Low pressure casting represents a pivotal technique in the manufacturing sector, primarily known for its ability to produce high-quality metal components with significant structural integrity and precision. This process plays a critical role in various industries such as automotive, aerospace, and electronics, offering both economic and production advantages.
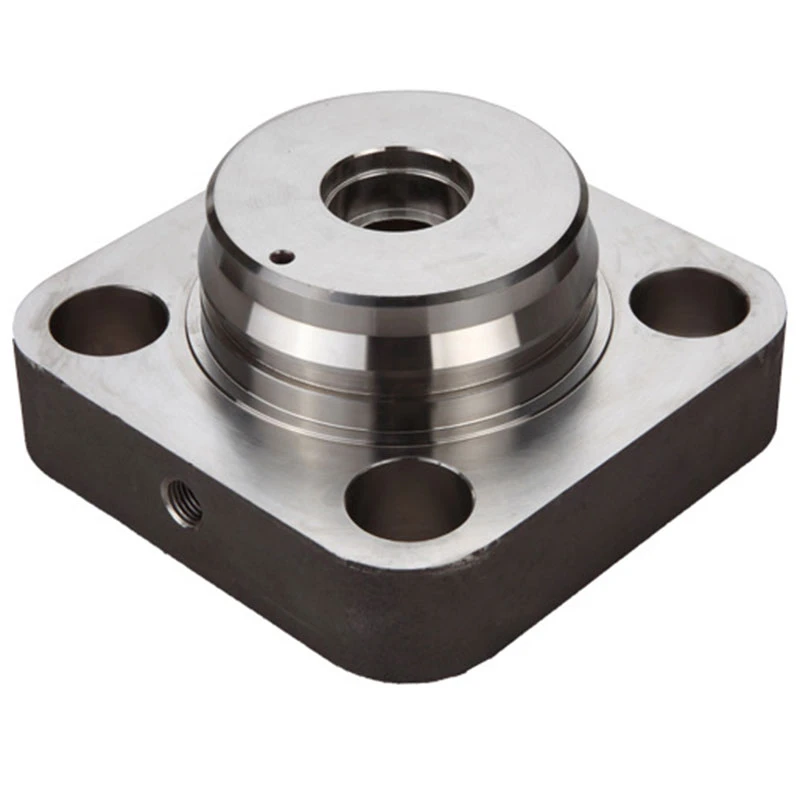
Low pressure casting involves injecting molten metal into a mold under low pressure, allowing for precise control over the flow and solidification of the material. Unlike traditional methods, low pressure casting significantly reduces turbulence, minimizing the formation of oxides and defects in the final product. This method ensures that the cast components exhibit excellent surface finish and dimensional accuracy by promoting a smooth metal flow and controlled solidification.
One of the hallmark experiences associated with low pressure casting is its capacity to manufacture thin-walled parts with complex geometries. This is particularly advantageous in the automotive industry, where weight reduction without compromising on strength is a constant pursuit. For example, automotive manufacturers have reported substantial improvements in fuel efficiency by switching from traditional casting methods to low pressure casting, enabling the production of lighter, yet equally robust, engine components and chassis parts.
