Sand casting, a well-established manufacturing technique, often evokes questions regarding its capability to produce intricate and detailed parts with high precision. Despite its widespread use, there's a general perception that it may not be suitable for high-precision applications. To clarify these misconceptions, it's essential to delve into the capabilities and potential of sand casting, especially in creating complex shapes with accuracy.
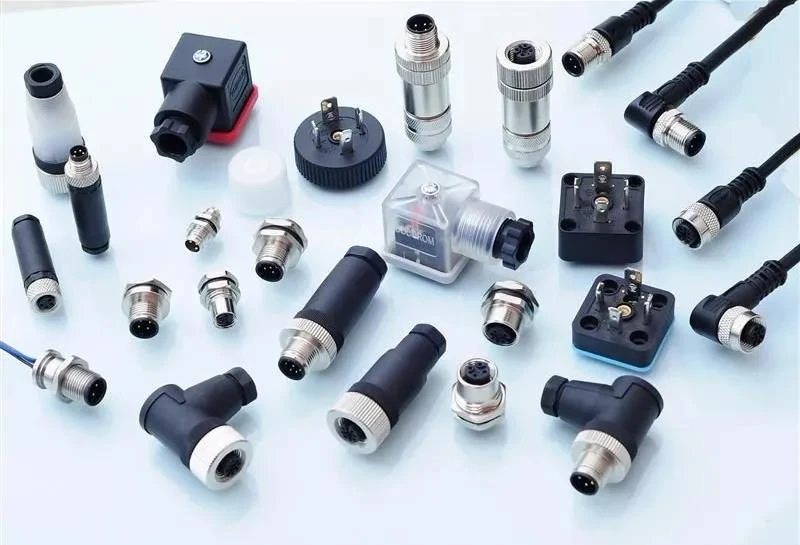
Sand casting has been a staple in manufacturing due to its versatility and cost-effectiveness, making it an attractive option for producing metal parts. It involves creating a mold from sand and pouring molten metal into the mold to produce a cast part. The mold is destroyed in the process, but the ability to use sand for a myriad of shapes is invaluable. The level of detail and precision achievable in sand casting largely depends on several factors, including the quality of the sand, molding techniques, and the experience of the foundry.
One area where sand casting shines is in its adaptability. Skilled foundries can produce complex parts by using finer sand particles, which allow for better surface finish and details. Furthermore, advancements in binder technologies and molding techniques have enhanced the precision achievable in sand casting. With careful control over the compaction of sand and the use of cores to form complex internal geometries, sand casting can create surprisingly intricate shapes that challenge stereotypes regarding its precision limits.
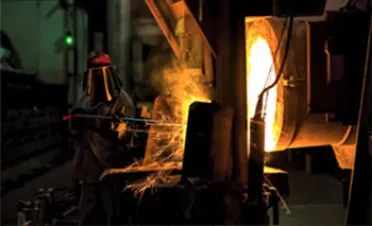
Moreover, the expertise of technicians plays a crucial role in maximizing the output quality in sand casting. Seasoned experts can adjust the sand mixture, binders, and compaction methods to suit the specific requirements of intricate designs. They also use modern tools such as 3D printing to create patterns, enabling the production of complex part geometries with significantly improved accuracy. These factors contribute to the capability of sand casting to achieve precision that can meet the demands of various industries, from automotive to aerospace.
does sand casting produce intricate detailed parts with high precision
When it comes to precision, it's also essential to consider the post-processing steps involved. Though the initial casting may not always meet the highest precision standards, machining and finishing can refine the details to the required specifications. This combination of meticulous casting and careful finishing processes can lead to high-quality parts that serve in critical applications.
Trusted authorities in the industry have recognized the importance of sand casting in producing detailed and accurate parts under certain conditions. For example, ASME (American Society of Mechanical Engineers) reports how implementation of modern quality control and advanced mold-making techniques can significantly improve the precision of sand-cast components. Therefore, sand casting is not just about creating large, rough parts but is equally capable of producing precision components given the right expertise and technologies.
In summation, while sand casting has its limitations, dismissing it as incapable of producing intricate,
detailed parts with high precision would be a misjudgment. The potential demonstrated in modern-day foundries shows that with the right conditions and expertise, sand casting can meet sophisticated requirements. Embracing contemporary techniques and continuous improvement reinforces sand casting's place as a viable choice for producing both simple and complex high-precision parts. Such a comprehensive understanding ensures that sand casting remains a trusted and effective manufacturing method in today's competitive market.