Die cast aluminum alloys have become fundamental components in modern engineering and manufacturing due to their versatility and impressive performance properties. These alloys are crucial in industries ranging from automotive to aerospace, where precision, durability, and light weight are highly valued. This article aims to deliver a comprehensive overview of die cast aluminum alloys through the lens of real-world applications, in-depth expertise, and authoritative insights, thereby enhancing your understanding and trust in using these materials for innovative product designs.
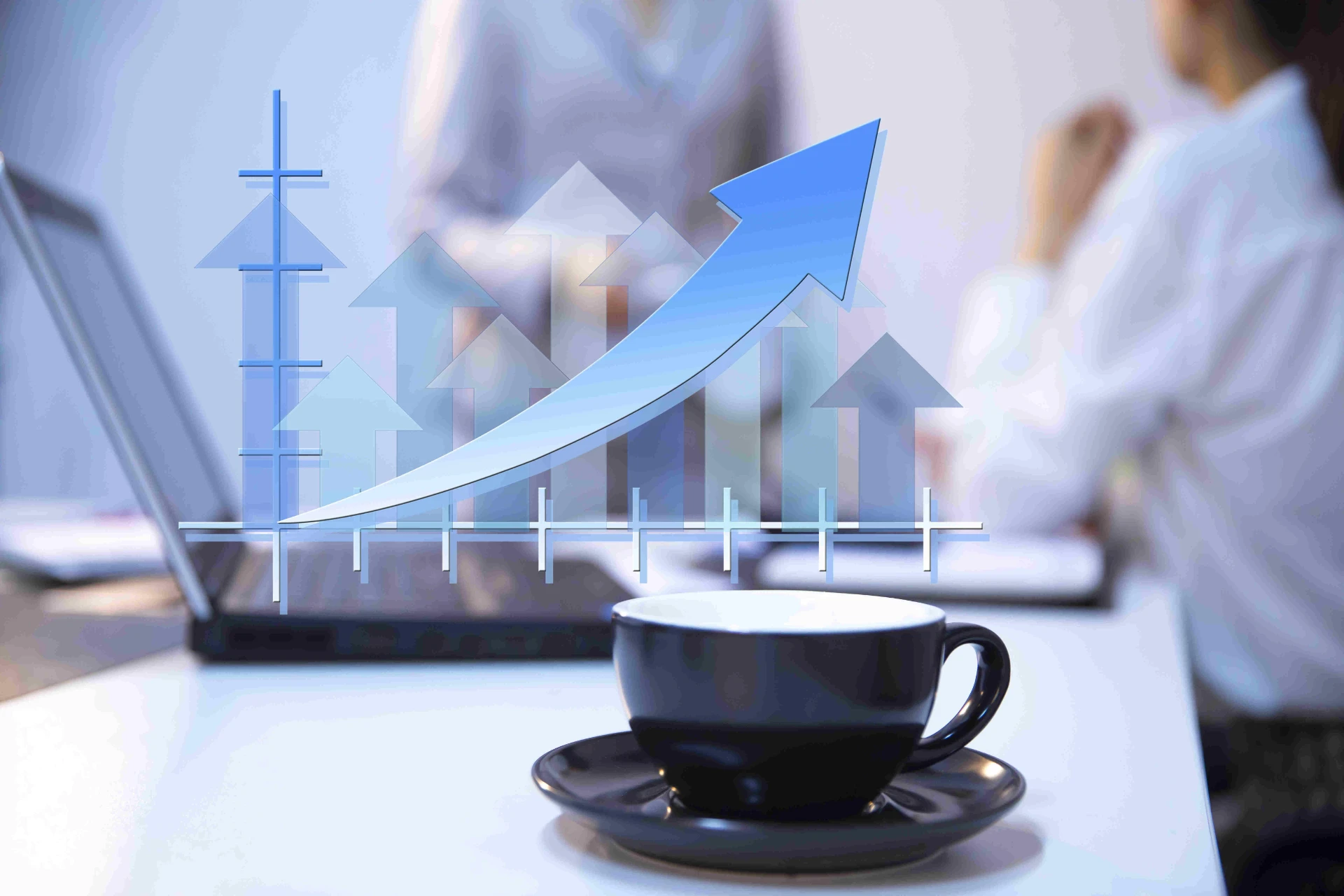
Die casting is a precision process where molten aluminum is forced into steel molds under high pressure. Among qualities that make aluminum alloys particularly suited for die casting are excellent corrosion resistance, high thermal and electrical conductivity, and superior finishing attributes. These characteristics make them an essential choice for producing parts that not only endure demanding environments but also align with aesthetic expectations, such as automobile components visible in car designs.
One prominent experience with die cast aluminum alloys is in the automotive industry, where they are extensively used to reduce vehicle weight, which in turn enhances fuel efficiency and performance. Automakers leverage these materials for engine blocks, transmission housings, and other critical components. For example, Ford’s experimentation with die cast aluminum in its EcoBoost engine components showcases real-world innovation that combines efficiency with sustainability by reducing the overall vehicle mass.