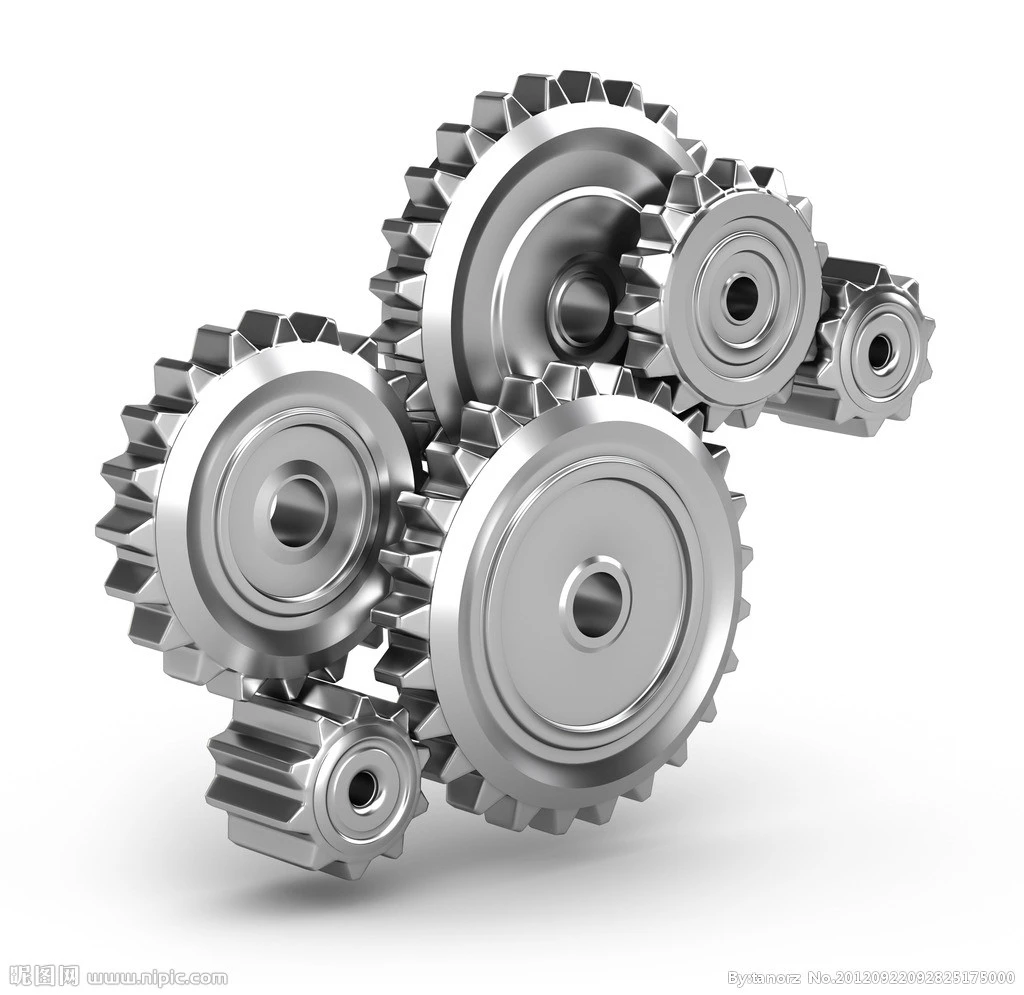
From an expertise perspective, low pressure casting requires a deep understanding of material properties and thermal dynamics. Operators need to maintain precise control over temperature and pressure to ensure that the metal fills the mold completely and uniformly. Using advanced computer simulations in the casting process enhances predictability and reduces the time for iterative testing. Simulation tools help in anticipating how the molten metal will fill the mold, solidify, and contract, allowing engineers to adjust mold designs proactively and thus minimize wastage and enhance overall efficiency.
Regarding authoritativeness, the advancements in low pressure casting benefit from continuous research and development. Leading technical conferences and journals regularly discuss innovations in the alloy compositions used in low pressure casting to optimize material properties like tensile strength, ductility, and wear resistance. Commitment to rigorous research standards and international collaborations has positioned it as a highly respected process in metallurgy and industrial manufacturing.
low pressure casting
Trustworthiness in low pressure casting is enhanced by the stringent quality assurance protocols that govern the process. Regular audits, material testing, and adherence to global standards such as ISO and ASTM ensure the reliability of the cast products. Manufacturers often employ non-destructive testing methods, such as X-ray and ultrasonic inspections, to verify internal consistency and detect potential defects even in the most intricate parts. Ensuring that products meet and exceed safety requirements builds confidence in end-users and makes low pressure casting a preferred choice for critical applications.
In terms of products, low pressure casting is prominently utilized for producing aluminum and magnesium components, offering a favorable strength-to-weight ratio critical in high-performance vehicles and aerospace applications. The process's ability to mold intricate features makes it invaluable for consumer electronics, where miniaturization without losing performance is vital. The production of thin-walled die-cast components achieves the dimensional precision required in modern smartphones and laptops.
The global shift towards sustainability has also highlighted the environmental benefits of low pressure casting. By improving yield rates and reducing material wastage, this process aligns with eco-friendly production practices. Many leading manufacturers are investing in recycling initiatives, utilizing excess metal and scrap to develop new components without compromising quality. This not only supports sustainable manufacturing but also drives down production costs by maximizing material utilization.
Across industries, the demand for high-performance, lightweight components is surging, and low pressure casting stands out as a technology that meets these demands efficiently. With continuous advancements and a robust framework supporting innovation, the position of low pressure casting in industrial production is set to grow. The technology fosters a synergy between precision engineering and sustainable practices,
ensuring its key role in the future of manufacturing.