Custom die casting has emerged as a pivotal process in the manufacturing industry, known for its precision, efficiency, and ability to create complex metal parts. This specialized manufacturing method involves the injection of molten metal into a mold cavity, which is then cooled and solidified into the desired shape. Its significance spans across multiple sectors, including automotive, aerospace, electronics, and consumer goods. In this article, we'll delve into the nuances of custom die casting, drawing from extensive experience and authoritative knowledge to explore its benefits and challenges, while also highlighting its professional applications and implications for product development.
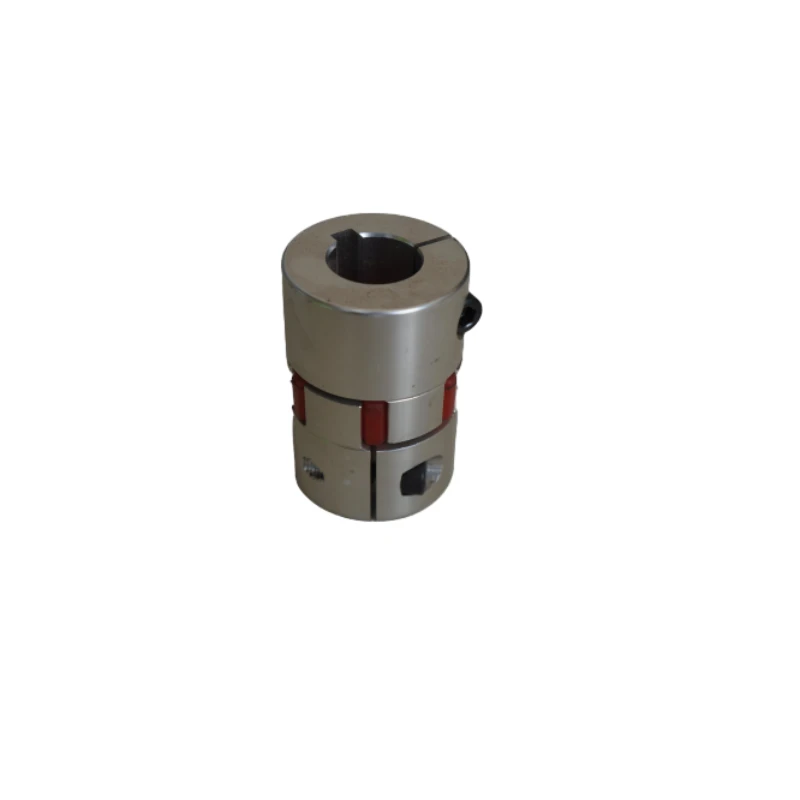
Custom die casting stands out due to its ability to produce high-quality components with intricate detail and tight tolerances. The process avoids the necessity for extensive machining, which not only minimizes waste but also significantly reduces production costs. From an expert's viewpoint, the hallmark of custom die casting lies in its scalability; it allows for the production of both large and small volumes, catering to a wide variety of industrial needs. Developed with precision engineering, custom die casting ensures products that are robust, reliable, and meet strict industry standards.
The expertise required in custom die casting is multifaceted, extending beyond the basic operation of machinery. It includes mastering the properties of various metals, such as aluminum, zinc, and magnesium, each chosen based on the specific demands of the application. Professionals in the field must understand the thermal and mechanical properties of these metals and how they interact with different mold materials and designs. Moreover, they must be conversant with advanced technological tools like computer-aided design (CAD) software, which is imperative for designing molds with exceptional precision. This technical prowess ensures that every aspect of the die casting process, from conception to production, aligns with the client's specifications and quality standards.
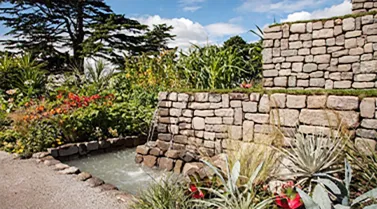
Authoritativeness in the die casting industry is often demonstrated through adherence to strict regulatory and environmental standards. Companies well-versed in custom die casting prioritize sustainable practices, such as recycling excess material and reducing energy consumption. Furthermore, they maintain certifications from recognized bodies, which serves as a testament to their commitment to quality and efficiency. By consistently meeting and exceeding these standards, manufacturers not only underscore their reputation but also build long-standing trust with customers and partners.
custom die casting
The reliability inherent in custom die casting contributes significantly to its trustworthiness. Each piece produced through this method is subjected to rigorous testing processes to verify its structural integrity and functionality. Proven methodologies, including finite element analysis (FEA), are employed to detect potential defects and enhance product performance. This thorough testing regime ensures that end products, whether used in safety-critical applications like automotive components or intricate parts for electronic devices, are of the highest caliber.
Tailoring the die casting process to meet specific customer needs is crucial for achieving optimal results. Customization involves selecting the right alloy and refining the mold design to suit the intended application. The expertise and creativity of seasoned engineers are invaluable in this phase, as they can predict and mitigate potential challenges, ensuring a seamless manufacturing process. Through close collaboration with clients, these professionals can offer invaluable insights and advice, transforming initial ideas into tangible, high-precision components.
For businesses considering custom die casting as a solution, it is imperative to partner with a manufacturer that exemplifies the principles of experience, expertise, and trustworthiness. By doing so, they can benefit from streamlined production processes, reduced lead times, and superior quality components that align with their business objectives. Embracing this advanced manufacturing technology can lead to innovative product designs, offering a significant competitive advantage in the marketplace.
In summary, custom die casting is a sophisticated manufacturing process that requires deep technical knowledge, a commitment to quality, and a proactive approach to environmental stewardship. As industries continue to evolve, the demand for precision-engineered components grows, and custom die casting positions itself as a critical player in meeting these emerging needs. Its blend of efficiency, versatility, and reliability makes it an indispensable tool for manufacturers focused on delivering high-performance, customized products that fulfill the stringent demands of industrial innovation.