In the world of manufacturing, die casting materials play a crucial role in producing complex and precise metal components. This process, known for its efficiency and precision, relies on the use of specific materials that can withstand the rigors of high-pressure molding and provide long-lasting durability. Understanding the intricacies of die casting materials is essential for maximizing product quality and performance.
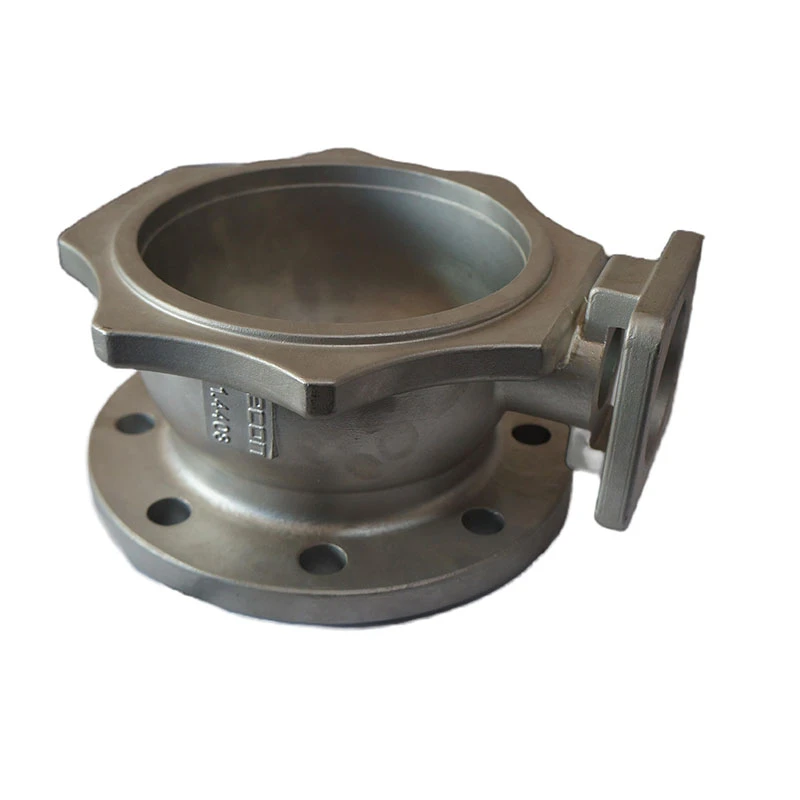
Aluminum, magnesium, and zinc are the predominant die casting materials used in various industries, each offering unique properties that cater to different applications. Aluminum, for instance, is prized for its lightweight nature and exceptional corrosion resistance, making it an ideal choice for automotive and aerospace components. Its ability to withstand high temperatures and conduct electricity efficiently extends its usability across a myriad of sectors, translating into significant cost savings and enhanced product longevity.
Magnesium, on the other hand, is renowned for being one of the lightest structural metals available. Its impressive strength-to-weight ratio makes it a preferred material in the automotive and electronics industries where reducing component weight without sacrificing strength is crucial. By leveraging magnesium’s inherent properties, manufacturers can achieve higher fuel efficiencies and improved product performance, which aligns with the growing demand for sustainable and environmentally-friendly solutions.
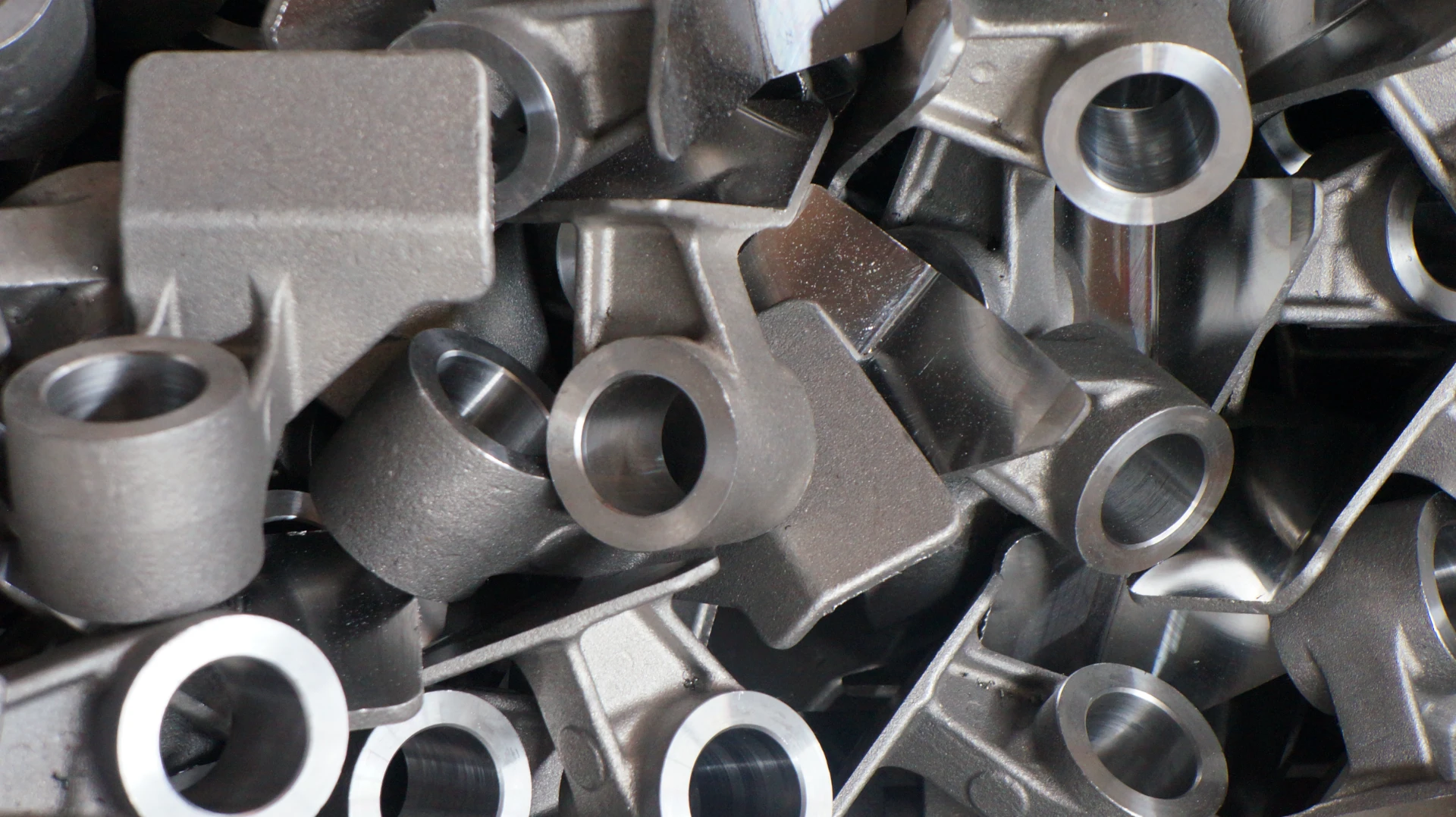
Zinc’s superior malleability and impact resistance make it a popular choice for intricate designs that require high levels of detail and durability. It is commonly used in the production of hardware components, gears, and other small mechanical parts that demand precision and resilience. Its excellent thermal and electrical conductivity further enhances its applicability in the electrical and electronics sectors.
The choice of die casting material significantly impacts the manufacturing process and end product quality. Expert manufacturers must consider factors such as melting point, fluidity, thermal conductivity, and mechanical properties when selecting the material best suited for their specific needs. Furthermore, the material's ability to withstand corrosion and environmental factors over time is critical in ensuring product reliability and reducing maintenance costs.
die casting material
