Fine casting sand, often considered the unsung hero in metal casting, stands out as a crucial component in producing high-quality metal products. From its composition to the unique advantages it offers, exploring the realm of fine casting sand unveils a world marked by precision, innovation, and enduring craftsmanship.
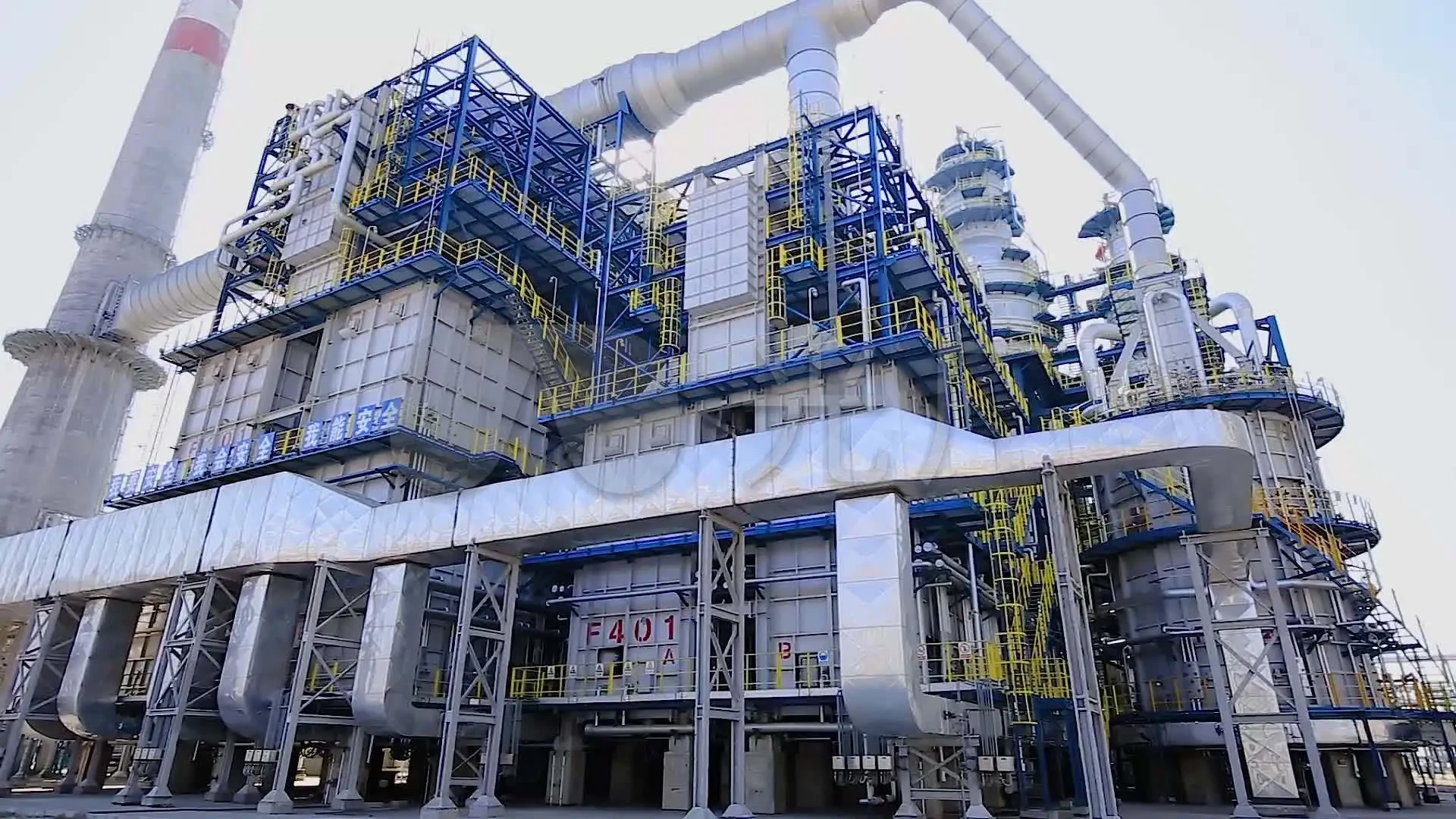
Understanding the Composition
Fine casting sand is typically made of high-grade silica, combined with bonding agents to create a mixture that is both malleable and resilient under high temperatures. The granularity of this sand is meticulously controlled, allowing for the creation of flawless molds. Unlike regular sand, the fine particles allow for intricate detailing essential in modern casting techniques.
