Engineered precision casting stands as a cornerstone in the world of manufacturing, owing to its remarkable capabilities and unrivaled precision. This technique, crucial to several industries, involves creating complex metal parts by pouring molten alloys into meticulously designed molds. Through this method, manufacturers achieve not only accuracy but also an impressive level of detail that other casting techniques often cannot match.

Real-life experiences highlight the myriad benefits of engineered precision casting. An aerospace company, for example, might rely on this process to craft turbine blades with intricate geometries that ensure optimal performance in extreme conditions. This level of exactness is only possible because the precision casting process involves detailed planning and execution. This includes careful temperature control of the molten metal and the use of high-quality raw materials, which together ensure the structural integrity of each component.
From a professional standpoint, expertise in engineered precision casting requires a deep understanding of both the technical and material sciences. Metallurgists and engineers work hand-in-hand to develop alloys that meet specific stress, corrosion resistance, and thermal demands. By consistently focusing on these aspects, experts ensure that each casting maintains the highest standards of durability and reliability, a critical factor in sectors like automotive and medical devices where failure is not an option.
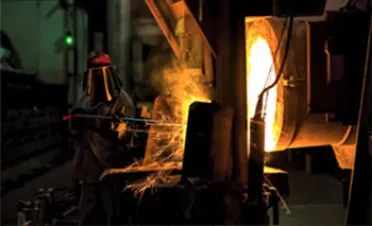
The authoritativeness of engineered precision casting is evident in its historical evolution and widespread application. Industries ranging from aerospace to oil and gas leverage this method for products where failure could result in catastrophic consequences. Regulatory bodies often set stringent standards governing the quality of cast components, a testament to the critical role this process plays in ensuring safety and performance.
Trustworthiness in engineered precision casting is established through rigorous testing and quality assurance. Non-destructive testing methods such as X-ray and ultrasonic inspections are routinely employed to verify that the castings lack defects or impurities that could compromise their performance. Furthermore, the industry's commitment to adhering to stringent international standards underscores the reliability of the components produced.
engineered precision casting
In terms of product excellence, engineered precision casting offers unparalleled versatility. This process is employed to produce a diverse array of components, from small intricate elements like dental implants to massive parts like aircraft engine casings. The ability to produce complex geometries without necessitating expensive and time-consuming machining post-casting gives manufacturers a significant competitive advantage.
Moreover, the sustainability aspect of engineered precision casting cannot be overstated. The ability to utilize advanced alloys and achieve precise tolerances means less material wastage. It also opens doors to recycling and reusing materials—a critical advantage in today's environmentally conscious manufacturing landscape.
The future of engineered precision casting is promising, with technological advancements paving the way for even greater innovations. The integration of computer-aided engineering and simulation tools into the casting process allows manufacturers to predict and optimize the performance of castings before production. These advancements not only improve efficiency but also lead to the development of superior products that consistently meet or exceed customer expectations.
In summary, engineered precision casting represents a blend of time-tested techniques and modern innovation, ensuring that it remains an indispensable process in the manufacturing sector.
It is not merely a method of production but a strategic asset that delivers unmatched precision, reliability, and sustainability. This technique continues to shape the future of manufacturing, driving industries forward with components that support high-stakes performances and sustainable practices.