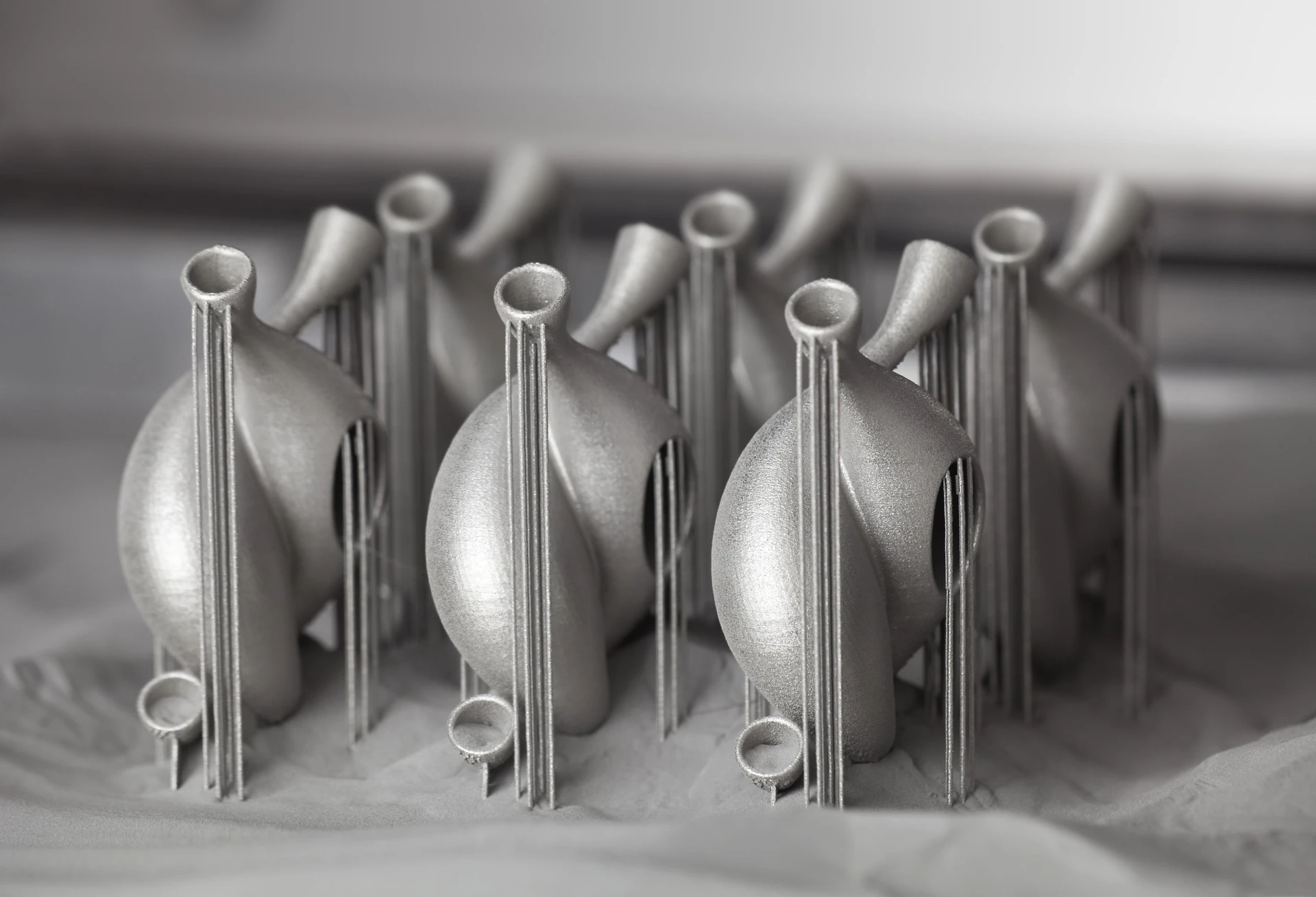
From an expertise perspective, the careful selection and application of specific die cast aluminum alloys can define the success of an engineering project. Alloys such as A380 are known for their excellent flowability, resistance to hot cracking, and mechanical strength, ideal for intricate and densely-packed components.
Additionally, ADC12 (also known as A383.0), with its enhanced corrosion resistance and quality castability, is another popular choice among engineers for manufacturing reliable components in corrosive environments.
die cast aluminum alloys
On authority and trustworthiness, decades of research have built a substantial body of knowledge regarding the efficacy and applications of die cast aluminum alloys. Standards bodies like the Aluminum Association and international entities such as ASTM provide detailed specifications and performance benchmarks for various alloys, ensuring that engineers and designers utilize materials that meet stringent safety and performance criteria. These standards help align global manufacturing practices, fostering trust across industries that rely on these materials for critical applications.
Moreover, sustainability plays an increasingly significant role in material selection, with aluminum alloys at the forefront due to their recyclability. Recycling maintains material properties without significant loss, thereby closing the loop in the material lifecycle and contributing to environmental goals without compromising on performance. Companies focusing on sustainability can lean on the established infrastructure for recycling aluminum, enhancing their eco-friendly credentials.
To further solidify trust and confidence among engineers and designers, case studies are beneficial. Consider Tesla's use of large die cast aluminum parts, referred to as 'megacasts', in the production of Model Y. This innovative approach reduces the number of individual components and assembly steps, optimizing manufacturing efficiency and structural integrity. Their documented success builds authority by demonstrating practical applications where theory successfully meets practice.
In conclusion, die cast aluminum alloys are indispensable in modern product development due to their mixture of mechanical properties, versatility, and sustainability. With extensive expertise guiding their use, and backed by authoritative standards and successful real-world applications, these materials are robust choices for forward-thinking companies and engineers. As industries evolve, aluminum die casting remains not only relevant but paramount, offering a trusted solution that meets contemporary challenges head-on.