Experience in Use
In the world of metal casting, the significance of the right type of sand cannot be understated. Veteran foundry engineers often testify to the fact that the quality of casting sand directly influences the texture and structural integrity of the final product. The fine granules fill the smallest voids in the mold, ensuring that even the most complex designs are captured accurately.
This results in castings that need minimal machining, thereby reducing both cost and production time. Through decades of refinement, many foundries have developed proprietary blends of fine casting sand, tailored specifically to their unique production needs, illustrating the practical experience-driven innovation in this field.
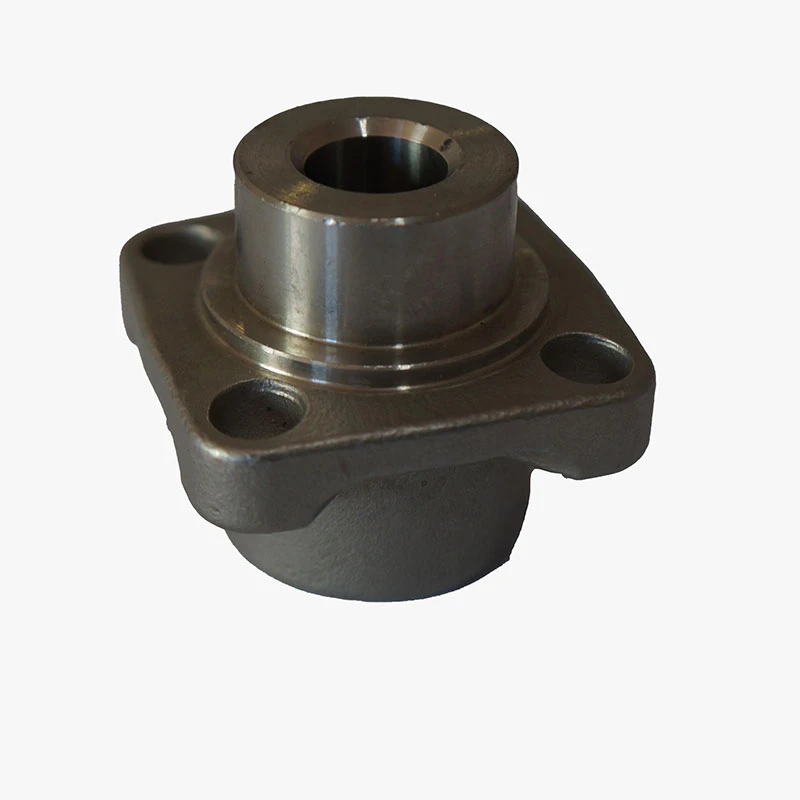
Technical Expertise
Engineers specializing in metallurgical processes emphasize the technical superiority of fine casting sand. Its thermal conductivity and refractory properties make it ideal for high-temperature applications, preventing deformation or any unwanted reactions during the casting process. Furthermore, the controlled grain size distribution is critical in minimizing metal penetration and ensuring a smooth surface finish. This level of expertise requires meticulous selection and testing of sand batches, often conducted in advanced laboratory settings. The result is a material that can withstand the rigors of modern manufacturing while adapting to various metals such as iron, brass, and aluminum.
fine casting sand
Authoritative Insights
Studies by leading industrial research organizations confirm that fine casting sand significantly enhances casting quality. Published papers in engineering journals detail the economic advantages brought by reduced waste and lower defect rates. Experts from academic institutions also contribute to this body of knowledge by collaborating with industry players to innovate and test new formulations. These authoritative figures highlight the role of fine casting sand not just as a material, but as a critical enabler of industrial efficiency and product excellence.
Building Trust
For manufacturers and artisans alike, trust in the materials used is paramount. The reliable performance of fine casting sand has established it as a cornerstone in various manufacturing industries. Testimonials from industry leaders and quality assurance certifications further bolster trust, ensuring that users can confidently predict outcomes and timelines. Traceability of the sand, from extraction to processing, is rigorously documented, providing further assurance of its consistent quality.
Innovative Applications
Beyond traditional foundry work, fine casting sand is finding innovative applications in art and design. Artists appreciate its ability to capture fine details and textures, which translates beautifully into metal sculptures and decorative pieces. This crossover into non-industrial sectors showcases its versatility and potential for creative applications.
In conclusion, fine casting sand is more than just a component in metal casting; it represents a fusion of art and science, experience and expertise. Its role in modern manufacturing is solidified by the trust it has earned from professionals worldwide. As industries continue to evolve, the adaptability and reliable performance of fine casting sand will undoubtedly support future advancements, maintaining its indispensable status in the world of metallurgical engineering.