Stamping parts are an integral component of manufacturing processes across various industries, including automotive, aerospace, electronics, and consumer goods. However, defects in these parts can lead to functional issues, safety concerns, and increased production costs. Understanding the nature of these defects, their causes, and prevention strategies not only enhances production efficiency but also reinforces quality assurance and trustworthiness with clientele.
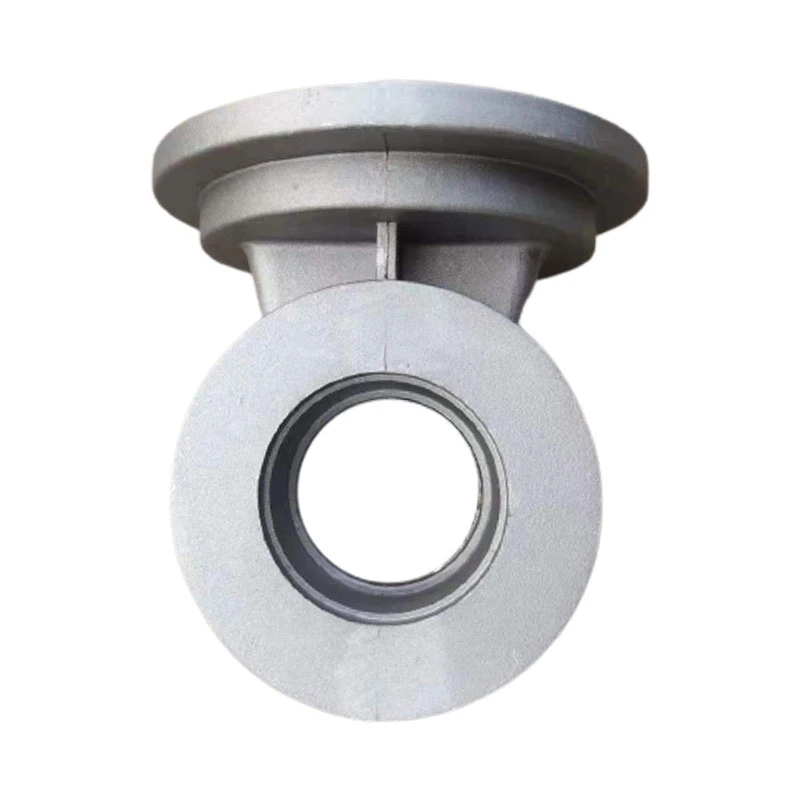
A common defect in stamping parts is surface defects, which can manifest as scratches, dents, or irregular finishes. These imperfections often arise from improper handling during transportation or storage, or due to debris on the stamping equipment itself. Mitigating these issues requires meticulous maintenance routines for machinery and establishing stringent handling protocols to prevent surface contact with hard objects.
Another frequent defect is warping, which results in an uneven surface that can impair the part's performance. Warping often stems from uneven cooling or inappropriate material selection. Addressing this issue involves ensuring consistent cooling processes and selecting materials with suitable thermal properties to withstand the expected range of environmental conditions.
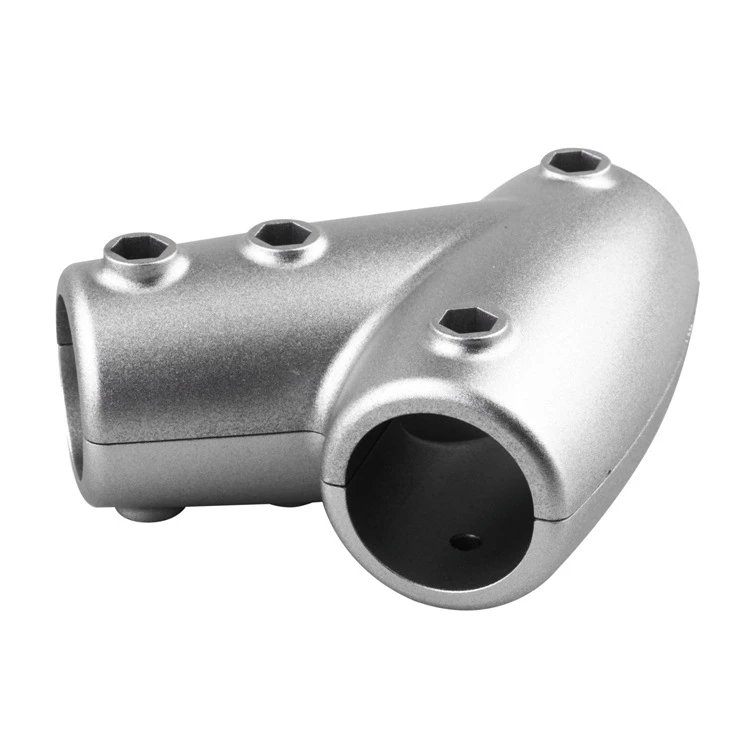
Burrs at the edges of stamped parts present another challenge. These occur when the cutting tool is dull or improperly aligned, leading to excess material protruding from the edge. Regular maintenance of cutting tools and precise calibration are essential to minimize the occurrence of burrs. Furthermore, incorporating a deburring process, either manually or through automated systems, can effectively eliminate these imperfections.
Dimensional inaccuracies are another prevalent defect, where the finished part does not meet the specified size or shape requirements. Such defects are usually caused by tool wear, incorrect press settings, or thermal expansion. Implementing regular tool inspections and calibrations, alongside real-time monitoring systems to track press performance, can significantly reduce dimensional inconsistencies.
Micro-cracks, particularly concerning in industries requiring high strength and durability, can undermine the structural integrity of stamping parts. These cracks often result from excessive stress during the stamping process or from using materials with improper ductility. To combat micro-cracking, it is vital to optimize the stamping process parameters, such as pressure and speed, and to select materials with appropriate mechanical properties for the intended application.
stamping parts defects
Material defects due to poor raw material quality can severely impact the performance of stamped parts. Impurities or inconsistencies in the raw material may lead to weak points that could fail under stress. To ensure material quality, manufacturers should establish rigorous supplier evaluation protocols and conduct thorough inspections upon material delivery.
Preventing defects in stamping parts also involves embracing technological advancements such as CAD software to simulate the stamping process and predict potential defect occurrences. Advanced simulation tools allow manufacturers to optimize tool designs and process parameters before commencing actual production, thus saving time and reducing costs associated with trial-and-error approaches.
Incorporating robust quality control measures is crucial. This includes implementing a comprehensive inspection protocol that utilizes both visual checks and high-precision measurement technologies like laser scanning or coordinate measuring machines (CMMs) to detect deviations from specifications.
Investing in training and development for operators and technicians also plays a critical role in reducing stamping defects. Skilled personnel are more equipped to identify and respond to potential issues early in the production process, maintaining high standards of quality.
By addressing the root causes of stamping parts defects through careful material selection, rigorous process optimization, and advanced technology adoption, manufacturers can enhance the reliability and safety of their products. Ultimately, fostering a culture of quality and continuous improvement not only drives operational excellence but also strengthens trust and authority within the industry ecosystem.