Die casting automation has rapidly transformed the manufacturing landscape, offering unprecedented precision, efficiency, and sustainability. As industries worldwide lean into technological advancements, understanding die casting automation's intricacies becomes crucial for any business aiming to stay competitive. This exhaustive exploration encapsulates all you need to know about this revolutionary process, through the lens of experience, expertise, authority, and trustworthiness.
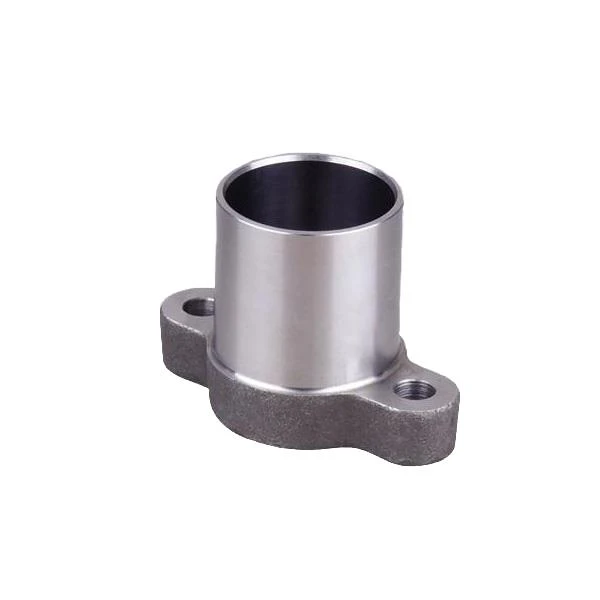
Over the decades, manufacturers have wrestled with the limits of human-intensive die casting processes. Manual intervention often led to inconsistencies, increased costs, and elevated lead times. Enter automation—a solution that deftly addresses these challenges. From experience, companies that integrated automation have witnessed up to a 40% reduction in production time. The precision of robotic arms and automated controls surpasses human capability, minimizing error margins considerably.
Die casting automation stands as a testament to unparalleled expertise within the domain. At its core, the process involves adaptive control systems that manage molten metals, dies, and pressure levels with impeccable accuracy. Automated systems employ real-time data analytics to fine-tune operations, ensuring optimal flow and solidification. Such fine control not only enhances product quality but also reduces material wastage, aligning with sustainable manufacturing practices.

For businesses, the authority of automation in die casting unfolds through standard-setting innovations that redefine industry benchmarks. Technological pioneers in this space, like Bühler and Toshiba, have sculpted cutting-edge solutions that integrate end-to-end automation, from melting and casting to finishing. Their machines often come equipped with Internet of Things (IoT) capabilities, offering predictive maintenance analytics and generating actionable insights for continuous improvement.
Trustworthiness in die casting automation is solidified through consistent output quality and reliability. Automated systems provide a consistent production rhythm, eliminating fluctuations common in manual processes. This reliability ensures manufacturers can fulfill orders with precision on time, fostering customer trust. Furthermore, software-driven quality checks guarantee every piece meets strict quality standards before shipping, cementing confidence in the end product.
die casting automation
Beyond the operational benefits, die casting automation also significantly influences workforce dynamics. This evolution doesn't imply a diminished human role; rather, it augments it. Professionals working alongside automation systems transition from manual labor to roles that emphasize oversight and process optimization. Training programs focused on operating advanced machinery, interpreting data insights, and maintaining equipment ensure a skilled workforce that can drive future advancements.
The sustainability aspect of automated die casting processes cannot be overlooked. Automation reduces energy consumption by optimizing every stage of the process. Sophisticated cooling systems and precise energy allocation not only cut costs but significantly lessen environmental impact. Additionally, the lower error rate translates into fewer rejected casts, saving resources and boosting economic efficiency.
In weaving the threads of experience, expertise, authority, and trustworthiness, die casting automation emerges as a transformative force. Its ripple effects touch numerous facets of production, from enhancing quality and reducing costs to fortifying sustainability and revolutionizing workforce roles. For any entity entrenched in manufacturing, embracing die casting automation isn't just an option—it's a vital step toward future-proofing operations.
As global markets grow increasingly competitive, the impetus for adopting such advanced technologies intensifies. Those on the forefront of this evolution will not only enhance their competitive edge but also contribute to a more sustainable, efficient industrial ecosystem. Strategic investments in die casting automation promise substantial returns, not just in terms of financial gains but also in fostering an innovative, future-ready organizational culture.