Die casting, an advanced manufacturing process for producing complex metal parts, is valued for its precision and efficiency. Understanding the types of die casting is essential for those involved in the manufacturing and engineering industries. This in-depth analysis explores various die casting methods, highlighting the unique benefits, applications, and technical distinctions of each type.
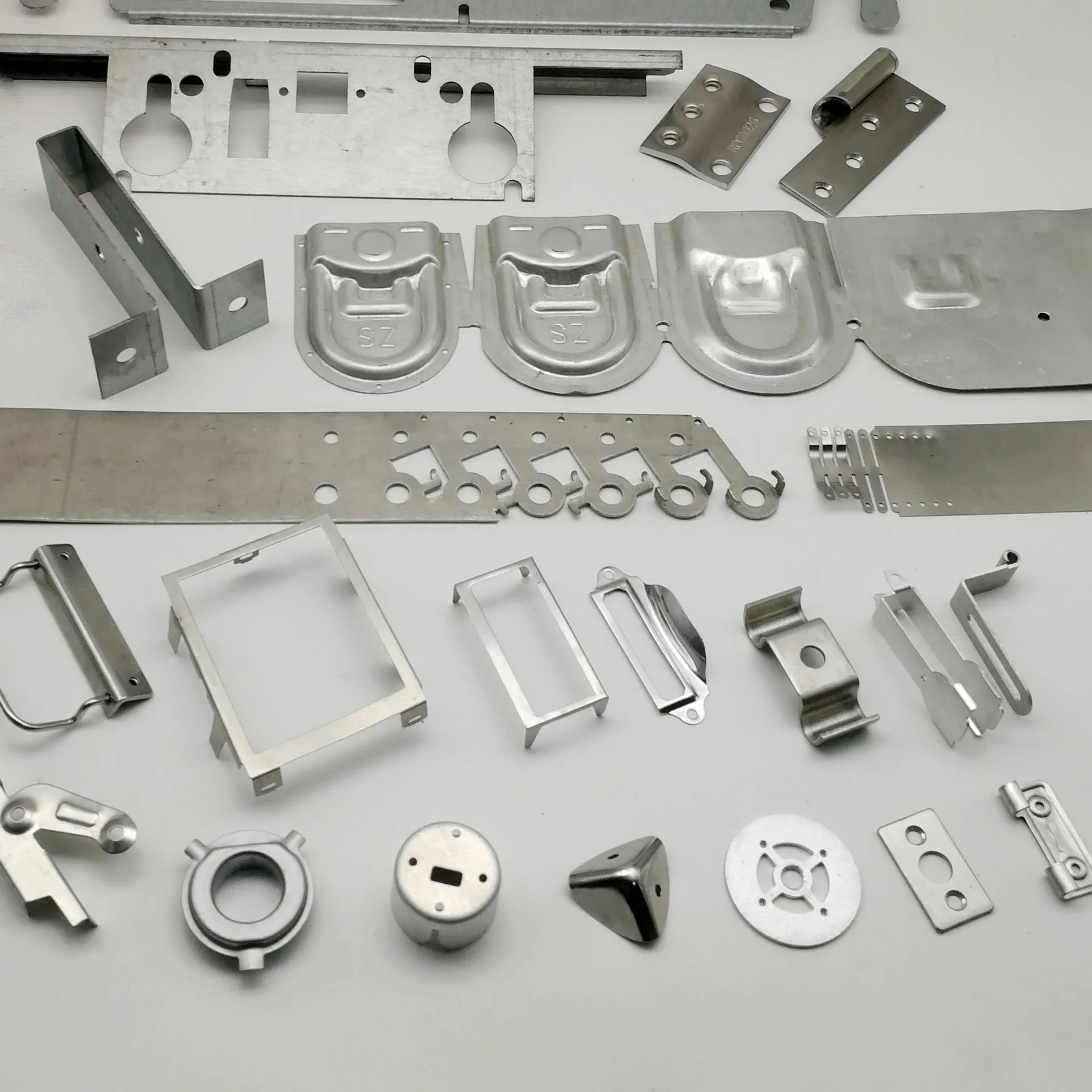
High-Pressure Die Casting (HPDC) is one of the most widely used methods due to its ability to produce high volumes of parts with exceptional dimensional accuracy and smooth surface finishes. In this process, molten metal is injected at high speed and pressure into a steel mold. This method is ideal for manufacturing lightweight automotive parts, complex industrial components, and intricate electronic housings. Both hot chamber and cold chamber machines cater to different material requirements; hot chamber techniques are suited for low melting point metals like zinc, whereas cold chamber processes accommodate aluminum and magnesium.
