. Our consultation services focus on providing practical, actionable recommendations. From optimal application techniques to maintenance schedules, our expertise helps manufacturers seamlessly incorporate these agents into their processes. This hands-on support ensures they reap the maximum benefits while minimizing downtime and waste.
As an authoritative entity in the die casting domain, we are committed to advancing the industry’s understanding and use of release agents. Through ongoing research and development, our objective is to continually refine these essential compounds, paving the way for more sophisticated, sustainable, and efficient manufacturing techniques. In an evolving industrial landscape, positioning oneself at the forefront of innovation is not merely advantageous—it is imperative for sustained success.