Understanding porosity standards in aluminum casting is crucial for manufacturers seeking to produce high-quality, reliable products. The integrity and mechanical properties of aluminum castings are significantly influenced by the degree of porosity present. Porosity, a void within the metal matrix, can arise due to various factors including gas entrapment, shrinkage, and metal turbulence during the casting process. Addressing these issues is paramount for ensuring compliance with industry standards and enhancing product performance.
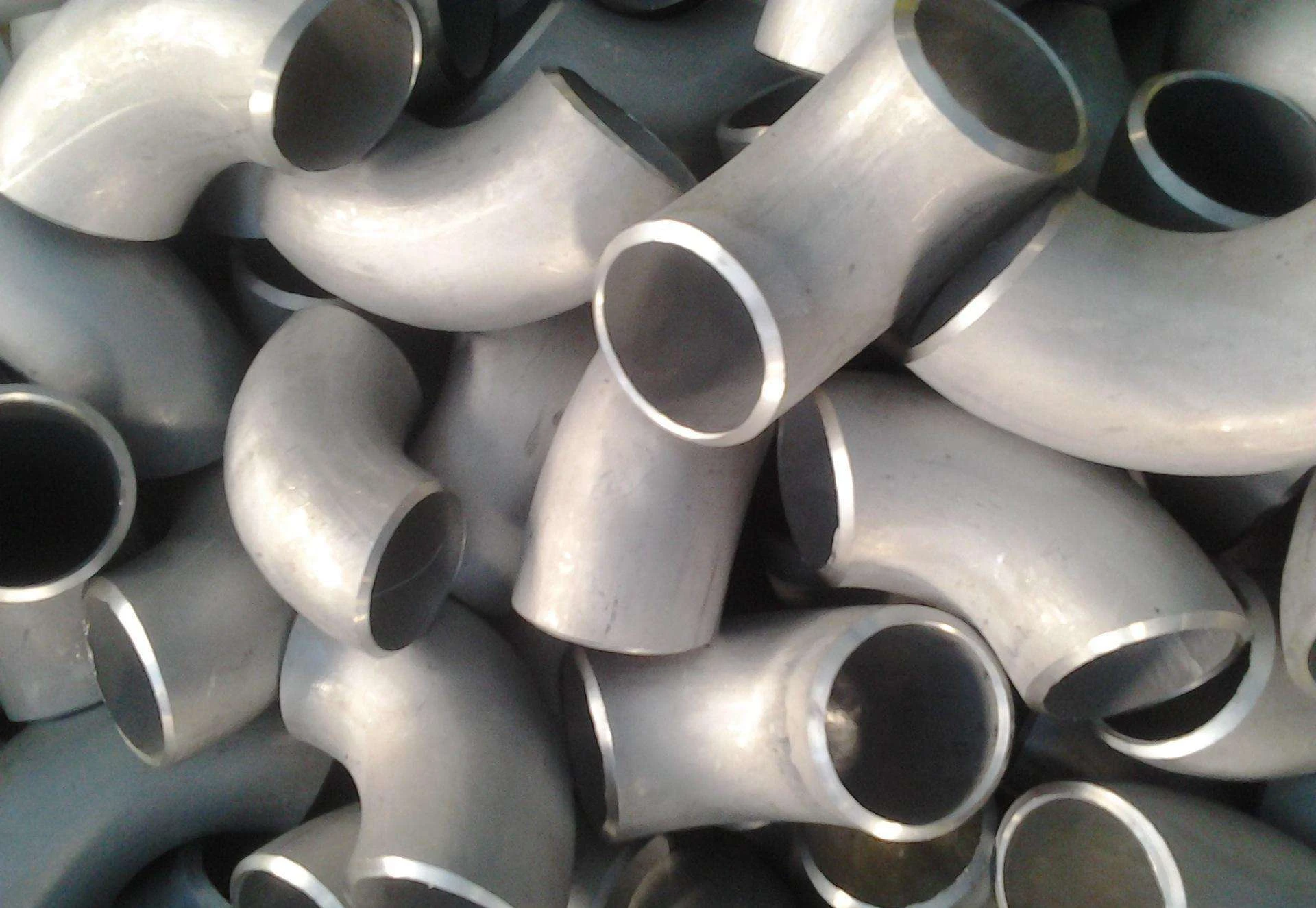
Industry standards for porosity in aluminum castings are set to guide manufacturers in maintaining optimal quality levels. Notably, standards such as those outlined by ASTM (American Society for Testing and Materials) and ISO (International Organization for Standardization) are widely recognized. These standards provide detailed specifications relating to acceptable levels of porosity, methods for testing, and guidance on corrective measures for mitigating excessive porosity.
Real-world experience in maintaining low levels of porosity revolves around meticulous process optimization. One effective approach is the careful management of the melt quality. Techniques such as degassing, filtering, and maintaining appropriate temperatures throughout the melting process can greatly reduce the risk of gas-related porosity. Moreover, employing computer-aided simulations helps predict potential porosity issues before production, allowing for preemptive adjustments to gating systems and mold designs.
