Calculating die casting tonnage is an integral part of manufacturing precision, efficiency, and sustainable production. This complex process, which requires a blend of mathematical acumen and industry expertise, directly impacts the quality and cost-effectiveness of the final product. Throughout the years, experts have refined tonnage calculation methodologies, ensuring that manufacturers can maintain high-quality outputs while minimizing material waste and production costs.
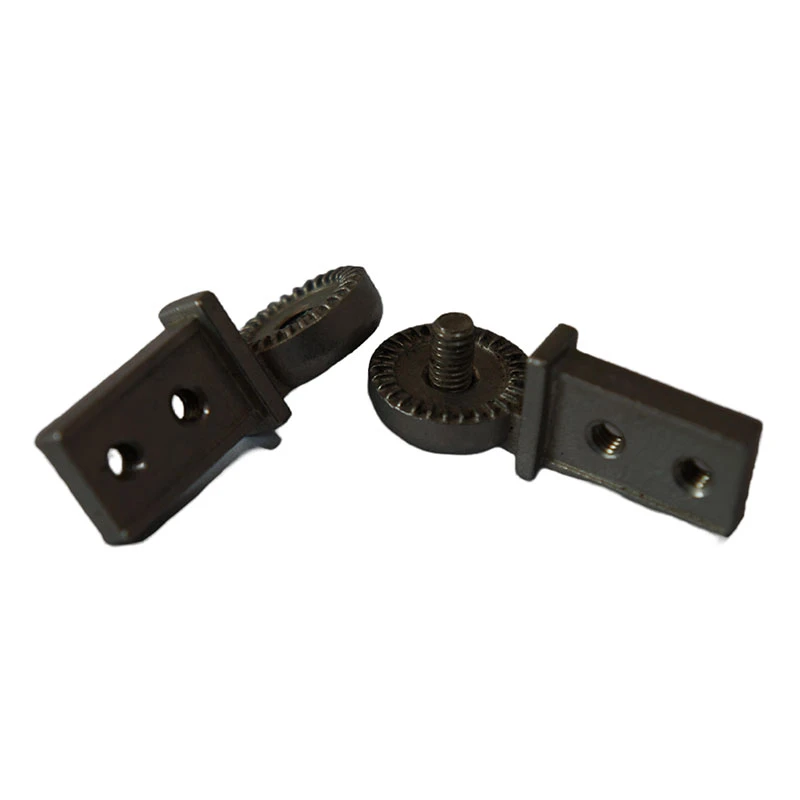
In die casting, tonnage refers to the amount of clamping force needed to keep the die halves closed during the injection of molten metal. This force is crucial in preventing metal from escaping the mold, which can result in defects and compromised structural integrity. The determination of die casting tonnage involves a series of calculations, starting with the understanding of the projected area of the mold and the pressure applied during the casting process. Typically, experienced engineers employ the formula Tonnage = Projected Area x Metal Pressure x Safety Factor.
The projected area, measured in square inches or millimeters, is the surface area of the part that will face the cavity pressure. An accurate measurement is paramount; any miscalculations can lead to insufficient clamping force, resulting in product defects or equipment malfunctions. To measure this, professionals usually rely on advanced CAD software that provides precise dimensions and eliminates human error.

Next is the metal pressure, the amount of pressure exerted by the molten metal during the injection phase, typically measured in psi (pounds per square inch) or MPa (megapascals). This variable is contingent upon the type of metal being used, with different materials requiring different levels of pressure. For instance, aluminum and magnesium, popular in die casting, generally demand moderate pressure levels due to their lower densities compared to metals like steel.
die casting tonnage calculation
Incorporating a safety factor is also crucial for ensuring that additional forces, such as those from rapid metal injection or thermal expansion, don't compromise the mold's integrity. Although industry standards may vary, a safety factor of 1.5 to 2x is commonly adopted to provide a buffer against unforeseen variables. The safety factor accounts not just for equipment limitations, but also for potential fluctuations in pressure and temperature during production.
Seasoned professionals recognize that optimal die-casting tonnage is more than just a calculation; it is a balancing act that involves cost, quality, and machine capability. While higher tonnage can eliminate defect risks, it may also elevate production costs and stress on machinery. Conversely, lower tonnage can conserve resources and reduce wear, but runs the risk of creating faulty products. As such, finding the right tonnage is a pivotal task requiring both experience and technical know-how.
Technological advancement has further streamlined this process, with the advent of sophisticated tonnage calculators and simulation software. These tools allow manufacturers to visualize and test different variables, refining the process and enhancing prediction accuracy. Many companies have integrated these technologies into their workflows, ensuring that each casting operation is fine-tuned to achieve the highest precision and efficiency possible.
To conclude, understanding and calculating die casting tonnage is an intricate art that combines scientific principles with industry expertise. It is a testament to the advances in manufacturing that such meticulous processes can occur smoothly and on a grand scale. Professionals in the industry need to not only engage with the mathematics of tonnage but also leverage innovative technologies and a deep understanding of material properties to improve product quality and efficiency continuously. As manufacturing continues to evolve, so too will approaches to die casting tonnage calculation, offering exciting possibilities for the future of this pivotal production method.