Low-Pressure Die Casting (LPDC) offers an alternative approach that emphasizes the consistent quality of casting and material strength. LPDC involves filling the die with metal from a holding furnace by applying low pressure, usually between 0.7 to 1.
5 bars. This technique is less stressful on the equipment and allows for the manufacturing of larger parts with fewer defects, making it perfect for producing automotive wheels and other symmetrical components. Its superior control over the filling process helps minimize turbulence and gas entrapment, enhancing the mechanical properties and integrity of the casted parts.
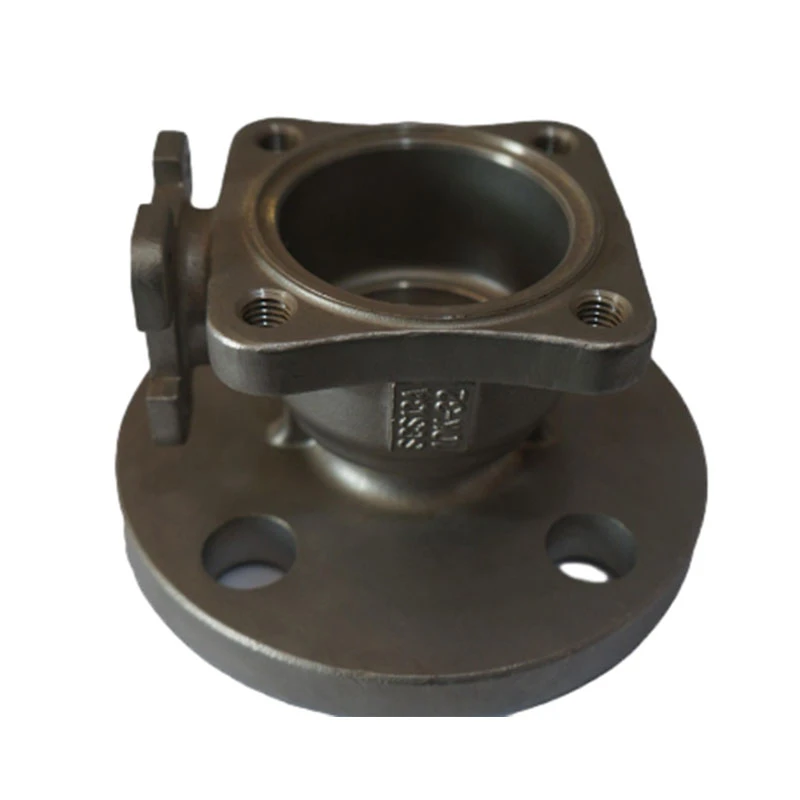
Vacuum Die Casting represents a high-end subset of die casting that incorporates vacuum to eliminate air and gases from the mold cavity. This approach reduces porosity and significantly boosts product density and quality, critical for applications demanding high structural integrity, such as aerospace and military components. By reducing defects and the need for post-processing, vacuum die casting not only delivers superior physical attributes but also offers cost-effectiveness for complex and demanding designs.
Squeeze Die Casting merges the quick cycle times of die casting with the porosity-free and high-strength characteristics of forging. During this process, molten metal is carefully pressed into a preheated die, where it solidifies under high pressure. The resultant components exhibit improved density and mechanical properties suitable for high-stress applications like engine components and high-performance machinery parts. This method effectively reduces machining operations and post-processing requirements, offering an efficient solution for producing robust parts with minimal waste.
die casting types
Semi-Solid Die Casting, also known as thixocasting, involves the injection of partially solidified metal into a die, leveraging the advantages of both liquid and solid metal processing. This allows precise control over the metal's flow and cooling rates, resulting in components with superior dimensional stability and reduced porosity. Ideal for producing components with intricate external geometries and thin walls, semi-solid die casting finds applications in consumer electronics, automotive, and medical devices, where lightweight yet resilient parts are paramount.
Each die casting method addressed offers unique advantages, and choosing the appropriate type hinges on several factors including the intended application's complexity, desired material properties, production volume, and cost constraints. Utilizing advanced technological integrations and process optimizations can further enhance the capabilities and applications of these casting techniques.
Continual advancements in material science and engineering bolster die casting as a transformative process, with innovations in alloy compositions and coating technologies promising future enhancements. As industries pivot towards sustainability, eco-friendly die casting practices, such as using recyclable materials and adopting energy-efficient technologies, are becoming integral. Understanding and harnessing the potential of these die casting types can significantly impact the development of lighter, stronger, and more cost-effective products across diverse sectors.
For manufacturers and engineers, mastering the intricacies of each die casting process fosters informed decision-making, tapping into sophisticated design potentials while ensuring quality and reliability. Through insightful exploration and application of these methods, industries can maintain a competitive edge in an ever-evolving market landscape.