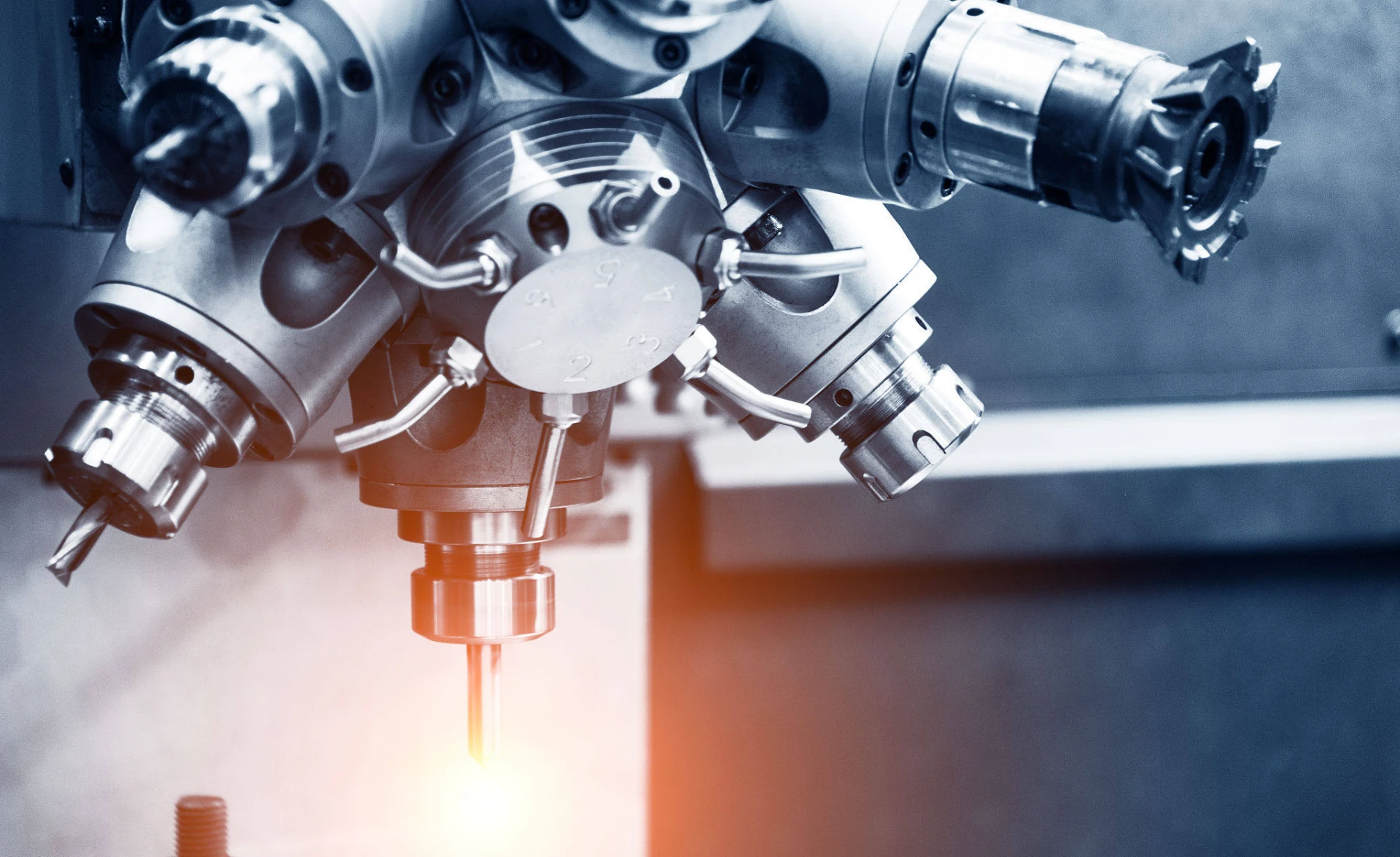
The expertise involved in aluminum casting extends to understanding the microstructural implications of porosity. Porous castings typically manifest reduced mechanical properties such as lower tensile strength and fatigue resistance. As a professional in this field, it is imperative to distinguish between macro and micro porosity, with the latter being more challenging to detect yet critically affecting the product's structural integrity. Advanced non-destructive testing (NDT) methods like X-ray radiography and computed tomography provide invaluable assistance in detecting and evaluating the magnitude and distribution of porosity within castings.
porosity standards in aluminium casting
Furthermore, maintaining authoritative knowledge in the latest advancements in casting technologies is essential. Innovations such as vacuum-assisted casting and high-pressure die casting offer superior control over porosity levels, yielding denser, stronger, and more reliable aluminum components. Regularly updating technical knowledge and participating in industry workshops and seminars contribute significantly to maintaining a competitive edge.
From a trustworthiness perspective, adherence to porosity standards directly influences the reputation and reliability of aluminum cast products. Manufacturers who rigorously follow standards not only ensure the production of components with superior quality but also instill confidence among clients and end-users. It is beneficial for manufacturers to document their quality control processes and results, demonstrating a commitment to transparency and excellence.
In summary,
porosity standards in aluminum casting are an indispensable aspect of producing high-caliber, durable products. By leveraging extensive experience and technical expertise, and adhering to recognized standards, manufacturers can effectively manage porosity, leading to enhanced product quality and strengthened market trust. Ensuring these elements are at the forefront of production strategies is key to achieving sustained success in the competitive field of aluminum casting.