High pressure die casting (HPDC) has long been valued in the manufacturing industry for its ability to deliver high precision and durability in metal components. This article offers a deep dive into the intricate calculations essential for optimizing HPDC processes. Through years of experience and industry expertise, these insights can significantly elevate the quality and efficiency of die casting operations.
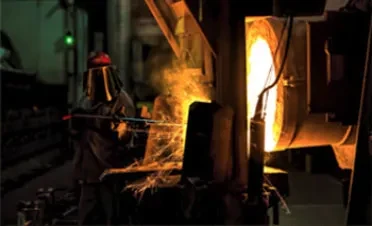
The cornerstone of successful high pressure die casting lies in the meticulous calculation of parameters which influence the yield and quality of the casted parts. Central to this is understanding the alloy's behavior under high pressure. Various factors, such as melting temperature, fluidity, and thermal expansion, must be quantitatively assessed. These properties directly affect the filling time and cooling rate, critical parameters in minimizing defects like porosity and cold shuts.
Begin the process by establishing the precise melt temperature suitable for the alloy in use. Common alloys like aluminum, magnesium, and zinc have distinct profiles—aluminum, for instance, requires a higher melting point compared to zinc. An authoritative approach involves utilizing data from material data sheets and testing under operational conditions to define the exact melt temperatures.
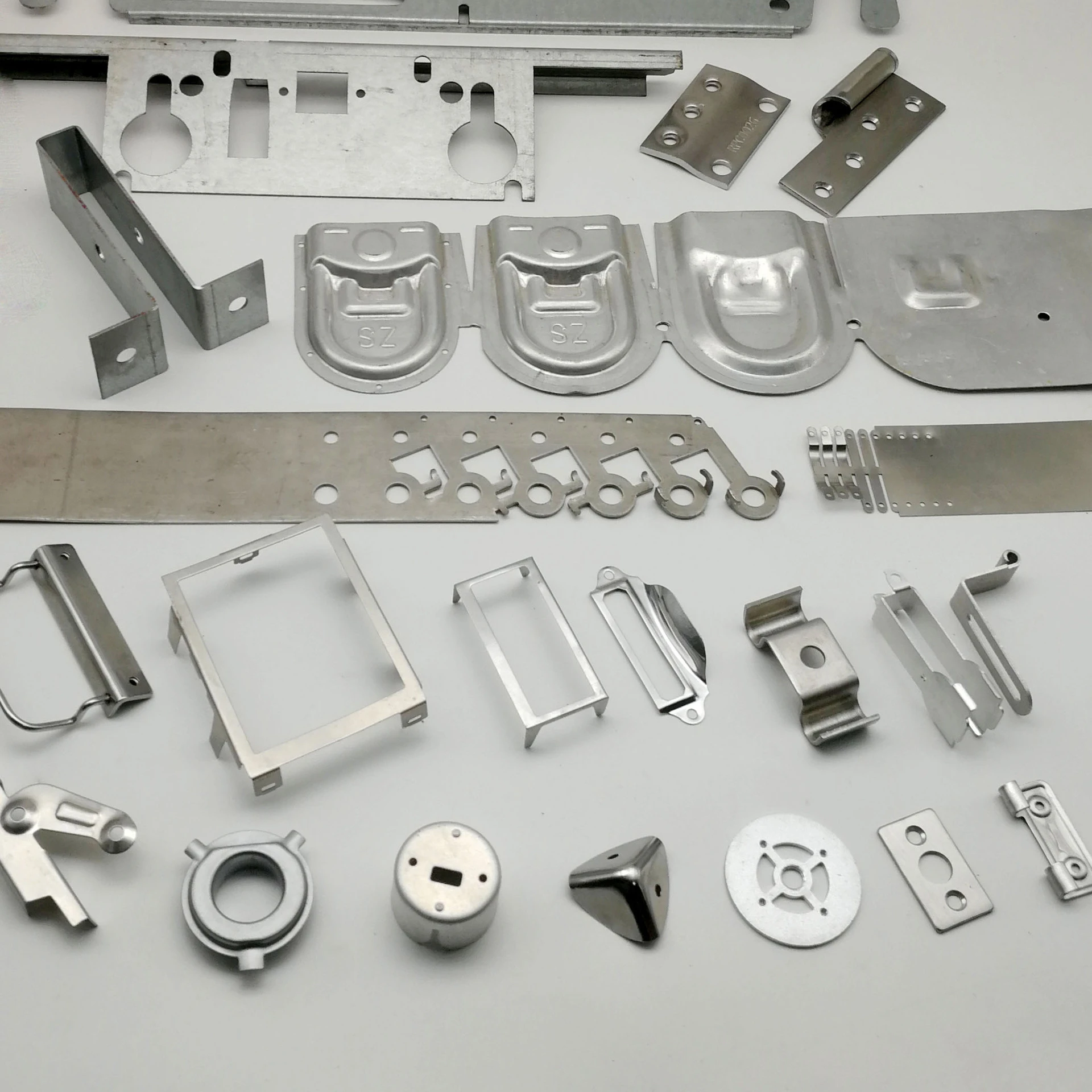
The die filling time calculation is pivotal. A comprehensive understanding involves employing empirical formulas that consider gate velocity, fluidity of the alloy, and the complexities of cavity geometry. These calculations help in estimating the optimal injection speed and pressure. For example, a typical formulation might factor in the shot weight divided by the gate area, modified by an efficiency coefficient derived from historical performance data.
high pressure die casting calculation
Attention must be paid to the cooling phase, crucial for achieving the desired microstructure and mechanical properties. The cooling rate directly influences grain size and, consequently, the strength of the cast component. This phase demands calculating the heat transfer rate from the molten metal to the die material; measurements often incorporate both conduction and convection parameters that vary based on the die material composition, such as H13 tool steel commonly used in HPDC.
Particularly authoritative insights into die casting are often garnered through simulations pre-production. Employ advanced software to model casting scenarios—these simulations can predict potential defects, allowing for preemptive adjustments in design or process parameters. Utilizing Finite Element Analysis (FEA) in simulations adds a layer of precision to your planning by testing multiple scenarios without the cost and time of trial runs.
Trustworthiness in HPDC calculations also hinges on rigorous documentation and analysis of past project performances. Detailed records facilitate continuous improvement and training modules for new engineers. An efficient feedback loop involving regular auditing of metal quality, equipment calibration, and process control metrics is indispensable. This methodical approach guarantees reliability in manufacturing, prevents unnecessary resource expenditure, and ensures customer satisfaction.
High pressure die casting is not merely a process of manufacturing; it's a science balanced with the art of predicting and controlling variables. Establishing authoritative expertise in this field requires not only the fundamental calculations but also an ongoing commitment to refine techniques based on empirical evidence and technological advancements. Through these calculated methodologies, organizations can excel in producing superior cast components that meet stringent industry standards.