Die casting and sand casting are two predominant methods in the casting industry, each offering unique advantages and tailored applications. Both processes have carved a niche in manufacturing sectors, powering the production of complex parts across a variety of industries. However, choosing between these two depends largely on specific project needs, including budget, volume, and precision requirements.
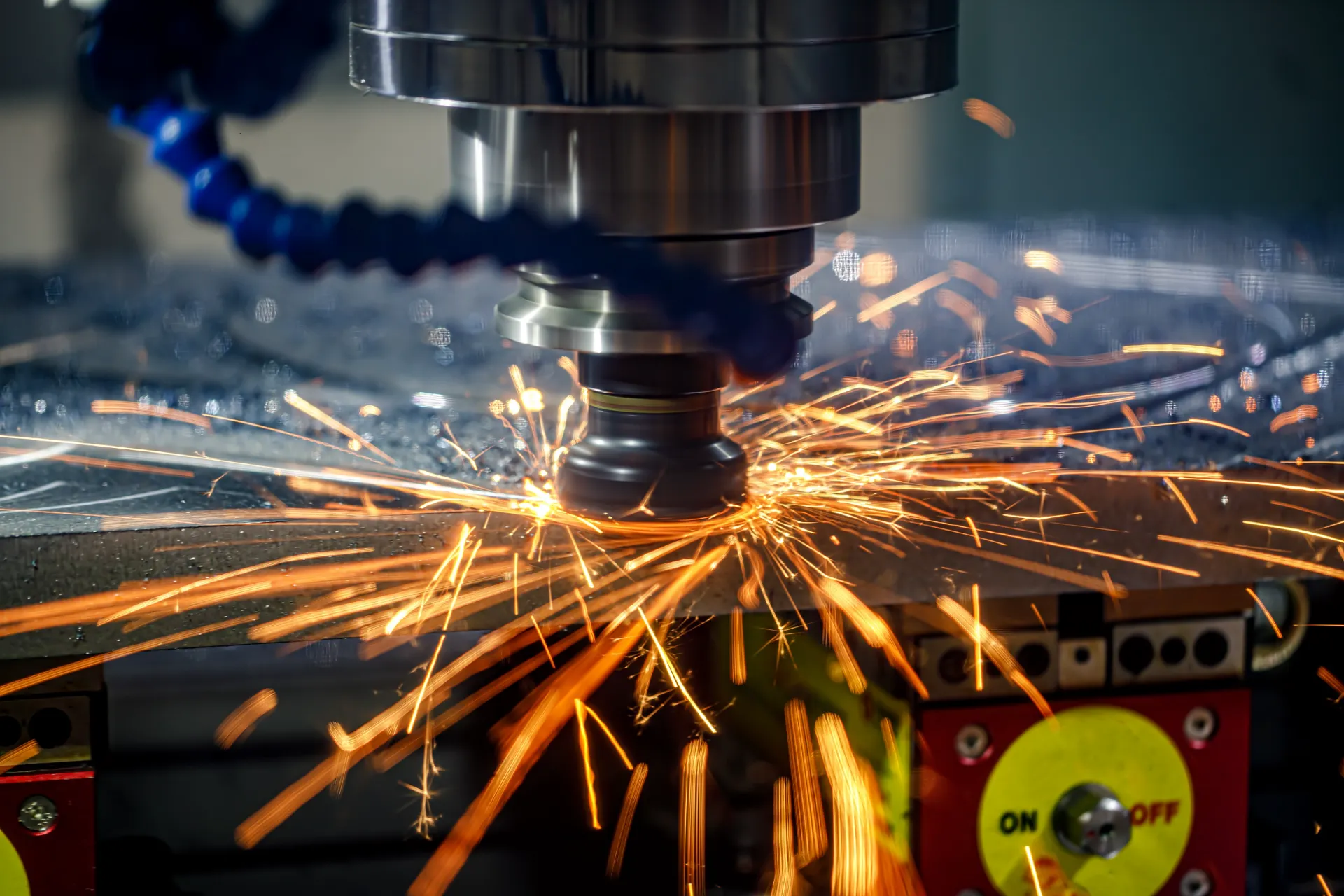
Die casting is renowned for producing highly intricate and precise metal parts. This process involves forcing molten metal under high pressure into a mold cavity. The molds, also called dies, are reusable and made from hardened steel, ensuring durability and consistency across large production volumes. With this method, industries can achieve high dimensional accuracy and smooth finishes, vital for components in automotive, aerospace, and consumer electronics sectors. One critical advantage of die casting is its cost-effectiveness when scaling up to high-volume production. Although the initial mold development can be expensive, the per-unit cost decreases significantly with volume, making it an economical choice for mass production.
