Understanding the intricate dynamics of die casting enclosures is crucial for businesses seeking robust, reliable, and efficient product housing solutions. Die casting, a manufacturing process that involves injecting molten metal into a mold cavity under high pressure, has revolutionized enclosure production by offering superior precision and consistency over other manufacturing methods.
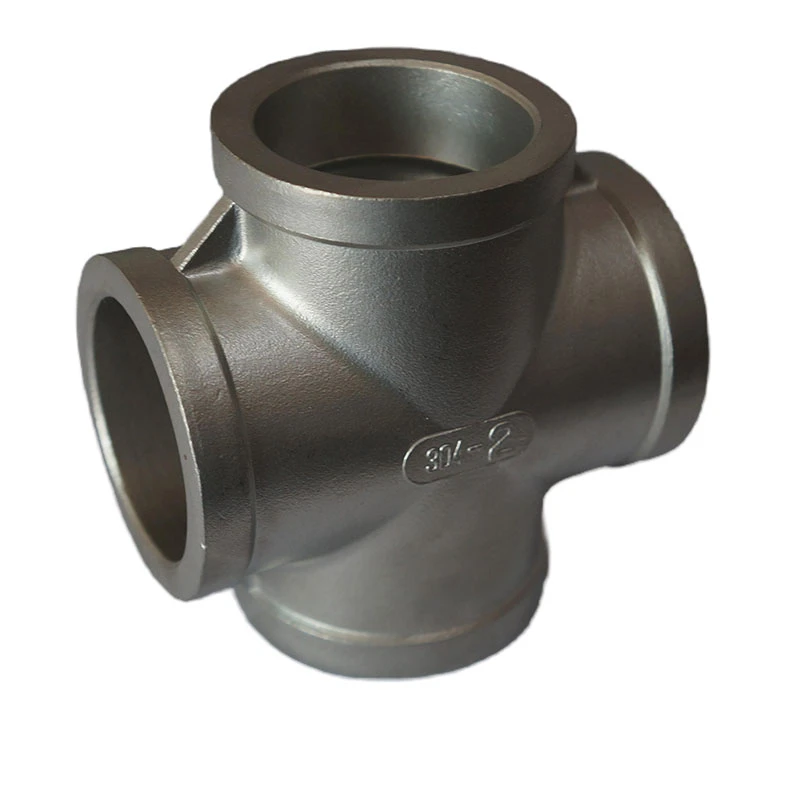
Firstly, die casting enclosures boast an unmatched level of accuracy and consistency, essential for housings that need to accommodate sensitive electronic components. The precision achieved with this method surpasses that of sand or gravity casting, resulting in tighter tolerances and smoother finishes. These attributes are particularly beneficial for industries like automotive, aerospace, and consumer electronics, where component integrity cannot be compromised.
In terms of material selection,
die casting excels due to the versatility it offers. Metals such as aluminum, zinc, and magnesium are popular choices in this domain. Aluminum stands out for its strength-to-weight ratio and corrosion resistance, making it ideal for durable enclosures used in harsh environments. Zinc, on the other hand, provides excellent ductility and impact endurance, often preferred for enclosures requiring substantial structural integrity.
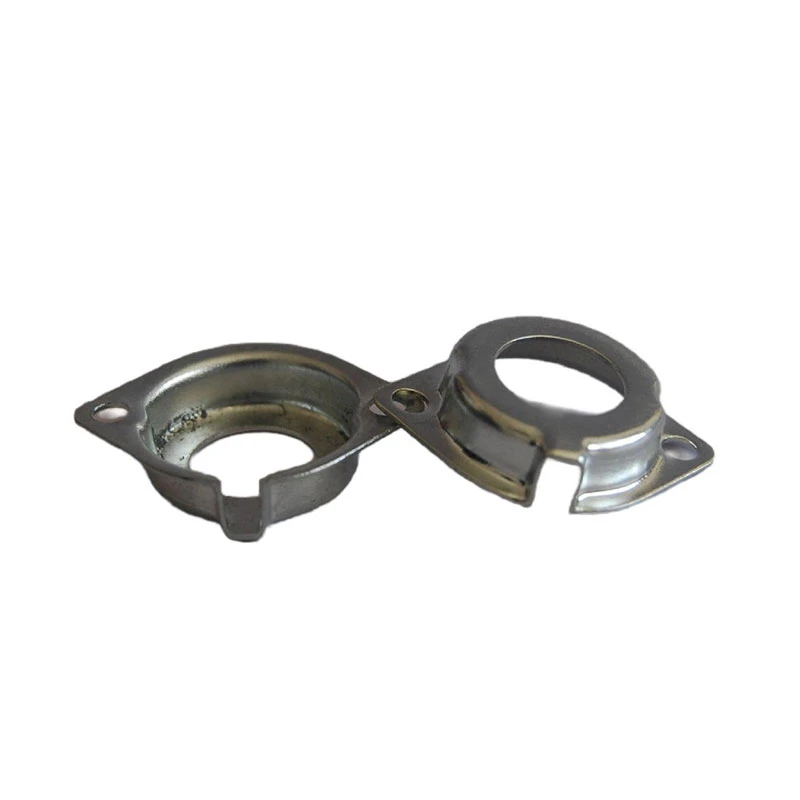
One of the paramount factors enhancing the attractiveness of die casting enclosures is the efficiency it brings to the production process. This method enables rapid production rates, which can significantly reduce lead times—a critical advantage in today’s fast-paced market that demands swift product turnaround. The ability to mass-produce components with little to no secondary processing further ensures cost-effectiveness, a vital consideration for any competitive business.
Expertise in engineering custom die casting enclosures allows for tailored solutions that meet specific application requirements. Professionals in this field capitalize on advanced simulation software to predict and rectify potential defects, such as porosity or warping, before the actual manufacturing process begins. By meticulously refining every aspect of the design and production stages, experts ensure that each enclosure not only meets but often exceeds industry standards for performance and durability.
die casting enclosure
Trustworthiness and reliability stem from adherence to rigorous quality control procedures throughout the die casting process. From initial design to final inspection, a commitment to stringent testing standards guarantees every enclosure is fit for purpose. Critical assessments, such as X-ray inspections and pressure leakage tests, are routinely performed to validate structural integrity and ensure enclosures can withstand operational demands without failure.
Furthermore, incorporating sustainability into the production and lifecycle of die casting enclosures aligns with modern environmental consciousness. The metals used in die casting are not only recyclable but can also be reprocessed without degradation to their properties, promoting a circular economy. This sustainable approach not only reduces environmental impact but can also enhance a company’s brand reputation, reflecting a commitment to eco-friendly manufacturing practices.
Finally, when considering the importance of supplier selection in acquiring die casting enclosures, businesses should prioritize partners with a proven track record in innovation and industry compliance. Collaborating with manufacturers that possess certifications such as ISO 9001 or IATF 16949 assures adherence to global quality standards, fostering confidence that the enclosures will perform reliably in their intended applications.
In conclusion, the application of die casting technology for enclosure manufacturing offers exceptional advantages in precision, efficiency, and reliability. By leveraging expert design capabilities and stringent quality controls, businesses can ensure their enclosures meet the high standards necessary to protect delicate internals while conforming to cost-effective and sustainable production practices. With the rise of customized solutions, companies are now better equipped than ever to achieve excellence in their product housing endeavors.