Casting sand for metal plays a crucial role in the metal casting industry, a practice that dates back thousands of years. This method of metal casting remains prevalent due to its cost-effectiveness and capability to produce complex shapes and components. Delving into the intricacies of casting sand unveils a myriad of details that underscore its significance, optimal usage, and evolving technology.
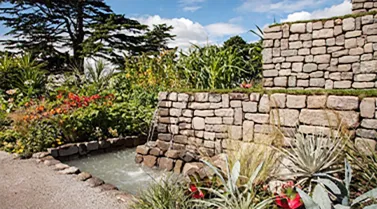
Casting sand primarily consists of finely ground, small grains of silica, alumina, or zircon, selected for their heat-resistant properties. The essential characteristic of these sands is their ability to withstand the high temperatures of molten metal while providing a fine surface finish. The grains are often mixed with clay or chemically bonded materials to enhance moldability and durability. The binding elements play a pivotal role as they determine the sand's compressibility, permeability, and ultimately, its suitability for different metal casting projects.
Green sand is one of the most commonly used casting sands in the industry. It comprises silica sand, clay, and water, making it beneficial for producing steel, iron, and non-ferrous alloys. Its name derives from the moisture content present when it's used to form a mold. The clay and water mixture grants green sand its bond strength, allowing it to hold the mold shape even under significant stress. Green sand molds are renowned for their flexibility and reusability, cutting down material waste and lowering costs for manufacturers.
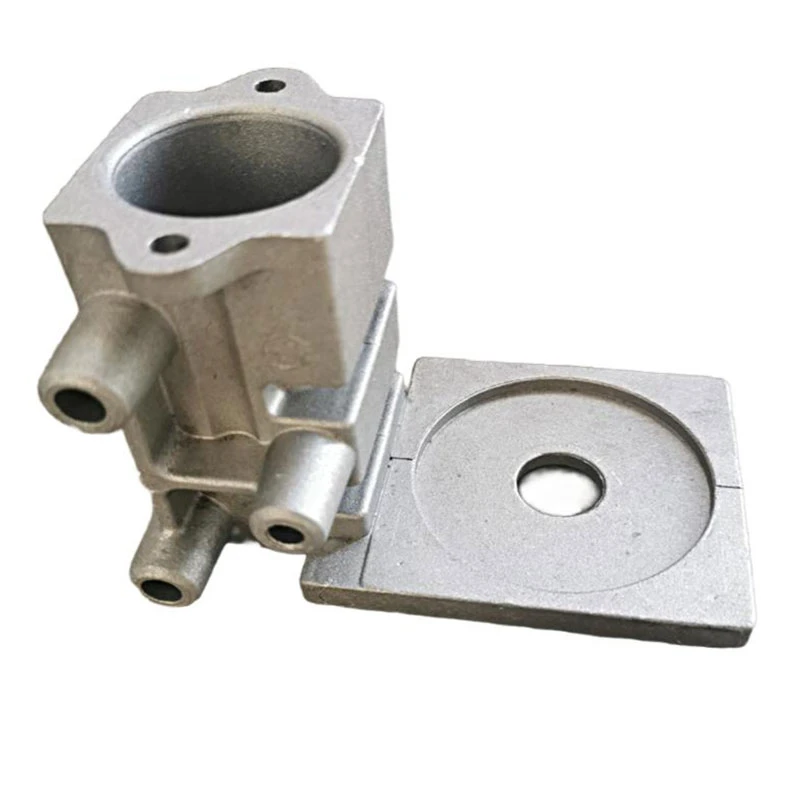
Another variation is the chemically bonded sand, where resins such as phenolic, furan, or alkaline phenolic binders replace traditional bonding agents like clay. These sands exhibit superior strength and permeability, fostering precision in detailed castings and reducing defects. Industries that demand high fidelity in casting, especially aerospace or automotive sectors, often prefer chemically bonded sands due to their reliability in producing consistent and precise components.
In recent years, the introduction of 3D printing in the creation of sand molds and cores has revolutionized metal casting, allowing for unprecedented complexity and customization. This technology uses CAD software to design molds, significantly speeding up the prototype phase and enabling the production of intricate shapes that would be impossible using traditional methods. 3D printing also facilitates the use of less sand, reducing material costs and enhancing environmental sustainability.
casting sand for metal
However, successful metal casting with sand necessitates a deep understanding of the metallurgical properties involved. It’s crucial to consider the expansion characteristics of the sand to avoid casting defects like veining or scabbing. Techniques such as pre-compaction of sand and proper control of sand-to-metal ratios are vital for preventing defects and ensuring the integrity of the final product.
The environmental implications of casting sand cannot be overlooked either. Continuous advancements in recycling and sand reclamation techniques play a significant role in minimizing the environmental footprint of foundries. Innovations such as thermal reclamation help clean and reuse casting sand, greatly reducing the need for new raw materials and preserving natural resources.
For companies aiming to optimize their search engine presence, understanding the multifaceted aspects of casting sand not only aligns with effective SEO strategies but also illustrates their commitment to sustainability and technological advancement. Today's informed consumers and B2B partners prioritize environmental responsibility, making it an indispensable aspect of business models in the metallurgy sector.
In conclusion, casting sand for metal remains a testament to the union of tradition and modernity within the metal casting realm. Its evolution reflects ongoing advancements that meet the demands of industry trends and consumer expectations. Harnessing these insights can dramatically elevate a company's standing as a leader in both technology and environmental stewardship.