Green sand casting has marked its territory as a primary method in the realm of metal casting, offering undeniable benefits and showcasing unshakable reliability. This casting process uses a mixture comprising sand, clay, water, and other additives to create a mold into which molten metal is poured. The term green doesn't relate to color; instead, it signifies that the sand is used in its wet, or green, state.
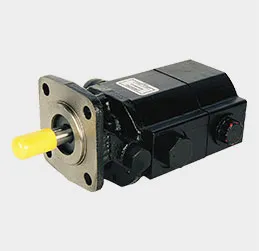
In terms of expertise, the technique is celebrated for its ability to produce castings in intricate shapes, sizes, and weights with considerable precision. The pliability of green sand allows for meticulous mold detailing, ensuring that even the most complex geometries can be effectively achieved without compromising on mold integrity. This adaptability renders green sand casting ideal for a wide range of industries, including automotive, aerospace, and machine parts.
Real-world experiences from seasoned foundry professionals are full of insights into the green sand casting process.
Many emphasize the process’s efficiency and cost-effectiveness. For instance, manufacturers praise it for reducing energy consumption because it operates at lower temperatures compared to other casting methods, contributing to both cost savings and improved sustainability profiles. Furthermore, it supports a sustainable approach by favoring the recycling of sand, minimizing its environmental footprint—a factor which resonates powerfully in an era of increasing ecological concerns.
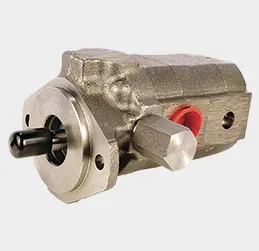
Expert authority in the field highlights green sand casting's versatility. The industry has witnessed significant advancements in the quality and consistency of the castings produced through continuous developments in sand formulation and process automation. Modern foundries leverage advanced technologies and testing methodologies, ensuring the physical properties of both the sand mixtures and resulting castings meet rigorous international standards. Decision-makers and technical directors in manufacturing enterprises often consider green sand casting as the go-to choice for volume production where dimensional accuracy and cost efficiency are critical.
green sand casting
Trustworthiness in green sand casting is built on its long-standing history and proven track record. The technique is one of the oldest known to metalwork, yet remains highly relevant and continually evolves with technological enhancements. Successful case studies and data-driven results from industries that rely heavily on green sand casting contribute significantly to its reputation. Testimonials from engineers and quality assurance experts often highlight the reliability and durability of components produced using this method, reinforcing its credibility in the manufacturing ecosystem.
An essential point of product-based discussions is the material compatibility and range green sand casting offers. It supports a vast array of ferrous and non-ferrous metals, allowing it to cater to diverse industry specifications and performance requirements. Cast iron, steel, aluminum, and copper alloys are commonly used within this process, each bringing distinct benefits in terms of mechanical properties and application potential.
From a practical standpoint, green sand casting provides foundries with flexibility in production scheduling and customization, enabling swift transitions between projects and accommodating custom requirements with minimal downtime. This aspect is particularly beneficial for operations looking to minimize lead times and enhance production throughput, thereby optimizing their supply chain dynamics.
Concisely, the green sand casting process embodies a synthesis of traditional expertise and modern innovation. Its esteemed place in the casting industry is a testament to its reliability, affordability, and supreme adaptability. As technology progresses, green sand casting will likely continue to evolve, retaining its relevance and reinforcing its fundamental role in shaping the future of manufacturing and metalwork.