Precision casting components have emerged as a pivotal element in the advancement of various industries, reflecting not only technological progress but also the intricate expertise demanded to create high-quality parts. This casting process, known for its ability to produce complex shapes with high accuracy, plays a crucial role in sectors such as aerospace, automotive, medical, and industrial machinery, among others. At the heart of precision casting lies the lost-wax casting technique, renowned for its ability to reproduce intricate designs and superior surface finishes.
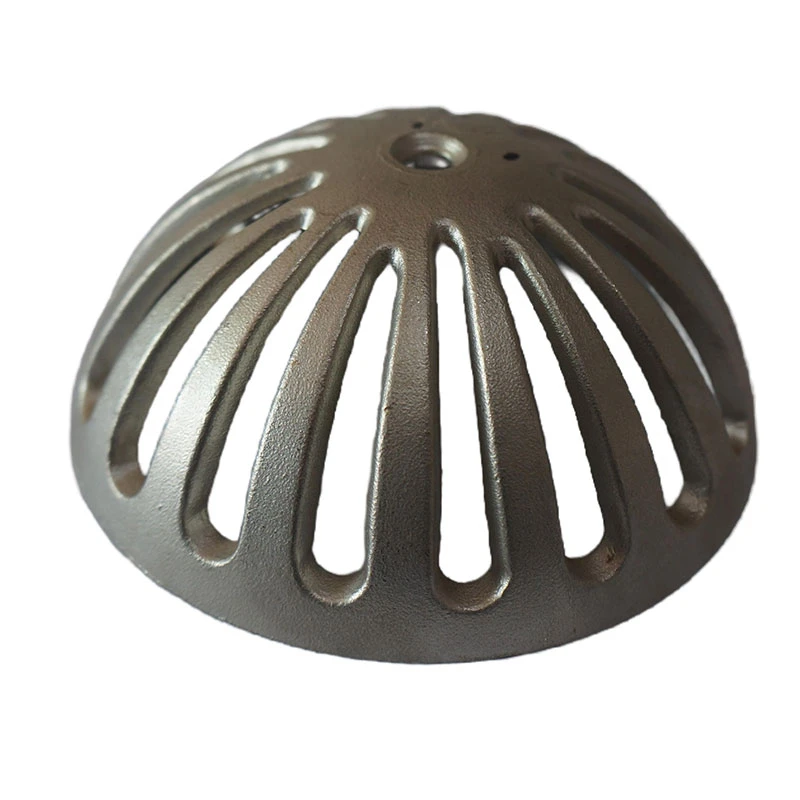
The creation of precision casting components begins with the designing phase, where engineers meticulously draft blueprints tailored to the specific needs of the application. This stage is crucial as it lays the groundwork for producing parts that meet rigorous industry standards. The design includes considerations for functionality, material choice, and dimensional precision, allowing manufacturers to anticipate challenges and address them proactively. This focus on detail underscores the degree of expertise involved in precision casting, where even minor deviations can significantly impact the performance of the final product.
Once the design is perfected, the process transitions to creating wax patterns, which are exact replicas of the desired component. These patterns are assembled into a tree-like structure, accommodating multiple components, before being encased in a ceramic shell. This meticulous process exemplifies the element of trustworthiness, as manufacturers ensure that each pattern and subsequent mold is free from imperfections and capable of withstanding extreme casting conditions without compromise.
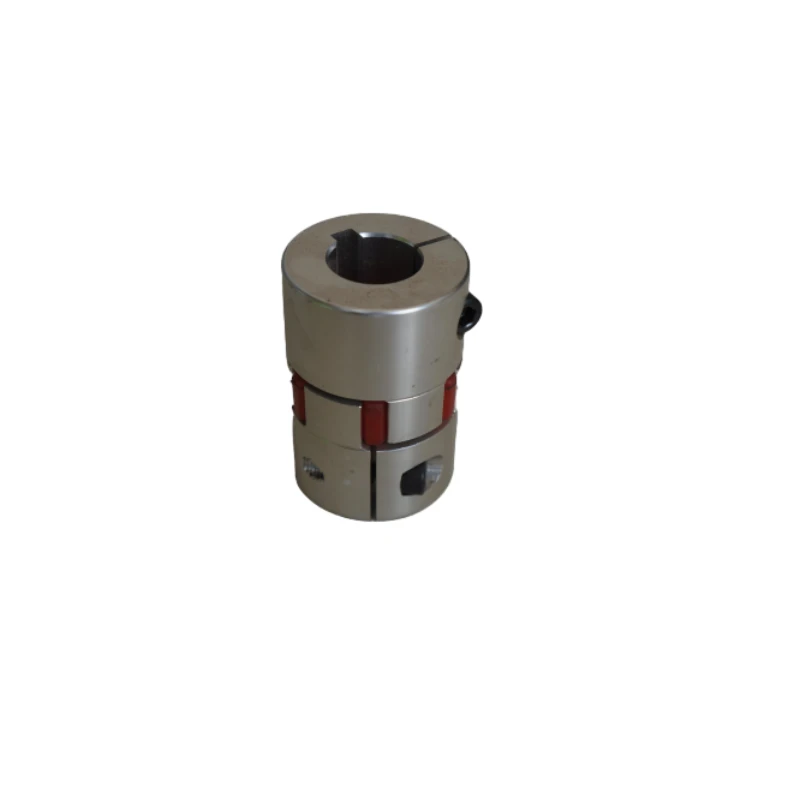
The subsequent step involves melting and removing the wax, followed by pouring molten metal into the resultant mold. This phase demands authoritative control over temperature and timing, reflecting a deep-seated expertise in metallurgical sciences. The cooling phase must be carefully managed to prevent defects such as shrinkage or porosity, thereby ensuring each component emerges with a uniform and defect-free composition. Such stringent control over variable parameters highlights the specialized knowledge and authoritative control manufacturers wield over the casting process, reinforcing their reliability as producers of precision components.
precision casting components
After cooling, the ceramic shell is broken away to reveal the rough casting. However, the journey to a finished product doesn't stop there. These components undergo rigorous finishing operations, which include cutting, grinding, and polishing. Such processes ensure that every component meets the tight tolerances required by high-spec applications. The attention to detail at this stage exemplifies the experience embedded within the manufacturing team, where accumulated knowledge leads to the creation of reliable and sustainable components that surpass industry expectations.
Furthermore, precision casting components are subject to strict quality inspection protocols. This stage involves non-destructive testing techniques such as X-ray inspection, ultrasonic testing, and dye penetrant inspection, each chosen to verify the internal and external integrity of the components. Manufacturers often correlate their findings with predefined standards and certifications, fortifying the authority and trustworthiness of their products. Customers rely on this assurance, knowing each component has undergone extensive validation processes to ensure safety and effectiveness in its intended application.
The evolution of precision casting components is a testament to the continual advancements in the field of metallurgy and engineering. With increasing demands for miniature and more complex parts, manufacturers are compelled to push the boundaries of what is possible, often turning to innovate casting materials and techniques. This relentless pursuit of excellence not only enhances the performance of the finished components but also solidifies the manufacturers' standing as experts in their field.
Precision casting components, therefore, represent the epitome of engineering innovation and operational excellence. By blending experience, expertise, authoritativeness, and trustworthiness, manufacturers deliver products that not only meet but exceed the rigorous demands of modern industries, securing their position as invaluable partners in technological advancement. Companies reliant on these components can rest assured knowing they have invested in components that offer unparalleled performance, reliability, and longevity.