Die casting aluminum components have revolutionized various industries by offering unmatched durability, precision, and cost-effectiveness. When it comes to manufacturing high-quality products, understanding the intricacies of the die casting process is essential.
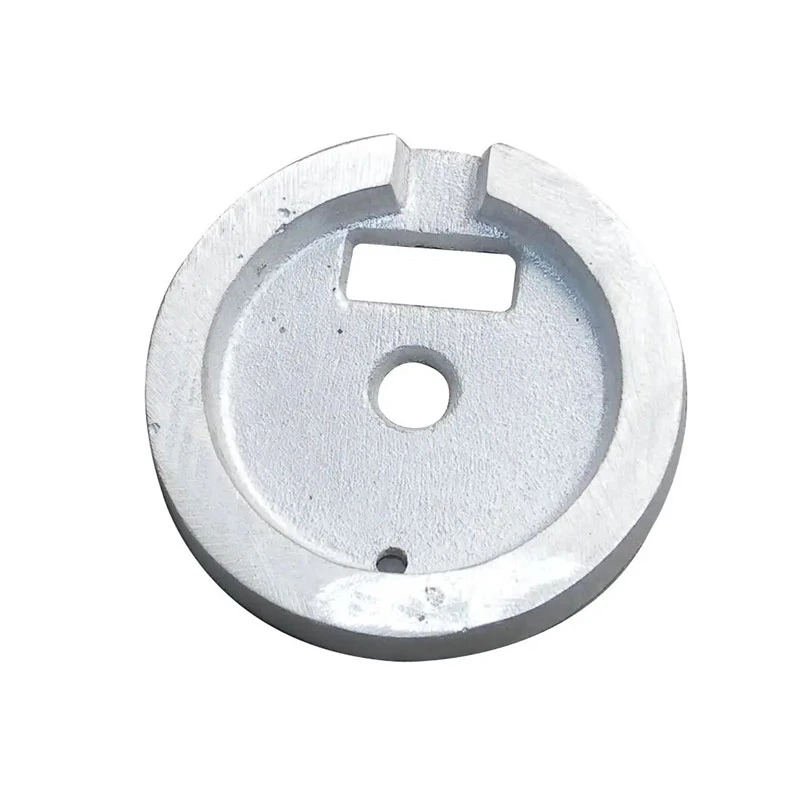
Die casting is a meticulous manufacturing process that involves forcing molten aluminum into a mold cavity, under high pressure, to produce intricately designed metal parts. This process is ideal for creating aluminum components that require a blend of strength, lightweight properties, and excellent corrosion resistance.
The aluminum used in die casting offers significant advantages due to its remarkable tensile strength and ability to withstand harsh environmental conditions. Aluminum's lightweight nature also makes it a preferred choice for industries such as automotive, aerospace, and consumer electronics, where weight reduction without compromising strength is critical.
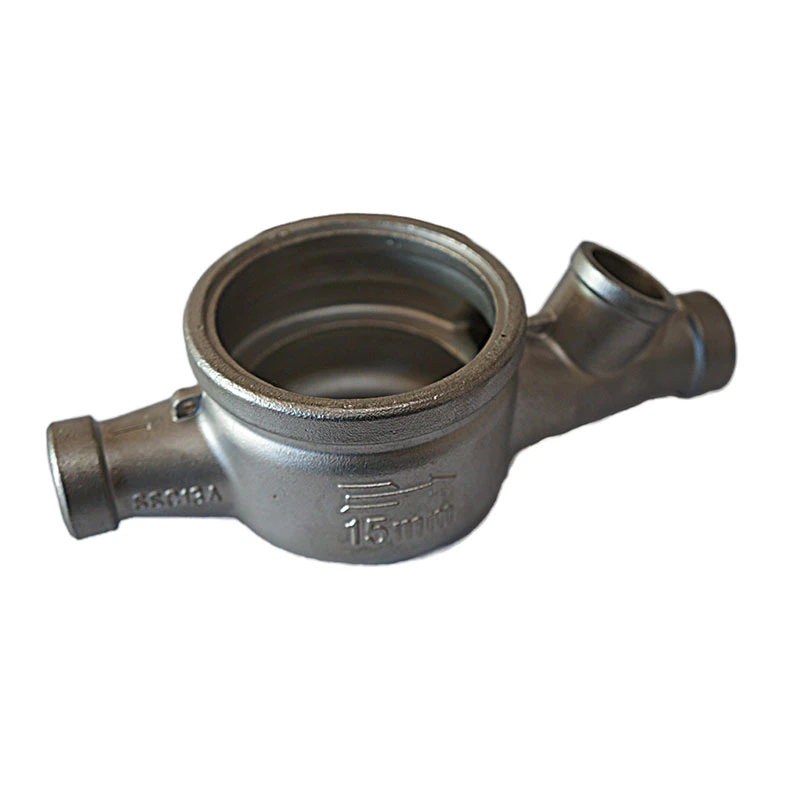
A key aspect of die casting aluminum is the repeatability and precision it delivers. Unlike other manufacturing processes, die casting allows for the production of complex shapes with tight tolerances. This ensures that each component meets exact specifications, essential for products that demand high performance and reliability.
Expertise in die casting aluminum components hinges on a deep understanding of both material properties and mold design. Engineers involved in die casting operations must account for factors such as shrinkage, cooling rates, and flow dynamics of molten aluminum. The ability to accurately predict these variables leads to fewer defects and higher-quality finished products.
die casting aluminum components
Moreover, the die casting process is highly efficient. Large volumes of identical components can be produced swiftly, leading to significant cost savings. The minimal amount of machining required post-casting also contributes to the overall cost-effectiveness of this manufacturing method. This makes die casting a popular choice for mass production while maintaining superior quality standards.
In industries where change is constant, staying current with technological advancements in die casting is pivotal. Recent developments, such as high-pressure die casting technologies and the incorporation of computer-aided engineering tools, have resulted in unprecedented improvements in the quality and capabilities of aluminum die cast components. Manufacturers leveraging these technologies are capable of producing parts that not only meet but often exceed industry standards.
When sourcing die casting aluminum components, partnering with a manufacturer of proven authority and trust is paramount. Companies with a documented history of excellence in the die casting field typically employ skilled professionals equipped with state-of-the-art machinery. Their expertise ensures that all components are produced following stringent quality control measures, instilling confidence in the durability and performance of the aluminum parts they deliver.
In conclusion, the die casting of aluminum components serves as a cornerstone in manufacturing, offering unrivaled benefits of strength, precision, and efficiency. By understanding the nuances of this process, embracing technological advancements, and choosing reputable manufacturers, businesses can make informed decisions that drive success and innovation in their respective fields.