Pressure die casting is revolutionizing modern manufacturing, combining speed, precision, and durability to produce complex metal parts essential for industries such as automotive, aerospace, and electronics. This advanced manufacturing process involves injecting molten metal into a steel mold at high pressure, allowing for the production of parts with exceptional dimensional accuracy and excellent surface finishes. Esteemed for its efficiency and cost-effectiveness, pressure die casting is distinguished by its ability to produce high volumes of uniform and intricate components.
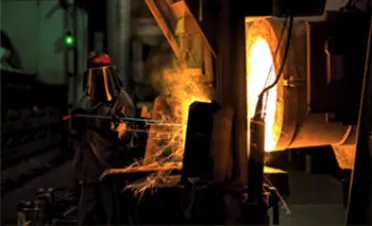
The pressure die casting process begins with the preparation of the mold, which is engineered to withstand repeated use and high temperatures. This mold, made from hardened steel, is crafted with precision channels to ensure proper metal flow and cooling. Once the mold is prepped, molten metal, often aluminum, magnesium, or zinc, is injected into it at pressures between 1,500 to 30,000 psi. The high-pressure injection allows the metal to fill all cavities of the mold,
capturing every intricate detail of the design.
Speed is a critical advantage of pressure die casting. The rapid injection and solidification process means a typical casting cycle can be completed in mere seconds. This quick turnaround is particularly beneficial for automotive manufacturers where demand for parts like engine blocks, transmission cases, and other components is high. The ability to produce large volumes of identical components with minimal machining reduces overall manufacturing time and costs.
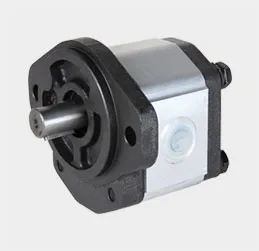
In terms of expertise, the success of pressure die casting depends heavily on the choice of materials and the design of the casting system. An expert understanding of metallurgical properties ensures the selection of the right metal alloys, which can withstand the specific environmental stresses of their intended applications. For example, aluminum alloys are chosen for parts that require lightweight properties and good thermal conductivity, whereas zinc alloys are selected for their excellent wear resistance and strength.
pressure die casting
The authoritativeness of pressure die casting is unwavering, supported by decades of technological advancements and broad applications across industries. Companies that invest in state-of-the-art die casting technology often lead the market due to their ability to produce superior parts more efficiently than competitors. Their extensive facilities are equipped with advanced CNC machines, robotic systems, and real-time data monitoring to ensure precise control over every aspect of the casting process. These features exemplify the commitment to maintaining high standards of quality and reliability.
Trustworthiness in pressure die casting focuses on consistent product quality and adherence to stringent industry standards. Certified die cast manufacturers are committed to quality management systems such as ISO 9001, ensuring every part produced meets specific performance criteria. Rigorous testing, including destructive and non-destructive methods, verifies that each component withstands the physical demands of its application. This reliability fosters long-term partnerships with clients who require precision parts with predictable performance.
Furthermore, environmental considerations are becoming increasingly important in pressure die casting. Advanced technologies like vacuum-assisted casting and automated lubrication systems reduce material waste and energy consumption. Moreover, recycling capabilities within the process make die casting a sustainable choice, aligning with global sustainability goals and reducing the carbon footprint of manufacturing operations.
In conclusion, pressure die casting offers unparalleled advantages in the production of high-quality metal parts, combining technical expertise with cutting-edge technology to produce components that are both durable and economically viable. By continuously pushing the boundaries of design and manufacturing, pressure die casting stands as a pillar of modern engineering, driving innovation and efficiency across critical industries.