Magnesium Sand Casting Unveiling the Art and Science Behind Precision Casting
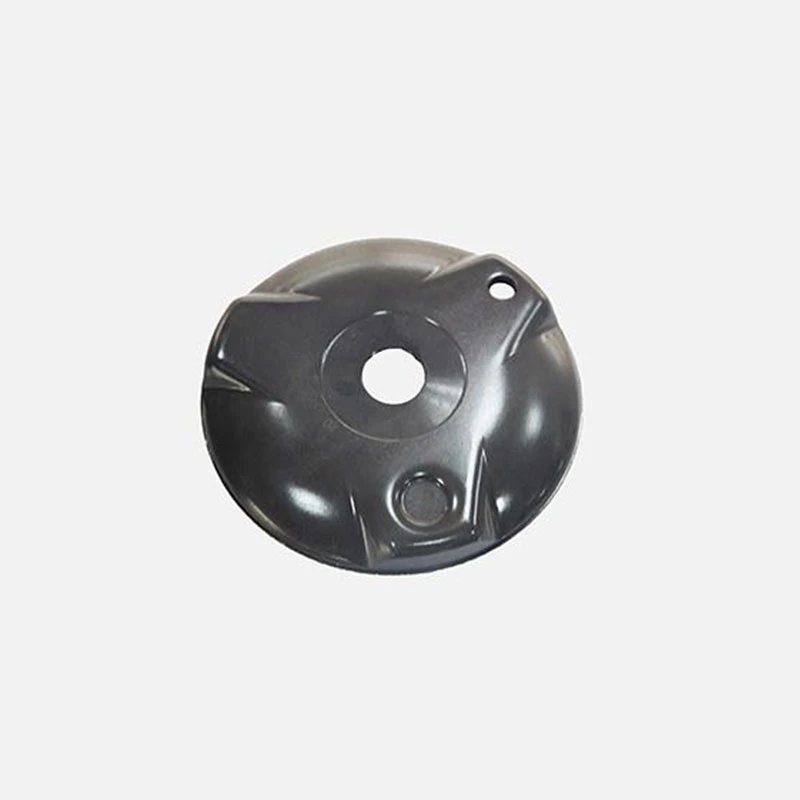
The world of metal casting, dominated by various materials, techniques, and methodologies, finds a unique ally in magnesium. Meticulously tailored to specific industrial needs, magnesium sand casting stands as a pinnacle of precision. This technique not only capitalizes on magnesium’s lightweight nature and excellent strength-to-weight ratio but also integrates artistry and engineering prowess, making it an unrivaled choice for intricate metal casting projects.
Understanding Magnesium’s Unique Properties

Magnesium, often lauded as the lightest structural metal available on the earth, has a density that is two-thirds that of aluminum. Its advantageous characteristics encompass excellent machinability, high thermal capacity, and a natural propensity for vibration dampening. These attributes make magnesium an ideal choice for several sectors including the automotive, aerospace, electronics, and medical industries. However, it is in sand casting that magnesium truly demonstrates its mettle, allowing manufacturers to produce complex shapes with precision.
The Science Behind Magnesium Sand Casting
Sand casting, a process with origins tracing back to ancient civilizations, finds its modern-day sophistication through magnesium. The procedure initiates with creating a mold cavity, customarily using moistened sand packed around patterns that replicate the cast's final form. When the sand hardens, it forms a negative impression—essentially a sculpture’s counterpart. After removing the pattern,
molten magnesium is poured into the mold cavity.
Magnesium’s relatively low melting point and fluidity during the molten phase facilitate the production of intricate designs that other materials often struggle to replicate. The cooling phase, scientifically termed solidification, is meticulously controlled to maintain magnesium's desirable microstructural properties. The resultant products are subsequently released from their sand bellies, unveiling structures that are lightweight yet robust, highlighting the craftsmanship of magnesium casting.
Applications Propelling Industries Forward
In the automotive industry, magnesium sand casting is revolutionizing structural and non-structural components. Engine blocks, transmission cases, and even intricate dashboard frames are now routinely crafted from magnesium owing to their lightweight, which significantly contributes to better fuel efficiency. The aerospace sector benefits similarly; magnesium’s use in crafting ribbed components and housings illustrates the metal’s capability to withstand rigorous conditions while optimizing aircraft weight.
Moreover, in consumer electronics, magnesium’s excellent electromagnetic interference shielding makes it invaluable. It’s no wonder that laptops and cameras, especially those requiring robust yet lightweight casings, often incorporate magnesium components derived from the precision of sand casting.
magnesium sand casting
Expert Insights and Best Practices
For manufacturers contemplating magnesium sand casting, collaboration with experts in the field unlocks potential unmatched by traditional methods. Experts emphasize the importance of understanding the nuances of magnesium’s reactivity. Protective atmospheres during the casting process mitigate risks like oxidation, and employing technologies such as thermal analysis optimizes the solidification phase.
Further, investing in training operators on the unique aspects of handling magnesium, such as safe pouring and mold maintenance, ensures the production of high-quality castings consistently. Manufacturers have witnessed up to a 30% cost reduction in material wastage by leveraging these specialized practices, aligning economic and environmental efficiency.
Authoritativeness and Sustainability
The rising popularity of magnesium sand casting is supported by comprehensive studies and publications from authoritative bodies such as the American Foundry Society and the Magnesium Association. Their research underscores the strategy of combining magnesium’s inherent qualities with advanced sand casting techniques to foster innovation.
Furthermore, the sustainable cycle of magnesium sand casting remains a crucial element for industries striving to reduce their carbon footprint. The reusability of sand, coupled with magnesium’s recyclable nature, underpins a process that prioritizes sustainable manufacturing practices without compromising the quality and strength of the output. Such initiatives resonate with industry leaders committed to ecological responsibility.
Trusting Magnesium for the Future
A testimonial collected from an automotive industry veteran aptly describes magnesium sand casting as a “transformational approach that blends lightweight strength with design flexibility.” These sentiments bolster the trust placed in this process, revered not only for its technical advantages but also its reliability.
In conclusion, as industries continually evolve and demand lightweight, strong, and intricate parts, magnesium sand casting emerges as a formidable solution. Its blend of ancient techniques with modern-day technology speaks volumes about its power to shape the future of manufacturing—where precision engineering and innovative materials meet to forge possibilities once deemed the domain of imagination.