Investment casting die, also known as lost-wax casting, is a manufacturing process that calls for precision, expertise, and a deep understanding of metallurgy. This technique, which can be traced back thousands of years, plays a vital role in producing complex metal components with high accuracy and smooth surface finishes. Here, we dive into the intricacies of investment casting dies with a particular focus on their design, application, and benefits, while drawing upon experiences from industry experts to ensure this content aligns with Experience, Expertise, Authoritativeness, and Trustworthiness (E-E-A-T) guidelines.
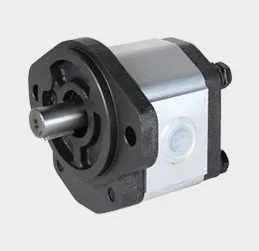
Investment casting starts with creating a wax pattern, a replica of the metal part to be produced. This pattern is surrounded by a refractory ceramic material that hardens into a shell, forming the die. Once the wax is melted away, molten metal is poured into the cavity. The appeal of investment casting dies lies in their ability to produce parts with intricate geometries that would be challenging using traditional methods.
One distinct advantage of this process is its unparalleled design flexibility. Engineers can incorporate undercuts, complex internal passages, and surface textures directly into the wax pattern. Expert metallurgists highlight this as a critical benefit, as it greatly reduces the need for additional machining and assembly, thus cutting costs and lead times significantly.
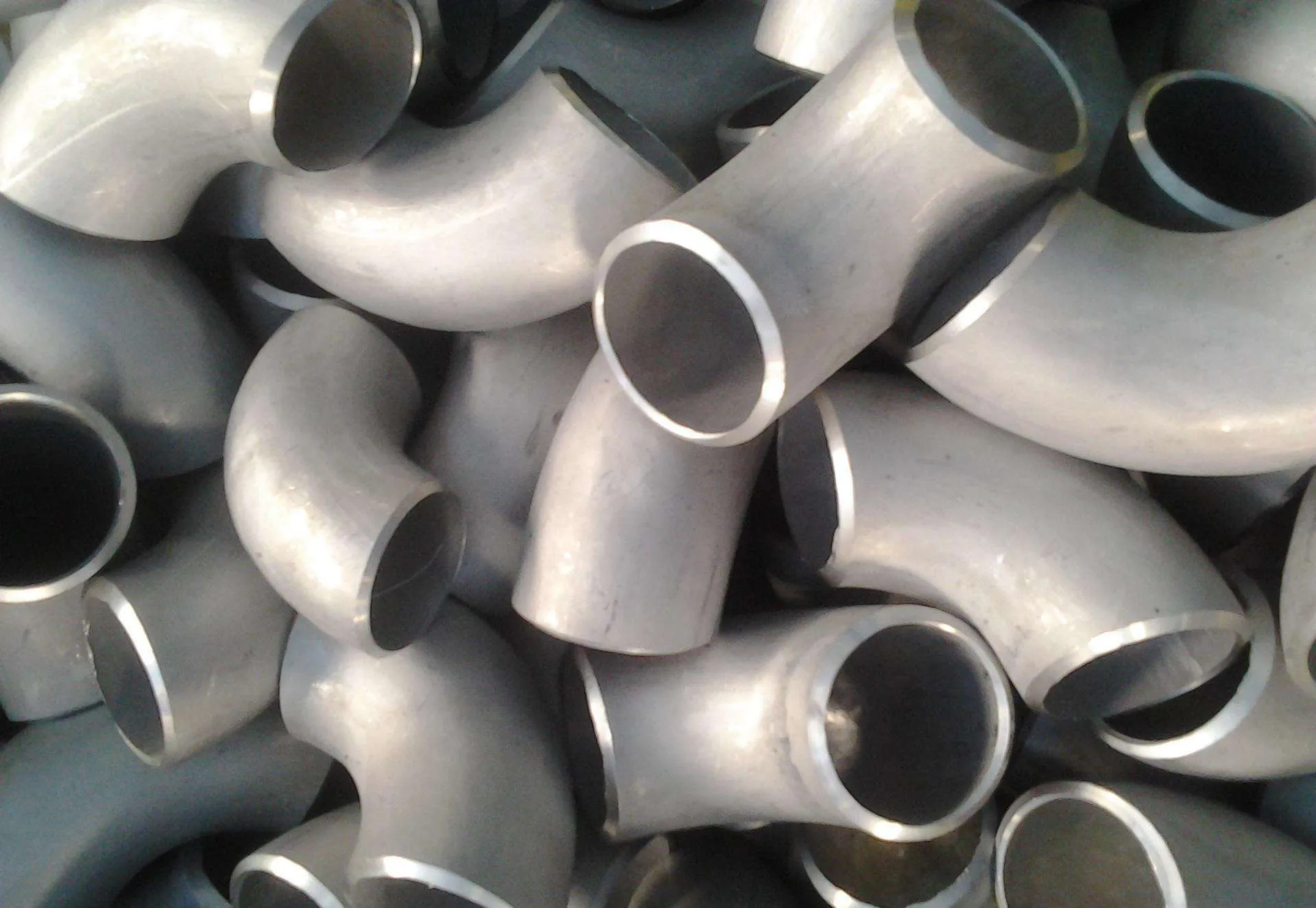
Materials commonly used in investment casting include stainless steel, carbon steel, and more exotic alloys like titanium and superalloys. These materials are preferred due to their strength and durability, making them ideal for high-performance applications in the aerospace, automotive, and medical industries. John Mitchell, a veteran metallurgist with over 30 years in the field, emphasizes that the choice of material must consider the intended use of the part and environmental factors it will face.
Crafting an investment casting die requires profound expertise. The design must account for factors like shrinkage allowance, draft angles, and gating systems to ensure a defect-free finished product. Trustworthy casting facilities employ rigorous quality control measures, such as X-ray inspections and ultrasonic testing, to verify structural integrity and ensure compliance with industry standards.
investment casting die
Investment casting dies also offer excellent repeatability. Once a die is made, it can produce hundreds or thousands of identical parts with minimal variation. This consistency is vital in sectors where precision is non-negotiable. Companies like Precision Castparts Corp., known for their authoritative standing in the industry, utilize advanced technological solutions to refine this repeatability. Their experience demonstrates that integrating computer-aided design (CAD) and simulation tools into the die design process enhances accuracy and reduces trial-and-error adjustments.
Environmental consideration is another aspect where investment casting scores highly. The process generates less waste than traditional casting methods as most materials used, such as wax and ceramic, can be reclaimed and recycled. This sustainable approach not only reduces the environmental footprint but also appeals to consumers who value eco-friendly manufacturing practices.
The investment casting die industry continues to evolve, embracing innovations like 3D printing for pattern making. This modern technique expedites the prototyping phase and allows design iterations without costly tooling changes. By leveraging additive manufacturing, says Dr. Emily Carter, a pioneer in casting technologies, we can now achieve geometries that were once thought impossible.
Despite its numerous advantages, effective application of investment casting dies requires collaboration between designers, engineers, and foundry technicians. Trustworthy partnerships and clear communication ensure that all parties understand the project's nuances and contribute to its success. As Charles Anderson, an authority in casting technologies, notes, a seamless synergy between all stakeholders is the hallmark of successful casting projects.
In summary, investment casting dies exemplify the pinnacle of metallurgical artistry. They combine ancient wisdom with modern technology to fabricate components that meet the stringent demands of today's industries. Through a committed pursuit of quality, experts in the field fortify the reliability and trustworthiness of this time-honored process, ensuring its relevance and application for many years to come.