Understanding aluminum die casting wall thickness is crucial for manufacturers and engineers aiming to produce efficient and high-quality components. Aluminum die casting has become increasingly popular due to its lightweight nature and ability to form intricate shapes with precision. However, wall thickness plays a pivotal role in influencing the quality, cost, and performance of the final product.
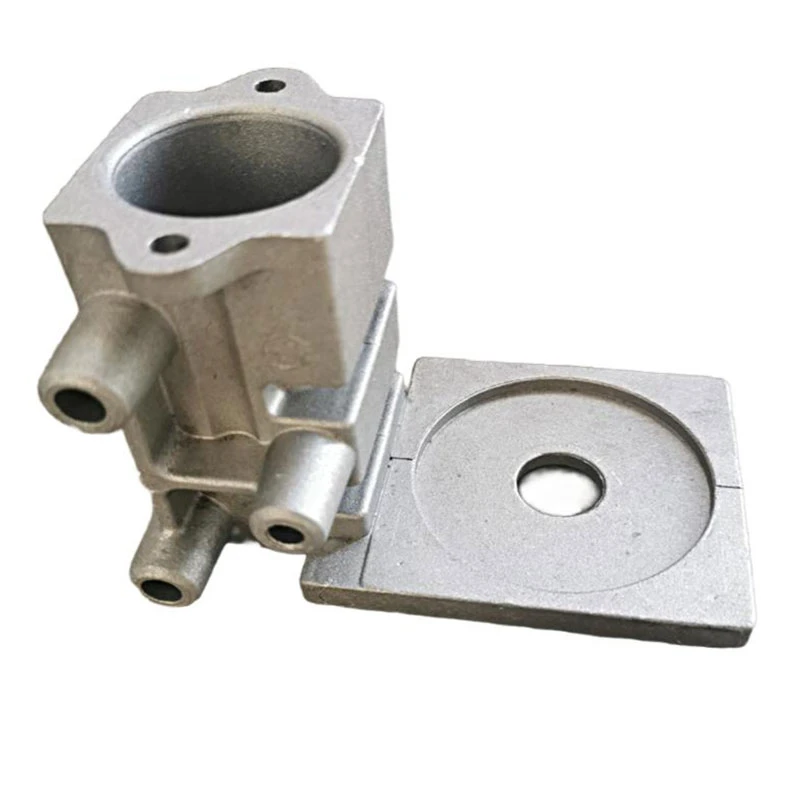
The optimal wall thickness in aluminum die casting depends largely on the design requirements and end-use applications. A critical consideration is achieving a balance between strength and weight. Thinner walls can reduce material consumption and finishing costs, while thicker walls can often offer better structural integrity. Hence, understanding the appropriate thickness is vital for achieving long-term sustainability and performance.
From a manufacturing perspective, there are several factors that impact the choice of wall thickness in aluminum die casting. One primary element is the type of aluminum alloy used. Different alloys exhibit varying mechanical properties, thermal conductivity, and resistance to casting defects which can influence the minimum and maximum feasible wall thickness. Engineers typically select aluminum alloys based on attributes like strength, ductility, and corrosion resistance to meet the desired specifications of different industries from automotive to electronics.
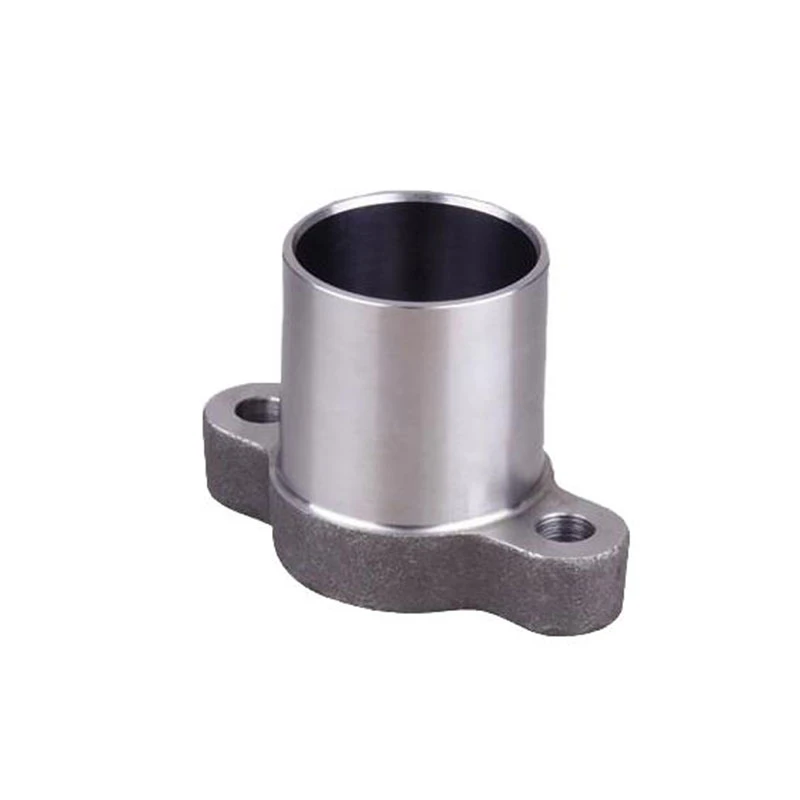
Another crucial consideration is the complexity of the cast design. Components with intricate geometries or those requiring tight tolerances may necessitate varying wall thicknesses to ensure uniform cooling rates and minimize the risk of defects such as porosity or cold shuts. Utilizing computer-aided design (CAD) software, manufacturers can simulate casting processes to predict and optimize wall thickness distribution across complex components, ultimately improving both quality and performance.
Die casting machines and tools employed in the production process also directly influence wall thickness. These tools must be capable of handling fine and precise casting to maintain consistency across production runs. For example, high-pressure die casting machines are preferred for their ability to produce intricate designs with thinner walls, offering more control and reducing the probability of defects.
aluminum die casting wall thickness
One of the often overlooked yet significant factors influencing aluminum die casting wall thickness is the cooling time. Thicker sections typically require longer cooling periods to solidify completely, which can extend cycle times and increase production costs. Efficient cooling techniques, such as water-cooled molds, can help in stabilizing the temperatures, thereby reducing cycle times and ensuring uniform wall thickness.
Manufacturers must also consider post-processing operations like machining and surface finishing, which may alter the initial wall thickness. Machining allowances need to be incorporated into the design to compensate for material removal during subsequent processing. Surface finishes may add layers or coatings that change dimensions subtly but significantly enough to affect component fitment and performance.
Compared to traditional casting methods, aluminum die casting offers a unique combination of precision and efficiency. However, achieving the correct wall thickness remains a technical challenge that requires a nuanced understanding of materials engineering and process control. By evaluating the interplay between alloy selection, cooling strategies, and machining processes, industry professionals can enhance the robustness, reliability, and longevity of aluminum die cast parts.
Practically, partnering with an experienced die casting supplier can significantly benefit industries seeking precision-engineered components. These specialists bring a blend of expertise in material science, tooling technology, and process optimization. They employ advanced techniques and methodologies to forecast performance and sustainability, aligning with the ever-evolving demands of modern engineering applications.
In conclusion, the significance of wall thickness in aluminum die casting frames itself as more than a measure of material usage—it is a determinant of quality assurance, economic efficiency, and product efficacy. As the industry continues to evolve, embracing technological advances and scientific insights promises enhanced outcomes across various manufacturing sectors.