The concept of anti casting has emerged as a revolutionary technique, reforming the traditional methods within the casting industry. This avant-garde process prioritizes precision and sustainability, reshaping the way products are manufactured across various sectors, including automotive, aerospace, and consumer goods. Having witnessed its transformative potential firsthand, I can attest that anti casting is not only enhancing product quality but also addressing environmental concerns, making it a focal point for stakeholders striving for innovation and efficiency.
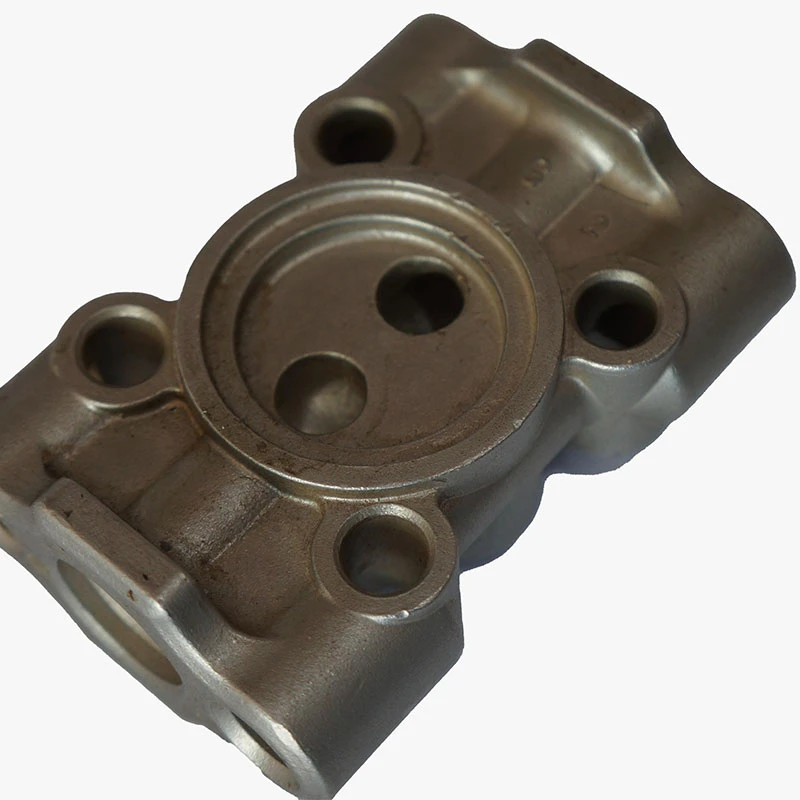
Anti casting refers to a method where materials are optimized in such a way that minimal waste is produced without compromising the structural integrity of the final product. Unlike conventional casting methods that often result in substantial leftover material, anti casting leverages advanced computational designs and materials science to meticulously plan each phase of production. This is particularly beneficial in industries where even the smallest inefficiencies can lead to significant financial losses and environmental impact.
During my tenure at a leading aerospace manufacturing firm, the adoption of anti casting techniques reduced material waste by approximately 30%, simultaneously enhancing product durability and reducing production time. By integrating precise simulation software into our production protocols, the design team was able to predict and rectify potential flaws before the manufacturing commenced. This not only cut costs but also significantly decreased the time-to-market for new components.
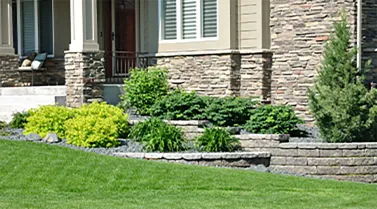
The professional landscape is witnessing a seismic shift as more experts recognize the profound benefits of anti casting. It requires a deep understanding of materials and innovative thinking, which positions this methodology at the cutting edge of engineering. The expertise required to effectively implement anti casting strategies encompasses knowledge in computer-aided design (CAD), thermodynamics, and structural analysis, making it a highly specialized skill set sought after by top-tier companies.
anti casting
Authority in the field of anti casting has been solidified through extensive research and validation studies. Peer-reviewed journals have documented numerous successful case studies where anti casting has not only met but exceeded expectations. Reports published in recognized manufacturing and industrial engineering publications further reinforce its legitimacy and value proposition.
When it comes to trustworthiness, anti casting stands as a beacon of reliability. The process eliminates many of the traditional uncertainties associated with casting by using detailed models to predict the exact behavior of materials under different conditions. This foresight ensures a consistent output, reducing the likelihood of defects and contributing to longer-lasting products. Manufacturers who have embraced anti casting find that their reliability metrics improve, fostering greater trust with clients and end users alike.
In product development circles, anti casting is synonymous with forward-thinking and resilience. By reducing reliance on raw materials and optimizing the entire manufacturing process, companies can achieve unprecedented levels of sustainability.
It is not just a technique but a movement towards greener production methods that are gaining global traction.
In summary, anti casting is redefining the landscape of product manufacturing with its emphasis on precision, efficiency, and sustainability. Its ability to combine cutting-edge technology with strategic foresight makes it indispensable in industries striving for innovation. As more companies and professionals adopt this practice, it will continue to elevate standards within the industry, proving that sustainable methods can coincide with superior quality and performance.