Advanced technologies and innovations in die casting are continuously shaping the future of manufacturing. With a focus on enhancing the properties of traditional materials, researchers are developing new alloys that offer superior characteristics. These innovations aim to push the boundaries of what is possible in die casting, providing manufacturers with more options to refine processes and achieve desired outcomes. Alloy development not only improves performance but also contributes to sustainability efforts by enabling the creation of lighter, more efficient components that require fewer resources to produce.
The expertise of die casting professionals is pivotal in navigating the complexities of material selection and process optimization. Their deep understanding of the interplay between material properties and die casting parameters ensures that the resulting components meet the stringent quality and performance standards expected by modern industries. Through meticulous design and process control, experienced professionals can help mitigate common challenges such as porosity, surface finish defects, and dimensional inaccuracies, ultimately enhancing the reliability of the finished product.
Trustworthiness in die casting extends beyond material choice to encompass the entire production process. Adhering to industry best practices and maintaining rigorous quality control measures instill confidence in clients and end-users. Accreditation from recognized bodies and compliance with international standards further solidify a manufacturer’s reputation as a reliable partner in delivering high-quality die-cast products.
Collaborative partnerships between material scientists, engineers, and manufacturers are driving the evolution of die casting technologies. By sharing knowledge and insights, these stakeholders contribute to the advancement of materials and techniques that redefine industry standards. Continuous research and development efforts are essential in staying ahead of emerging trends and meeting the evolving demands of sectors such as automotive, aerospace, and consumer electronics, where precision, efficiency, and performance are paramount.
In conclusion, the careful selection and application of die casting materials is fundamental to achieving superior product quality and performance. As industries continue to evolve and demand more innovative solutions, the role of experienced professionals in navigating material choices and process optimization becomes increasingly vital. Through sustained research, collaboration, and adherence to best practices, the die casting industry is well-positioned to meet the challenges of the future, offering reliable and sustainable solutions that foster growth and success across multiple sectors.