Die casting is a highly popular manufacturing process that is widely used across various industries to produce intricate metal components with excellent dimensional accuracy and versatile characteristics. While the technique offers exceptional advantages, such as high production rates and the ability to create complex geometries with precision, the success of any die cast component starts from its design phase. Adhering to established die cast design guidelines not only ensures the functional integrity of the final product but also enhances its manufacturability and cost-effectiveness.
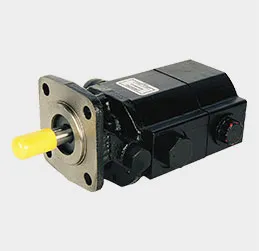
A fundamental principle in die cast design is maintaining uniform wall thickness whenever possible. This is crucial because it minimizes the occurrence of thermal variations and residual stresses within the casting, which can significantly impact the mechanical properties of the die-cast component. Having sections with inconsistent wall thickness can lead to issues such as warping, shrinkage, and even cracks. By ensuring a uniform wall thickness, the fill time is more consistent, and the likelihood of defects is minimized, which in turn enhances the product's reliability.
Another significant aspect is the use of draft angles on the casting surfaces that are perpendicular to the mold parting line. Draft angles facilitate the easy removal of the cast part from the die, reducing wear and tear on the die cast dies and ensuring the smooth operation of the production cycle. While the ideal draft angle may vary depending on the material and the intricacies of the design, incorporating even a minimal draft can greatly ease the ejection process and improve the surface finish of the final component.
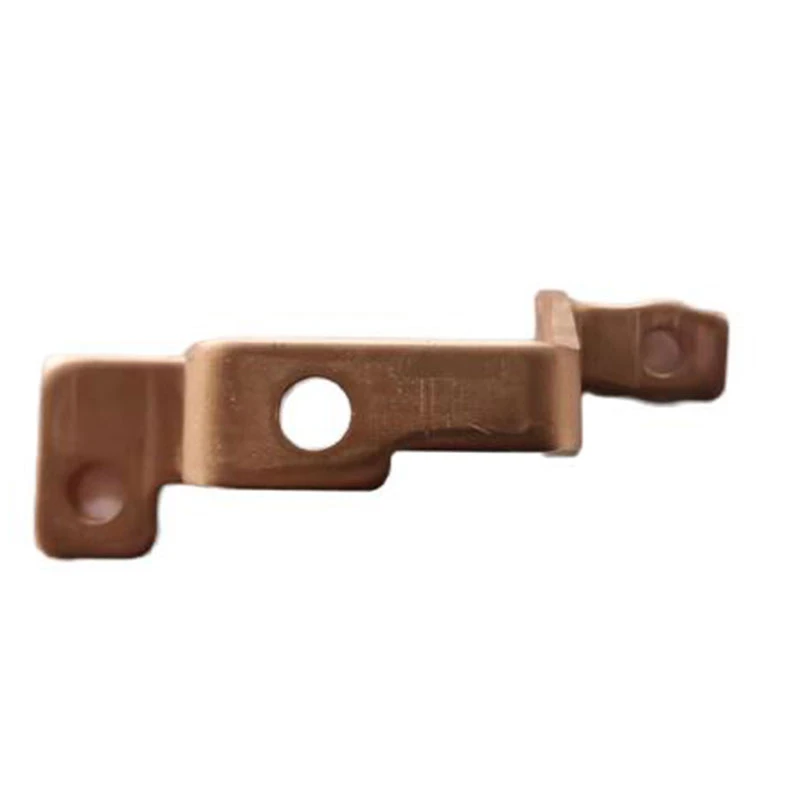
Incorporating adequate fillets and radii in the design is another pivotal factor. Sharp corners in a design can lead to stress concentration points, which may result in part failure under operating conditions. Rounded edges, in contrast, provide a smoother path for material flow within the die, reducing the risk of trapped air and other defects. Fillets not only enhance the part’s structural integrity but also improve the lifespan of the casting dies by minimizing stress concentrations and reducing erosion.
Optimizing rib and boss design is equally critical. While ribs are essential for providing structural strength without excessively increasing the weight of the part, they must be designed to prevent porosity and shrinkage cavities. A general design rule is to ensure that rib thickness does not exceed 60% of the adjoining wall thickness. Bosses, often used for mounting and fastening purposes, should be supported with ribs to distribute stress and prevent deformation.
die cast design guidelines
Attention must also be given to the gating and venting systems in the die cast design. Efficient gating design ensures that the molten metal fills the cavity in the most effective manner, reducing turbulence and air entrapment. Proper venting allows trapped air and gases to escape during the casting process, which is essential in preventing gas porosity defects. An expert understanding of flow dynamics within the die is imperative to develop an efficient system, optimizing the cycle time and ensuring a high-quality finish.
Another crucial consideration is the selection of materials. Each alloy used in die casting offers distinct advantages, whether it be aluminum, zinc, magnesium, or others. The chosen material should fulfill the required mechanical properties, corrosion resistance, and thermal conductivity for the intended application while also integrating seamlessly with the production process. An extensive understanding of material science is beneficial in making the right choice that aligns with the component's operational environment.
Effective communication and collaboration with die casting manufacturers can significantly aid the design phase. Leveraging the expertise of manufacturers can provide valuable insights into cost trade-offs, potential design modifications, and process limitations that may not be immediately apparent. Aligning with experienced manufacturers early in the design process can prevent costly revisions later and ensure that the design is optimized for manufacturability from the onset.
By embracing these die cast design guidelines, engineers can create high-quality products that meet dimensional tolerances and perform reliably in their intended applications. Integrating sound design principles not only benefits the product's performance and longevity but also supports cost-efficiency and sustainability throughout the manufacturing cycle. Ultimately, leveraging expertise and maintaining an open dialogue with manufacturing partners plays a critical role in converting innovative designs into successful die-cast products that cater to market demands effectively.