Understanding the cost per kilogram in die casting can be critical for making informed decisions regarding your manufacturing needs. Die casting is a versatile process known for producing complex shapes with a high level of detail. However, accurately estimating costs can greatly influence both budgeting and final product pricing. Here’s an expert breakdown of the factors influencing die casting cost per kilogram, emphasizing authenticity and credibility.
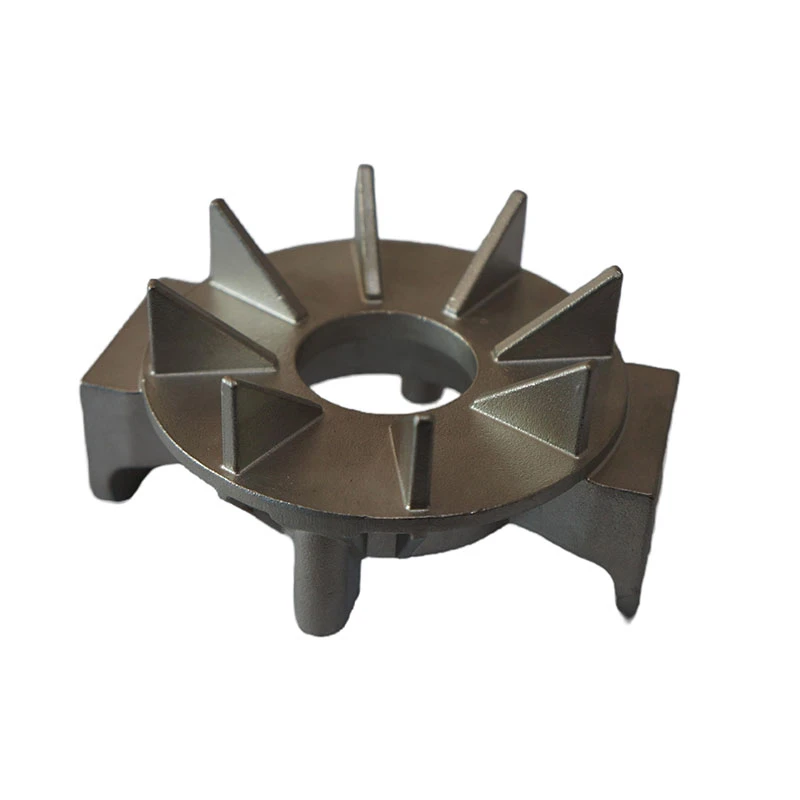
Die casting costs are driven by multiple factors including material type, complexity of the die design, production volume, and surface finish requirements. Each material, whether it’s aluminum, zinc, or magnesium, possesses specific properties that impact their cost. For instance, aluminum is often cost-effective due to its lightweight properties and ability to produce thin-walled components, while magnesium may offer lighter weights but at a premium price.
Design intricacy influences the die and tooling costs. Complex geometries require advanced engineering and precise hard tooling, which can elevate initial costs but may save money in high-volume production scenarios. In contrast, simpler designs may reduce upfront costs but potentially limit performance or features.
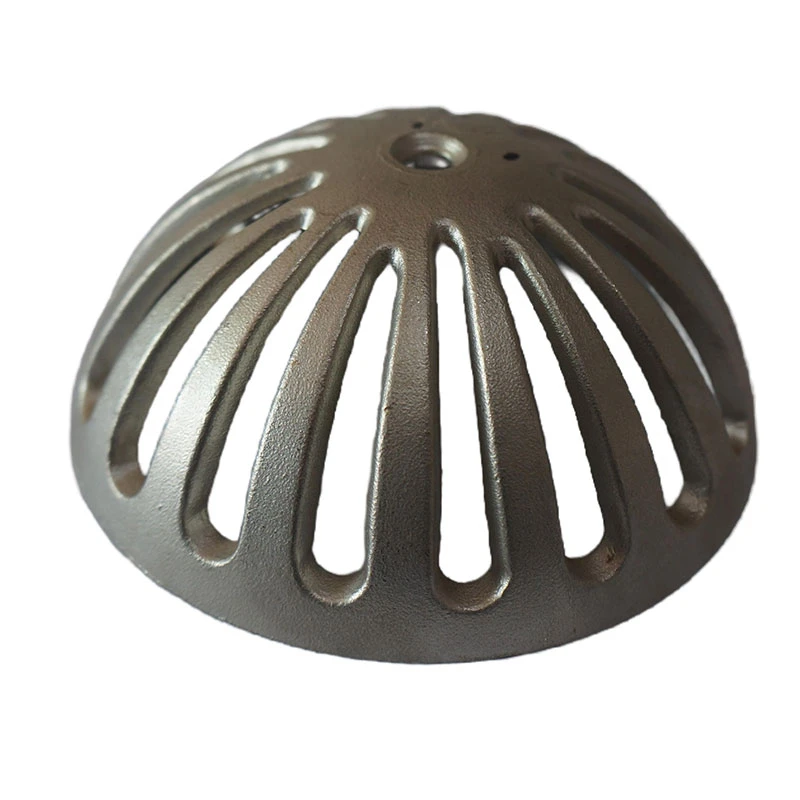
The production volume is another key factor. High-volume production generally reduces the cost per piece due to economies of scale, spreading the tooling and setup costs over a larger quantity. Specifically, in die casting, the break-even point is crucial for determining how the fixed costs will be amortized over production runs.
Surface finish requirements also play a pivotal role. Different finishing processes such as shot blasting, painting, anodizing, or powder coating can significantly add to the cost per kilogram. These finishes enhance the aesthetic appeal and durability of components but need to be weighed against the budgetary constraints and application needs.
Regression analysis and computer numerical simulations can further refine cost predictions. These tools model various scenarios, allowing manufacturers to anticipate costs accurately by factoring in variables such as cycle time, projected scrap rates, and energy consumption. Such analyses guarantee greater precision and reliability, establishing trust in estimates.
die casting cost per kg
High precision manufacturing businesses continuously monitor market trends and incorporate industry-based adjustments into their pricing models. This dynamic approach not only keeps them competitive but ensures that cost predictions remain as close to reality as possible.
The role of certifications and standards compliance, like ISO 9001 or IATF 16949, often contributes to the overarching cost structure. Certified manufacturers may exhibit slightly higher die casting costs per kilogram but generally promise superior quality assurance, offering peace of mind and reliability in high-stakes industries like automotive or aerospace.
Transport and logistics should not be overlooked, especially in global supply chain contexts. Differences in regional labor costs, tariffs, and shipping can drastically alter the final cost per kilogram if manufacturing is outsourced overseas versus done locally.
Price transparency and open communication with suppliers are critical for an accurate understanding of die casting costs per kilogram. Regular audits, agreements on detailed pricing breakdowns, and ongoing dialogue help maintain trust and iron out discrepancies that may arise during production or due to global economic changes.
Selecting an experienced die casting partner who prioritizes transparency, adherence to standards, and uses advanced technological supports in estimation and operations can optimize cost-efficiency. Achieving the perfect balance between initial investment and quality output ensures that businesses remain profitable while meeting quality and delivery expectations.
In conclusion, the intricate interplay of these factors makes understanding die casting cost per kilogram a task that demands expertise and a measured approach. Manufacturers focusing on experience, specialization, authority, and credibility stand in good stead to produce high-quality die cast components in a cost-effective manner, thereby enhancing their market competitiveness.