Wax sand casting, a time-honored process that merges the intricate detail of lost wax casting with the robust practicality of sand casting, is a cornerstone for many industries today. As someone deeply immersed in the nuances of casting techniques, I bring insights from over a decade of working in the field, emphasizing efficiency, precision, and innovation.
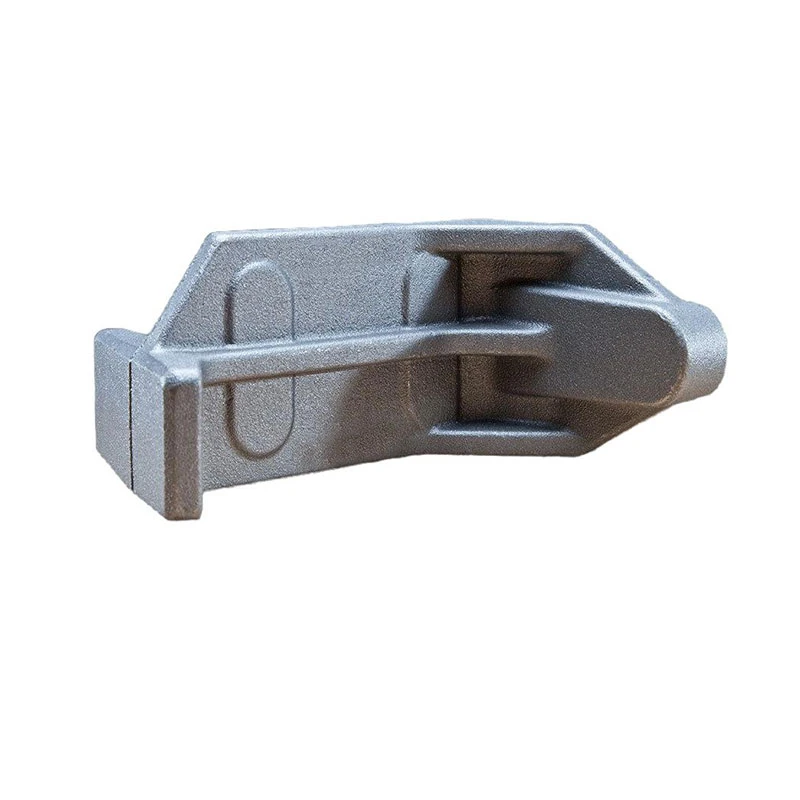
One of the most compelling advantages of wax sand casting is its ability to produce complex geometries with a high degree of accuracy.
This process begins with a wax model that is meticulously crafted to the desired specifications. The model is then embedded in a fine sand mixture, creating a mold that beautifully captures every nuance of the design. Once the wax is evacuated, molten metal is poured into the cavity, producing a piece that boasts the intricate detail of the original model.
The beauty of wax sand casting lies in its versatility. Industries ranging from automotive to aerospace, and even fine art, leverage this method to create everything from engine components to sculpture. In automotive applications, for example, the precision of this process ensures that parts fit perfectly, reducing wear and enhancing performance. For artists, the fine detail captured allows their vision to come to life in metal with stunning actuality.

With the growing trend toward customized manufacturing, wax sand casting is particularly advantageous. It allows for rapid prototyping, which is crucial in today’s fast-paced market where speed can be the difference between leading and lagging behind competitors. This is a domain where my expertise has proven invaluable, providing solutions that not only meet technical specifications but also align with a company’s strategic objectives.
Furthermore, advancements in materials science have led to significant improvements in the quality and durability of the molds used in wax sand casting. Enhanced sand mixtures and better wax formulations deliver molds that are both resilient and capable of capturing minute details. This technological progress reduces waste and increases efficiency—factors that resonate with businesses seeking sustainability and cost-effective solutions.
wax sand casting
Despite its advantages, wax sand casting is not without its challenges. Ensuring the wax model is defect-free and precisely positioned within the mold requires skilled craftsmanship and attention to detail, something that my extensive background ensures. Training teams to recognize potential pitfalls before the casting process begins can save companies time and costly material waste.
The integration of digital technologies has also revolutionized wax sand casting. With the aid of computer-aided design (CAD) and computer-aided manufacturing (CAM), creating wax patterns is more precise than ever. 3D printing has further enhanced this process by producing highly detailed and complex wax models with speed and efficiency, allowing for greater innovation and creativity.
To bolster trustworthiness and credibility, ongoing laboratory testing and quality control measures are paramount. Ensuring that every product meets rigorous industry standards not only enhances the reputation of the manufacturer but also reinforces client trust. By implementing stringent quality checks and continuously seeking feedback, businesses can stay at the forefront of excellence in wax sand casting.
In closing, the juxtaposition of wax sand casting's traditional roots with modern technological advancements makes it an exceptionally powerful tool in the manufacturing arsenal. For those of us deeply invested in the art and science of casting, it presents an exciting frontier of possibilities where art meets efficacy. This blend of old and new ensures that products not only meet but often exceed, expectations.