Integrated die casting is revolutionizing the manufacturing landscape, offering a sophisticated approach to producing complex metal parts with remarkable precision and efficiency. This advanced technique is gaining traction across various industries, setting new standards for quality and performance. By integrating multiple processes into a single step, integrated die casting minimizes production time and costs, while improving the structural integrity of components.
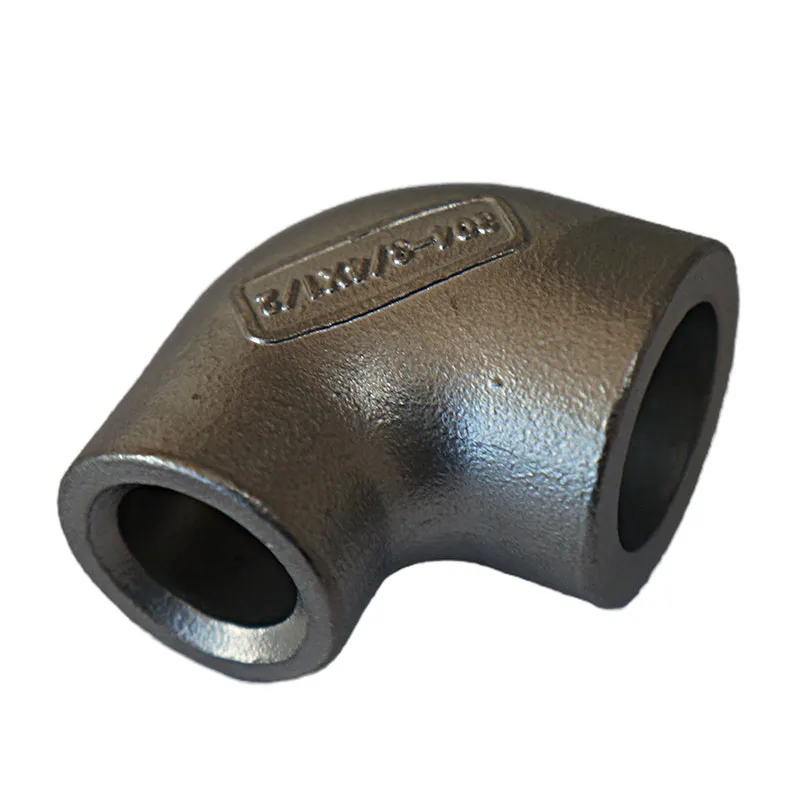
Experience shows that companies leveraging integrated die casting benefit from a significant reduction in material waste. Traditional methods often result in excessive scrap, but integrated die casting optimizes material usage by combining assembly processes. For instance, manufacturers have reported a reduction in material waste by as much as 40%, leading to a more sustainable production model. This not only enhances the environmental profile of the products but also results in considerable cost savings, which can be passed on to consumers.
A testament to the expertise required in integrated die casting is the precision involved in creating intricate components. Engineers who specialize in this field possess a profound understanding of material properties and thermal dynamics.
The expertise in modeling and simulating the die casting process is crucial to achieving desired outcomes. This level of specialization ensures that components meet stringent industry standards, such as those in the automotive and aerospace sectors, where reliability and performance are critical.
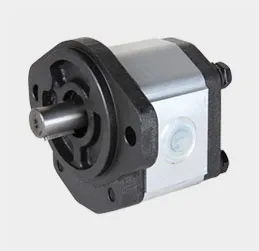
Furthermore, integrated die casting offers unparalleled authoritativeness in matters of component durability and performance. By eliminating the need for multiple assembly stages, potential points of failure are reduced, resulting in a more robust product. Industries such as automotive and electronics increasingly rely on this methodology to enhance the longevity of their products. Studies have demonstrated that products manufactured with integrated die casting techniques exhibit superior mechanical properties, including enhanced tensile strength and fatigue resistance.
integrated die casting
Trustworthiness is a crucial component of the integrated die casting process, underpinned by rigorous quality assurance protocols. From the selection of raw materials to the final inspection of finished goods, each stage of the process is meticulously controlled to ensure consistency and reliability. Manufacturers employ advanced non-destructive testing techniques, such as X-ray and ultrasonic evaluations, to verify the structural integrity of their products. This commitment to quality reassures clients and end-users of the dependability of components produced through integrated die casting.
Exploring the benefits of integrated die casting, it becomes apparent that this technique also promotes innovation in design. Engineers are no longer constrained by the limitations of traditional manufacturing methods, allowing for the creation of complex geometries that were previously unattainable. This newfound freedom is particularly advantageous in industries that demand lightweight yet strong components, such as the medical and consumer electronics sectors. By optimizing the design and reducing the overall weight, the performance and efficiency of the final product are significantly enhanced.
Moreover, integrated die casting streamlines supply chains by consolidating multiple production steps. This simplification reduces lead times and enhances responsiveness to market demands. Companies that have adopted this methodology report improved agility in meeting customer requirements, which is crucial in today’s fast-paced market environment. The ability to quickly adapt and innovate gives businesses a competitive edge, allowing them to capture market share and expand their product offerings more effectively.
In conclusion, integrated die casting is ushering in a new era of manufacturing efficiency and precision. By significantly reducing waste, enhancing component performance, and fostering design innovation, it offers a comprehensive solution for industries striving to meet the demands of modern production. As more companies recognize the advantages of integrating die casting into their manufacturing processes, the potential for innovation and improvement in product quality continues to grow. This technique not only enhances the final product but also contributes to a more sustainable and efficient manufacturing ecosystem.