In terms of expertise, die casting requires significant knowledge of die design, thermal management, and material properties. The process demands precision in temperature control and timing to avoid defects such as porosity or misalignment. Companies utilizing die casting often invest in advanced technologies and skilled personnel to maintain process efficiency and product quality. Moreover, the industry continues to evolve with innovations such as vacuum-assisted die casting and computerized modeling to enhance performance and accuracy.
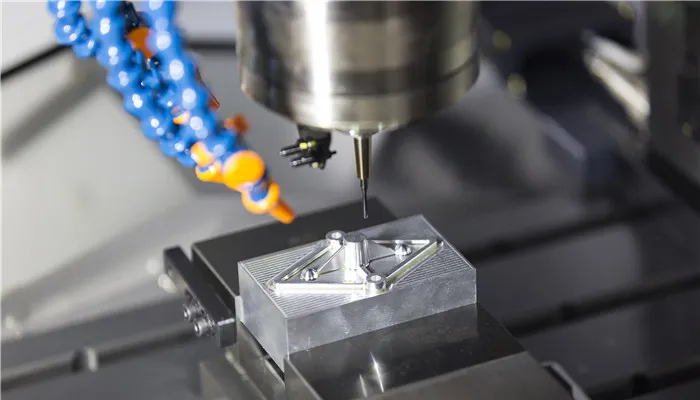
Sand casting, on the other hand, is the elder statesman of manufacturing processes, steeped in historical significance yet evolving with modern technologies. It involves pouring molten metal into a sand mold, which can be customized for each use, allowing immense flexibility. This process is particularly advantageous for producing large and uniquely shaped components, such as those used in heavy machinery and infrastructure projects.
One of the most striking advantages of sand casting is its cost-effectiveness for low-volume production and prototyping. The molds are inexpensive and can be formed rapidly, allowing for quick turnarounds and modifications. It provides an excellent opportunity for industries to test designs without substantial financial commitments. This flexibility extends to material choice as well, accommodating a wide range of metals and alloys.
die casting and sand casting
Sand casting’s expertise lies in understanding mold properties, cooling rates, and material behavior during solidification. Professionals in this field must be adept at designing mold compositions that prevent defects and optimize surface finish and tolerances. Innovations such as 3D-printed molds and core-making advancements have fortified sand casting's relevance in the modern industrial landscape, pushing boundaries in both precision and design complexity.
In upholding trustworthiness and reliability, both methods adhere to rigorous quality standards. Industries incorporate stringent testing regimes, from non-destructive testing to metallurgical inspections, ensuring that every casting meets precise specifications and can withstand functional stresses. The credibility of die and sand casting is further reinforced by their widespread acceptance and continuous improvement over decades, attesting to their foundational role in manufacturing.
The choice between die casting and sand casting ultimately hinges on the specific demands of the project at hand. For projects focusing on large-scale production and fine detail, die casting stands out with its precision and efficiency. Conversely, sand casting shines in the realm of customization and cost-effectiveness for smaller, intricate projects. As industries continue to advance, both die casting and sand casting will likely see further developments and integrations with cutting-edge technologies, promising even greater versatility and application breadth.
As a decision-maker or engineer, understanding the nuances of these processes allows for informed decision-making. It is advisable to work closely with experienced foundries that provide expert guidance and state-of-the-art facilities to bring your project from conception to completion with the highest level of quality and efficiency. The synergistic relationship between human expertise and technological advancements in this domain stands as a testament to the enduring importance of casting in today's manufacturing processes.