Die casting is a metal casting process that is characterized by forcing molten metal under high pressure into a mold cavity. The mold cavity is created using two hardened tool steel dies designed to the desired shape and finish. This time-tested process is widely popular for producing complex metal parts with high precision and repeatability, making die-casting dies an essential component in numerous industries.
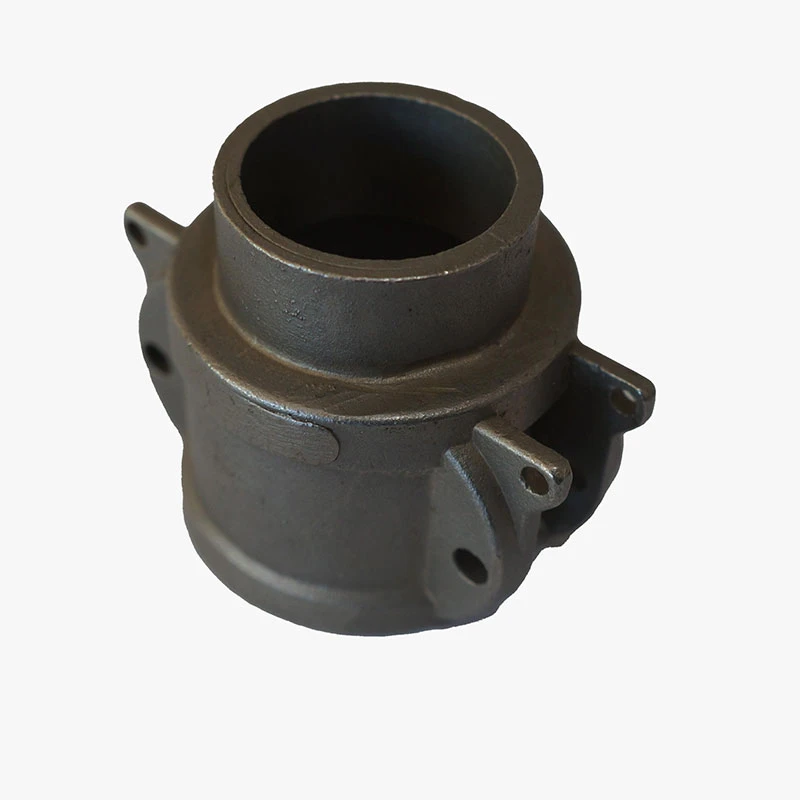
Die casting dies are intricate tools made from high-quality steel grades and demand meticulous design and manufacturing processes. They play a pivotal role in defining the quality, cost, and performance of the final product. The intricacy involved in creating die casting dies is profound as they are highly tailored to meet specific design and application needs.
When assessing the experience of manufacturers involved in die casting dies, it's crucial to delve into the subtle nuances of die making. Experienced manufacturers use advanced CAD software for precise die design, often incorporating complex geometries that reduce the weight of the final product without compromising strength. They employ state-of-the-art CNC machinery for die manufacturing, ensuring consistent dimensional accuracy essential for high-quality casting.
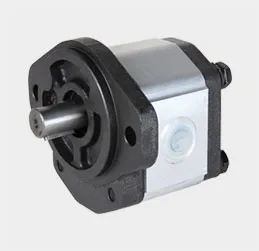
Expertise in die casting dies is reflected in the selection of materials and heat treatment processes. High-grade tool steels such as H13 or SKD61 are often chosen for their ability to withstand extreme thermal cycling and resist wear during the die-casting process. Additionally, these dies are treated with specialized coatings like nitriding or nitrocarburizing to enhance surface hardness and prolong die life, thereby maintaining product integrity across numerous casting cycles.
In terms of authoritativeness, leading experts in the die-casting industry continue to invest in research and development to push the boundaries of what's possible with dies. Innovations such as conformal cooling channels within the dies help reduce cycle times and improve the mechanical properties of cast components by offering more efficient cooling. These technological advancements are championed by industry leaders and backed by robust substantiation from successful implementations in various high-stakes industries such as automotive, aerospace, and consumer electronics.
die casting dies
Trustworthiness in the realm of die casting dies hinges on the rigorous testing and validation of the dies before they are put into full production. Leading manufacturers conduct comprehensive trial runs to ensure that the dies create parts that meet stringent quality and reliability standards. This trust is further reinforced through certification by recognized industry bodies, which adhere to international quality norms.
Moreover, a strong manufacturing partnership is critical when dealing with die-casting dies. Trustworthy manufacturers offer robust after-sales support, including die maintenance, repairs, and modifications if necessary. This long-term support is indicative of a manufacturer’s commitment to not only delivering high-quality products but also ensuring sustained performance over time.
Die casting dies significantly influence production efficiency, material usage, and the precision of the final products. Effective design and manufacturing of these dies can lead to substantial cost savings in mass production, as the repeatability of die casting allows for high volumes with minimal material wastage. Additionally, as sustainability becomes increasingly crucial, advanced die designs focus on optimizing energy efficiency and minimizing waste, aligning with the growing environmental consciousness in manufacturing.
In conclusion,
the importance of die-casting dies cannot be overstated. Their role as the backbone of metal casting processes demands a thorough understanding of design intricacies, material properties, and cutting-edge manufacturing techniques. The future of die-casting lies in continuous innovation, where experience, expertise, authoritativeness, and trustworthiness converge to create tools that shape industries and set standards for high-performance manufacturing. Such dedication to excellence fosters trust among stakeholders and drives the evolution of die-casting technology to meet ever-advancing industrial demands.